-
- News
- Books
Featured Books
- pcb007 Magazine
Latest Issues
Current IssueInventing the Future with SEL
Two years after launching its state-of-the-art PCB facility, SEL shares lessons in vision, execution, and innovation, plus insights from industry icons and technology leaders shaping the future of PCB fabrication.
Sales: From Pitch to PO
From the first cold call to finally receiving that first purchase order, the July PCB007 Magazine breaks down some critical parts of the sales stack. To up your sales game, read on!
The Hole Truth: Via Integrity in an HDI World
From the drilled hole to registration across multiple sequential lamination cycles, to the quality of your copper plating, via reliability in an HDI world is becoming an ever-greater challenge. This month we look at “The Hole Truth,” from creating the “perfect” via to how you can assure via quality and reliability, the first time, every time.
- Articles
- Columns
- Links
- Media kit
||| MENU - pcb007 Magazine
Estimated reading time: 5 minutes
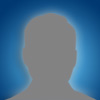
Contact Columnist Form
Oh, Really? - Why Did I Stay So Long?
Editor's Note: This column by Tony Hilvers originally appeared in the October 2012 issue of SMT Magazine.
I left IPC in July after 29 years of service. What prompted me, in 1983, to give up a corporate office with a teak desk and a wall of windows overlooking the skyline of Chicago for a dark office at IPC with no windows, a metal desk, and an office chair with stuffing coming out of the arms? Good question.
I left (okay, I was asked to leave) the North American Rail Car Company, a division of Tiger International, when Tiger International was nearing bankruptcy. I had a friend at AT&T who mentioned an open position at IPC. The not-for-profit had transitioned earlier from the Institute of Printed Circuits to a name that could only be developed by IPC’s Dieter Bergman and a group of engineers--The Institute for Interconnecting and Packaging Electronics Circuits. See, there really is an I, a P, and a C in the name!
I took the job at IPC as director of professional development, but, in those days, you could pick any title you wanted. Our building--I thought it was a converted gas station, but it was actually a former photo studio or extermination company--was next to a convenience store and stuck in a residential section of Skokie, Illinois. To confuse things further, the location had an Evanston mailing address. Our lunch table was a converted wooden picnic table and the view from my windowless office was the unisex bathroom. No more power lunches in Chicago for me. Now lunch had become a communal affair with the IPC staff. I didn’t need a coat and tie. Slacks and, hey, maybe even a tee shirt and jeans were fine.
I had worked at GTE Telecommunications Group and roamed the factory floor, so I was familiar with PCBs and electronics assembly including wave solder and component insertion machines. However, when I joined IPC, I wasn’t familiar with the TAEC, CCC, IEC, ISO, ANSI, or the dozens and dozens of abbreviations the IPC staff used.
In addition, the staff was frugal. No, that’s not right--they were cheap. Really cheap. Once, I was supported by an advertising agency. At IPC I had to send out my own direct mail to members. And heaven help me if my letter was over an ounce. I had to cut off the bottom of my letter, hundreds of my letters, to get them under an ounce to save money. I later realized that when you work for a not-for-profit, being frugal is, or should be, your lot in life.
I told a former co-worker at Tiger that my career had hit rock bottom.
So why did I stay?
I really liked the members. It sounds corny, but throughout my career at IPC I found the members to be honest, hardworking, and dedicated to the industry. You could count on members to come through whether it was for a speaking slot, serving as a workshop instructor, or chairing a committee. I really liked the men and women in the industry. Most were humble and not at all like the “emperors of the universe” I associated with in the financial services industry.
Don’t get me wrong, I’m not a Pollyanna. I recognize that the members who participated in standards development or served as workshop instructors or gave technical papers did it for very good reasons: the promotion of their company’s product/technology, the ability to influence the supply chain, the ability to influence regulations or legislation, and to network with their customers or suppliers. I think members recognize these benefits too. I’ve met many great members, but never one named Mother Teresa.
I stayed, too, because of the IPC Board of Directors. Contrary to the popular belief of some industry gadflies (remember, this is an editorial so I can say whatever I want!), the board actually drives the direction of the association. Sure, the staff makes recommendations, but it’s the board whose hands are firmly on the tiller. Historically, the board’s primary question has been, “Is it good for the membership and the industry?” And throughout my career they have been consistent in asking this question of themselves, the committees, and the staff.
I stayed because it was a lot of fun. Where else could I work where, in no particular order, I could help form the electronics manufacturing services (EMS) industry, be involved in the negotiated settlement with the Lemelson Foundation, publish round-robin research on lead-free solder alloys, create IPC’s certification program, launch a few trade shows, address conflict metals, and work with a dedicated, quality staff?
My goal for this column is to introduce you, the reader, to me. I don’t intend in future columns to be a “homer” or critic of IPC. I probably won’t write much about IPC at all. Contrary to the belief of some industry editors, many--if not most of you--don’t think about IPC a lot. You have a job to do. So, I’m not generally going to write about IPC but, rather, what I learned in my 29 years in the PCB and electronics assembly industries.
Future editorials will include “Tyranny of Sound Bites,” “Buy American,” and “Understanding Your Market.” I might even be bold enough to tweak this magazine’s publisher by writing about emotional tools to help you get over the adoption of lead-free solder.
Thanks to the I-Connect007 team for giving me the opportunity to write this column, and thank you for taking the time to read it.
Anthony (Tony) Hilvers left IPC in July 2012 after serving the association for 29 years, most recently as vice president of industry programs. At IPC he was responsible for industry segments including the PWB and EMS Management Councils, the PWB Suppliers Council, the Surface Mount Equipment Manufacturers Council, the Solder Products Value Council, and associated events, including IPC APEX EXPO. Hilvers was also responsible for IPC’s Market Research, Government Relations and Environmental Policy and Professional Departments. While at IPC, he formed the EMS management council and published the first market research study on the EMS industry in 1984. Hilvers launched six exhibitions including IPC Printed Circuits Expo, IPC APEX Conference and Exhibition and worked with the Hong Kong Printed Circuit Association to launch the HKPCA/IPC International Printed Circuits and Assembly Fair. Tony can be contacted at anthonyhilvers@gmail.com.
More Columns from Various Archived Columns
Slash Sheet Chaos: Is What You See, What You Get?Moisture in Materials: Avoiding Process Gremlins
Material Witness: Beat the Heat--A Non-Math Intro to Thermal Properties
Material Witness: Considerations in Using TC Materials for PWBs
Material Witness: Are Your Materials Up to the Challenge?
Material Witness: Thermal Oxidation of Materials, Part I
Material Witness: Thermal Oxidation of Materials, Part II
Material Witness: R.I.P. Speedboard C