-
- News
- Books
Featured Books
- pcb007 Magazine
Latest Issues
Current IssueInventing the Future with SEL
Two years after launching its state-of-the-art PCB facility, SEL shares lessons in vision, execution, and innovation, plus insights from industry icons and technology leaders shaping the future of PCB fabrication.
Sales: From Pitch to PO
From the first cold call to finally receiving that first purchase order, the July PCB007 Magazine breaks down some critical parts of the sales stack. To up your sales game, read on!
The Hole Truth: Via Integrity in an HDI World
From the drilled hole to registration across multiple sequential lamination cycles, to the quality of your copper plating, via reliability in an HDI world is becoming an ever-greater challenge. This month we look at “The Hole Truth,” from creating the “perfect” via to how you can assure via quality and reliability, the first time, every time.
- Articles
- Columns
- Links
- Media kit
||| MENU - pcb007 Magazine
Estimated reading time: 10 minutes
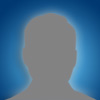
Contact Columnist Form
PCB Design Data: What Do Your Customers Expect?
One vision for the future of our industry is that every CAD system will eventually have the ability to output a common file format. Imagine a single file that could be sent to allof our customers, and each would extract the type of data needed for a specific process. A universal data format for electronics manufacturing will offer many advantages, and many are diligently working toward that goal; however, several considerations still need to be resolved, and there is still no consensus yet among industry leaders.
In the meantime, you need to know what you will be creating for your customers. The end result will be two major sets of manufacturing data: one for bare board fabrication and the otherfor assembly and test. In addition to these two, you may also be asked to provide other files along the way, so let's take a look at those first.
Bill of Materials (BOM)
When packaging a design, your CAD software will interpret the schematic diagram and map the symbols into components, assigning a unique identifier called a reference designator to each one. Since the system now knows how many of each type of component is required to build the product, a part list or bill of materials (BOM) can be generated.
Even before you start the board layout, several people may be waiting for the BOM information, so don’t delay sending it. The people responsible for purchasing may want this information to start looking for components that have long buying lead times, or for cost analysis or inventory control, and maybe even for component obsolescence study. Once you are confident that your BOM matches the design intent, get it to the people who can use it as soon as possible.
Mechanical Data
CAD systems used for circuit board layout are usually different than the CAD systems used to design the mechanical aspects of the product, but if a common file format can be used to transfer data between them, your job may get a lot easier.
Since physical details of the product such as the dimensions of the enclosure or the mounting scheme are most often defined in a mechanical CAD system, it may be easier for a mechanical engineer to define the board outline and send it to you. This process can become quite sophisticated, including the ability to define keep-out areas, height restrictions, connector locations, mounting hole sizes, etc. Importing this type of data directly into the circuit board layout can save time and reduce the chance for errors and oversights.
If the circuit board layout software can export a file back to the mechanical design software, additional interference checks can be performed before manufacturing begins. Sometimes a 3D model can be created in the mechanical system, and seeing a better representation of your final assembly mounted inside the product can highlight an issue that might not have been apparent in your 2D layout software, so take advantage of it if it is available.
Quoting
Before the design is finished, the purchasing department may ask you in advance for enough information to get a budgetary quote. The fabrication data and drawing will provide everything a bare board fabricator needs to know about the product, but these can’t be created before the layout is complete. In the meantime, cost analysis and purchase orders can start if you can provide the basic parameters of the design. For the bare board quote, they will want to know:
- Board size, thickness, and any cut-out or slot requirements.
- Board material including desired final finish.
- Number of layers.
- Approximate number of holes, and smallest hole size.
- Smallest trace width and clearance.
- Quantity of boards and required turnaround time.
Some of these estimates change slightly before the design is finished, but most fabricators are willing to provide a budgetary quote as long as they can adjust the price if there are significant changes.
The Fabrication Data Package
Artwork
You will be providing a description of each layer image either in Gerber format or in one of the other proprietary data formats supported by your CAD system.
Most circuit board artwork is described using the Gerber data format, so I should probably include a little historical background before we move on. The Gerber data format was developed by Gerber Scientific in 1980 as an input to control a photoplotter. A photoplotter was similar to a pen plotter, but instead of using ink on paper it used different sized apertures to expose an image on film, using a beam of light. Each file describes a single layer, and is used to create images for conductive layers, soldermask layers, silkscreen layers, and paste screen layers. These layers were created by flashing exposures in specific locations defined by shape (circles to create plated through-hole pads, for example, or rectangles to create SMT lands, etc.) and connecting them together by drawing exposures from point to point with apertures specified by width (usually round).
When using the original Gerber format (based on a subset of EIA RS-274-D), an aperture list was also required to define the sizes of the draws and flashes, but Gerber data files created using the newer RS-274-X format have the aperture information embedded in each file, so a separate list is not required. Use the newer 274X format if your CAD system can support it.
Although the Gerber data format was developed to control a photoplotter using draws and flashes, modern CAM systems can read in all the data at once and rasterize a complete image for each layer. This is much faster than drawing/flashing each feature sequentially.
Drill Data
Two more types of ASCII files are needed for numerically controlled drilling (NCD). These will be used to define the size and location of all the holes in the circuit board, both plated and unplated.
- A tool table lists the diameter of each drill size and assigns them to tool numbers, and gives instructions about how to interpret the drill data.
