-
- News
- Books
Featured Books
- pcb007 Magazine
Latest Issues
Current IssueInventing the Future with SEL
Two years after launching its state-of-the-art PCB facility, SEL shares lessons in vision, execution, and innovation, plus insights from industry icons and technology leaders shaping the future of PCB fabrication.
Sales: From Pitch to PO
From the first cold call to finally receiving that first purchase order, the July PCB007 Magazine breaks down some critical parts of the sales stack. To up your sales game, read on!
The Hole Truth: Via Integrity in an HDI World
From the drilled hole to registration across multiple sequential lamination cycles, to the quality of your copper plating, via reliability in an HDI world is becoming an ever-greater challenge. This month we look at “The Hole Truth,” from creating the “perfect” via to how you can assure via quality and reliability, the first time, every time.
- Articles
- Columns
- Links
- Media kit
||| MENU - pcb007 Magazine
Estimated reading time: 6 minutes
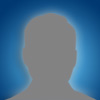
Contact Columnist Form
Oh, Really? The Tyranny of Sound Bites & the Sad Saga of Conflict Minerals
Editor's Note: This column originally appeared in the November 2012 issue of SMT Magazine.
Many years ago, Jack Wyatt, technical vice president of EIA, recounted a conversation he had with a congressman who asked if a replacement for tin-lead solder existed. Jack replied, “No, not really,” and then talked about the wonderful technical qualities of tin-lead solder--its history of reliability, low cost, and marginal impact on the environment. Jack then explained the disadvantages of lead-free solder.
The congressman, Jack said, held up his hand and told him to stop. The congressman said, “Jack, I’m a bright guy and I understand the benefits of tin-lead solder. However, when I get back to the district, my opponent is simply going to say ‘your congressman supports putting lead into the environment and harming your children.’ My response to his attack would be a 15-minute technical explanation on the merits of tin-lead solder. My opponent is going to kill me on this issue and I’m not going to support it.”
Guess what? The same thing happened with conflict minerals. On August 22, 2012, the U.S. Securities and Exchange Commission (SEC) finally adopted regulations under Section 1502 of the Dodd-Frank Wall Street Reform and Consumer Protection Act to enforce disclosure and reporting obligations on conflict minerals. Conflict minerals, regardless of where they are extracted, are tantalum, tin, tungsten, and gold.
The regulations, on first blush, have only limited scope. The SEC will enforce reporting requirements on only publicly-traded companies. But guess what? How many of your customers are publicly-traded companies or how many of your customers are customers to publicly-traded companies? “All” or “Almost all” is probably your response.
Oh, and the regulations don’t just impact the electronics industry, but nearly every single publicly-traded company in the U.S. And the regulations are going to flow down the entire supply chain of each industry. Section 1502 was intended to stop the atrocities taking place in the Democratic Republic of the Congo (DRC) and was placed at the last minute into the Wall Street Reform Act. Once in the Act, it was and is nearly impossible to vote it out. Why? No congressman or senator (like lead-free) is going to take a stance against Section 1502. Going back to their districts, anyone opposed to conflict minerals would face, “So you are against protecting innocent women and children in the DRC from rape and murder?” No elected official wants to be on the sharp end of that debate.
So why and how did conflict minerals happen? And why should the electronics industry care? In the article, “The International Dimensions of the Congo Crisis,” Georges Nzongola-Ntalaja explains that the second Congo war--or, as some describe it, Africa’s world war--“was a new type of war altogether, a war of resources. This was a war in which there was little engagement between the belligerents, and even allies would fight over turf for the control of resources.”
The results of this war of resources can be found in UNICEF’s Humanitarian Update: “An estimated 2.2 million people are internally displaced in eastern Democratic Republic of the Congo (DRC) as of June 2012--the highest number of internally displaced persons (IDPs) in DRC since the end of 2009. At least 50% of the displaced are under 18 years of age. Grave violations are taking place, including massacres of entire villages by armed groups, mass rape, abductions, exploitation and abuse, and child recruitment and use in armed forces and groups.”
The intention of Section 1502 was to stop these atrocities.
