Estimated reading time: 5 minutes
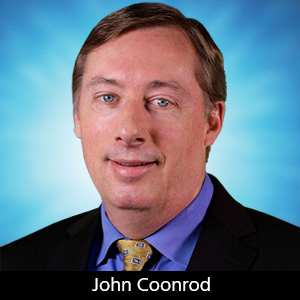
Should You Use a High-Frequency Laminate Instead of FR-4?
Editor's Note: This article originally appeared in the June issue of The PCB Magazine.
Epoxy-based FR-4 circuit board materials are popular for a wide range of electronics applications, and for good reason. These low cost, glass-reinforced substrates are reliable, with well-understood mechanical and electrical characteristics. They are used in everything from audio circuits to microwave designs. However, they are not the answer for every circuit, especially for a wide range of high-frequency designs, and for several reasons.
When trying to decide between FR-4 or a high-frequency laminate, the lower cost of FR-4 may be important, but it may not be the only consideration. For example, how critical is signal loss to your design? In most passive circuits, such as filters, loss increases as frequency increases. FR-4 has a higher dissipation factor (Df) than laminates engineered for high-frequency use, and circuits fabricated on FR-4 will suffer higher losses than similar circuits formed on a high-frequency circuit. Typical values are about 0.020 for FR-4 and about 0.004 for a high-frequency laminate, or a dissipation factor that is about one-fourth that of FR-4. This translates into a meaningful difference in insertion loss between the two circuit-board materials. Some designs can tolerate a certain amount of loss, but it will depend upon the loss budget for a given project.
Another factor to consider when trying to choose between FR-4 and a high-frequency laminate is how those losses occur. Are they evenly distributed across the frequency band of operation? FR-4 is characterized by a Df that increases steadily with frequency, so as frequency rises, insertion loss increases. High-frequency laminates typically exhibit a more stable Df characteristic with frequency, with considerably less loss at higher frequencies. Figure 1 shows a comparison of insertion loss for simple microstrip circuits made on different materials of the same thickness.
Figure 1: Insertion loss comparisons for microstrip circuits using different materials.
Stable impedance is important to many designs, and this is another area where FR-4 and high-frequency laminates can deliver much different results. Stable impedance depends on maintaining a stable dielectric constant (Dk) across the length and width of a substrate, including as temperature changes. While they are low in cost, FR-4 materials can suffer relatively wide variations in Dk across the length and width of a circuit board, and with temperature. This can make it impossible, for example, to achieve flat amplitude response with frequency in an amplifier. High-frequency laminates, on the other hand, provide a Dk that remains constant across the length and width of a board. This means more predictable performance in large circuits and more repeatable performance in multiple similar circuits formed from the same board.
For designs that must perform over temperature, FR-4 and high-frequency laminates can also provide very different results. To evaluate performance variations with temperature, circuit-board materials are characterized by the thermal coefficient of dielectric constant (TCDk). It is simply a measure of how much the dielectric constant changes over a defined temperature range. For FR-4, it is typically 200 parts per million (ppm) per degree Celsius (°C) change in temperature. While that might seem like a small number, it can result in large variations over a wide temperature range. Compare it to about 40 ppm/°C for high-frequency laminates, a much smaller number resulting in much less variations with temperature. If a circuit must work with little variation over a wide temperature range, a high-frequency laminate is probably a better choice than FR-4. Comparisons of different circuit materials are shown in Figure 2, regarding TCDk.
Figure 2: TCDk curves for several high frequency laminates as well as FR-4 (Epoxy/WG).
Sometimes, the very value of a circuit board’s Dk can play an important part in choosing a particular material. In a wavelength-dependent circuit, such as an RF or microwave design, the value of the dielectric constant will impact the size of the circuit’s transmission lines, and thus the size of the circuit. Simply put, circuit-board materials with higher Dk values can yield smaller circuits. If the size of a circuit is important, then the value of the Dk should be part of the decision process in choosing a circuit-board material. FR-4 typically has a Dk of about 4.5. That’s higher than most PTFE high-frequency materials, but lower than a number of high-frequency laminates which offer Dk values of 6.15, and even as high as 11.0. Using materials with these higher values can shave 25% or more off the size of a circuit built on FR-4. A typical example of the miniaturization of a microstrip filter circuit element is shown in Figure 3.
Figure 3: Example of possible circuit size reduction due to using a substrate with a higher dielectric constant.
There are several other factors to consider when deciding between FR-4 and a high-frequency laminate, including the type of operating environment and the power/thermal requirements. For circuits where moisture might be a problem, for example, most high-frequency laminates have much lower moisture absorption than FR-4, which can be critical in outdoor applications. Also, high-frequency thermoset-based laminates may be more thermally robust than FR-4, and better able to handle the high temperatures of lead-free soldering processes.
What is the best way to decide if your project might work better with a high-frequency laminate than with FR-4? Size up the electrical and mechanical requirements for the job, and see how they might be handled, first by FR-4 and then using a high-frequency laminate. For ease of comparison, data sheets are readily available for both types of circuit-board materials and provide the key facts on electrical and mechanical parameters and tolerances. If the mechanical and electrical variations of FR-4 are too wide for your application, consider paying a bit more for a high-frequency laminate, but with much improved performance and reliability. In the end, the higher yields from using a dielectric material with tighter manufacturing tolerances, such as RO4000® thermoset substrates, might even mean lower production costs than when using FR-4.
RO3000, RO3035, RO4000, RO4350B and LoPro are licensed trademarks of Rogers Corporation.
John Coonrod is a Market Development Engineer for Rogers Corporation, Advanced Circuit Materials Division. He has more than 24 years experience in the PCB industry, about half of which in the flexible printed circuit board industry doing circuit design, applications, processing and materials engineering. John has also supported the high-frequency rigid printed circuit board materials made by Rogers for the past 10 years. Reach John at john.coonrod@rogerscorporation.com.
More Columns from Lightning Speed Laminates
Lightning Speed Laminates: Millimeter-wave Properties and PCB Design ChallengesLightning Speed Laminates: Optimizing Thermal Management for Wireless Communication Systems
Lightning Speed Laminates: Test Vehicles for PCB Electrical Material Characterization
Lightning Speed Laminates: Optimum Thermal Stability Considerations
Lightning Speed Laminates: Thermal Management Isn’t Getting Easier
Lightning Speed Laminates: Benefits of High-Performance Hybrid Multilayer PCBs
Lightning Speed Laminates: An Overview of Copper Foils
Lightning Speed Laminates: The Importance of Circuit Features for Millimeter-Wave Applications