- The drill data file contains hole locations for each drill sorted by tool number
As a supplement to the ASCII drill data files, it is customary to provide additional information related to drilling on the fabrication drawing in the form of a hole legend or drill chart. During quoting, and for quality inspection activities, this summary is easier to read than having to interpret the raw data. Drill sizes are given unique symbols or letters, and the pictorial representation of the board on the drawing will show these symbols as a visual aid.
Netlist
The netlist file is not always included in fabrication data packages, but it probably should be. A bare board can be fabricated without a netlist, but if it is available, an extra level of checking is available that can help ensure that the data files describe the intended connectivity. This file should be in the IPC-D-356 format, which can be created automatically by most PCB layout software packages.
Fabrication Drawing
The fabrication drawing fulfills several important functions to support the circuit board manufacturing process:
- It provides enough information about the design for the bare board fabricator to prepare a quote.
- It adds all the extra details about the build that aren't easily incorporated into the data files, like material and final finish.
- It lists the criteria by which the finished product will be evaluated for acceptability.
- It serves as a tool to be used during final inspection.
- It is a record or document to store the history of a product by title, part number and revision, physical dimensions, and lists the name of the designer and possibly several other supporting entities as well as the company name and address, etc.
Several different types of information can be found on a typical fabrication drawing: board details including layer stack-up and construction, materials and process specifications, conductor width and clearance minimums, fabrication allowances, impedance requirements, marking requirements, test coupon requirements, performance requirements, and a graphical representation of the board with critical dimensions.
ReadMe.txt
Including this file into your data package gives you an opportunity to add extra information to the bare board fabrication order. For example, you may have intentionally shorted two nets together (like AGND and DGND) and you don't want the fabricator to put your job “ON HOLD” because of a netlist discrepancy. A README.TXT file is the place to include additional notes that you may not want to show in the final documentation. This is also a good place to list yourself or someone else as a contact, with name, phone number and e-mail address.
The Assembly/Test Data Package
Assembly Drawing
The centerpiece of an assembly drawing is a pictorial representation of what the finished electronic assembly will look like. The graphics should clarify component polarity, and provide other details specific to the assembly. Notes can be added for any special instructions and to indicate what level of workmanship and acceptability is expected.
Solder Paste Data
If surface mount components are used in the design, they will be attached to the board using solder paste. This solder paste is applied to the surface of the board using a stainless steel paste screen, which is typically created using a Gerber data file that describes the areas of the board where paste is needed. Two paste screens are required if there will be surface mount parts on both sides of the board assembly.
Paste screen technology is quite sophisticated, and unless you really know what you’re doing, you should provide paste screen apertures that are the same size as the lands you will be soldering to. This will give the paste screen manufacturer a known starting place to begin making modifications for various technologies.
Component Placement Data
Components needed for the assembly are purchased in quantity, loaded onto reels or inserted into plastic tubes. A component pick-and-place machine features a specific number of feeders that are loaded with these tubes and reels. After solder paste is applied to the land patterns of a bare board, it is loaded into the pick-and-place machine where a camera aligns the board using metal targets called fiducials (usually round dots 1 mm in diameter etched into the surface conductor layer). Then components are picked up one at a time and placed on the board in specific locations, at the proper rotation. An ASCII data file contains the fiducial locations, and the X-Y coordinates and rotation for each component.
ReadMe.txt
This is the place to include additional notes that you may not want to show in the final documentation. This is also a good place to list yourself or someone else as a contact, with name, phone number and e-mail address.
Test Data
Some products will be manufactured in a high enough volume to make the expense of an in-circuit test (ICT) fixture worthwhile. An ICT fixture and program will be developed to test the final assembled circuit board before it is mounted into the product. For these products you will add test points to the board layout, and then generate an extra file containing the test point coordinates. Many CAD systems can help automate this task. A copy of the schematic may also be helpful for the person developing the test program.
Compressed Archives
Data files are often combined and compressed into a single file called an archive, using a file extension such as ZIP, RAR or TAR. The resulting archive file can be transferred between customers and suppliers, and the individual files can be easily restored at the destination. Three of the most important advantages of compressed archives are:
- Compressed archives keep necessary components of a package together, making organization easier and reducing the chance of missing files.
- Compressed files are much smaller, needing less storage space, less time and less network usage for transfers.
- The software that compresses and uncompresses archives has automatic built-in error checking.
Unless your CAD system can output a single file format that is supported by your manufacturing process, you will probably be combining several different types of data into ZIP files before sending them out to your manufacturing partners.
Milestones
Throughout the design process there will be several different people using your data. After you work through a few designs, start recording the steps that you did to get from start to finish, and who needed what along the way. Then rearrange the steps where possible to get the data to the people who need it as soon as possible. You don't want to create bottlenecks for others, and it's better for you to be waiting on them than it is for them to be waiting on you.
Jack Olson, C.I.D.+, has been designing circuit boards full-time for more than 20 years. He would like to thank all the friends and colleagues who have taken time to teach him about the real world of electronics development.
This column originally appeared in the February 2013 issue of The PCB Design Magazine.
More Columns from Various Archived Columns
Slash Sheet Chaos: Is What You See, What You Get?Moisture in Materials: Avoiding Process Gremlins
Material Witness: Beat the Heat--A Non-Math Intro to Thermal Properties
Material Witness: Considerations in Using TC Materials for PWBs
Material Witness: Are Your Materials Up to the Challenge?
Material Witness: Thermal Oxidation of Materials, Part I
Material Witness: Thermal Oxidation of Materials, Part II
Material Witness: R.I.P. Speedboard C