-
- News
- Books
Featured Books
- design007 Magazine
Latest Issues
Current IssueProper Floor Planning
Floor planning decisions can make or break performance, manufacturability, and timelines. This month’s contributors weigh in with their best practices for proper floor planning and specific strategies to get it right.
Showing Some Constraint
A strong design constraint strategy carefully balances a wide range of electrical and manufacturing trade-offs. This month, we explore the key requirements, common challenges, and best practices behind building an effective constraint strategy.
All About That Route
Most designers favor manual routing, but today's interactive autorouters may be changing designers' minds by allowing users more direct control. In this issue, our expert contributors discuss a variety of manual and autorouting strategies.
- Articles
- Columns
- Links
- Media kit
||| MENU - design007 Magazine
Estimated reading time: 9 minutes
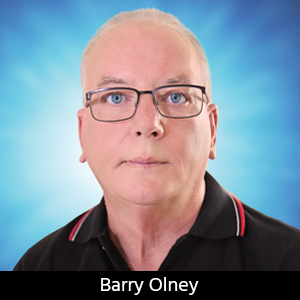
Beyond Design: Pre-Layout Simulation
Pre-layout simulation results for an address line shown in Figure 6 include the effect of a 22-ohm series terminator near the driver, and a 200-ohm pull-up at the end of the line to VTT (0.9V). The VTT pull-up is typically between 100 – 200 ohm and is determined by simulation.
Figure 6. Pre-layout address simulation results (MA0).
Establishing Routing Rules
Before starting placement and routing, detailed interconnect-routing constraints should be established. These are of course based on the pre-layout simulation. The matched length data, address, strobe/clocks, command and control signals should be setup in the constraints editor, along with differential pair rules, clearance between signal groups (to prevent crosstalk) giving priority to critical signals. Furthermore, return paths should be checked to ensure that there are no split planes or obstacles to delay the return current. Further details of the tolerances required are highlighted in my previous article “PCB Design Techniques for DDR, DDR2 & DDR3.”
Figure 7 shows the data lane routing for a DDR2 design. The trick is to closely match the data signals, data masks and associated strobe (which act as the data clocks). Results of pre-layout simulation of the data signals in Figure 4 show very close correlation with post-route simulation of the same signals in Figure 8.
Figure 7. Data and strobe lines for each data lane.
Figure 8. Note close timing between the data signals (MDQ0) and the data strobe (MDQS0) for a DDR2 interface.
Figure 9 shows the results of the routing process. However, before doing this, the daisy chain topology was simulated to establish whether the VTT end-of-line pull-up is required, and if a series terminator is also necessary.
Figure 9. Routing results.
Page 2 of 3
More Columns from Beyond Design
Beyond Design: Effective Floor Planning StrategiesBeyond Design: Refining Design Constraints
Beyond Design: The Metamorphosis of the PCB Router
Beyond Design: Radiation and Interference Coupling
Beyond Design: Key SI Considerations for High-speed PCB Design
Beyond Design: Electro-optical Circuit Boards
Beyond Design: AI-driven Inverse Stackup Optimization
Beyond Design: High-speed Rules of Thumb