Why Should the Electronics Industry Care?
I have been following this issue for three years. When I first heard about conflict minerals I thought the industry could simply stop buying these minerals from the warlords who operate the mines in the DRC. Problem solved!
Simple problem; simple solution, right? This was a very bad idea. First, this action would be a boycott in violation of the World Trade Organization. The second and most critical point is that this action would significantly harm the artisanal mines not controlled by the warlords. The DRC accounts for 4% of the world’s tin. However 50% of tin is mined by artisanal miners who use the profits to feed their families.
What seemed to be a simple problem became very complex in a hurry.
To their credit, over the last several years, the electronics industry was very proactive in addressing this problem. Groups like Electronic Industry Citizenship Coalition (EICC), Global e-Sustainability Coalition (GeSI), ITRI, and IPC and IPC Solder Products Council were, and still are, working on a number of initiatives including bagging and tagging minerals from artisanal mines and working to certify smelters.
But Section 1502 added a whole new level of complexity on the good work of the industry.
The Impact of Section 1502
Regulations are going to be costly. IPC estimates that the cost to the electronic interconnect industry would be $279 million in the first year of implementation for due diligence alone compared to the government’s original estimate of $16.5 million within the proposal. The final regulation, though, contains a new cost analysis in which SEC modified its original assessment to between $3 and $4 billion.
Now some consultants supporting the NGOs have said, “Aw, it won’t be that much. Business always overestimates the cost to prove their point.” The cost estimates seem reasonable to me, considering almost all publicly-traded companies in the electronics industry have to implement due diligence across their entire supply chains. The high cost is a fact that the NGOs are trying to marginalize.
Let’s have the next sound bite: “Big, bad business, all you care about is the money and the hassles this regulation causes!” Remember, I said this was a complex issue. Well, it appears that these regulations might not be that effective. And as a matter of fact, Section 1502 is hurting the artisanal miners in the DRC.
Mvemba Phezo Dizolele, adjunct professor at Johns Hopkins University’s School of Advanced International Studies, voiced this concern in his testimony to the United States House of Representatives Committee on Financial Services Subcommittee on International Monetary Policy. “In eastern Congo, from Butembo in North Kivu to Nzibira in the hills of South Kivu, thousands of families now live off this informal mineral trade, which generates between $300 million and $1.4 billion a year. The long supply chain ensures that people who would otherwise be unemployed and starve have a minimal income. These people, however, are likely to pay a high price for the legislation and lose their livelihood.”
Great! We pass a law that will cost U.S. business a lot of money and is plunging the artisanal miners in the DRC into abject poverty and starvation.
The world receives stunningly bad outcomes when decision makers base their decisions on sound bites rather than good science and sound social policy.
Anthony (Tony) Hilvers left IPC in July 2012 after serving the association for 29 years, most recently as vice president of industry programs. At IPC he was responsible for industry segments including the PWB and EMS Management Councils, the PWB Suppliers Council, the Surface Mount Equipment Manufacturers Council, the Solder Products Value Council, and associated events, including IPC APEX EXPO. Hilvers was also responsible for IPC’s Market Research, Government Relations and Environmental Policy and Professional Departments. While at IPC, he formed the EMS management council and published the first market research study on the EMS industry in 1984. Hilvers launched six exhibitions including IPC Printed Circuits Expo, IPC APEX Conference and Exhibition and worked with the Hong Kong Printed Circuit Association to launch the HKPCA/IPC International Printed Circuits and Assembly Fair. Tony can be contacted at anthonyhilvers@gmail.com.
More Columns from Various Archived Columns
Slash Sheet Chaos: Is What You See, What You Get?Moisture in Materials: Avoiding Process Gremlins
Material Witness: Beat the Heat--A Non-Math Intro to Thermal Properties
Material Witness: Considerations in Using TC Materials for PWBs
Material Witness: Are Your Materials Up to the Challenge?
Material Witness: Thermal Oxidation of Materials, Part I
Material Witness: Thermal Oxidation of Materials, Part II
Material Witness: R.I.P. Speedboard C