-
- News
- Books
Featured Books
- pcb007 Magazine
Latest Issues
Current IssueInventing the Future with SEL
Two years after launching its state-of-the-art PCB facility, SEL shares lessons in vision, execution, and innovation, plus insights from industry icons and technology leaders shaping the future of PCB fabrication.
Sales: From Pitch to PO
From the first cold call to finally receiving that first purchase order, the July PCB007 Magazine breaks down some critical parts of the sales stack. To up your sales game, read on!
The Hole Truth: Via Integrity in an HDI World
From the drilled hole to registration across multiple sequential lamination cycles, to the quality of your copper plating, via reliability in an HDI world is becoming an ever-greater challenge. This month we look at “The Hole Truth,” from creating the “perfect” via to how you can assure via quality and reliability, the first time, every time.
- Articles
- Columns
- Links
- Media kit
||| MENU - pcb007 Magazine
Estimated reading time: 1 minute
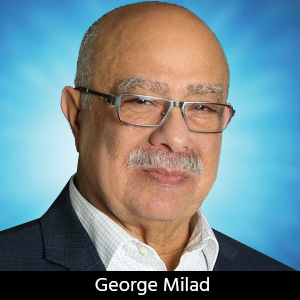
Acid Copper Plating for High Aspect Ratio and Via Fill
Newer products focused on form factor (size, weight, and portability) as well as high reliability, coupled with new developments in plating technology, offer designers options that were not available a few years ago. Among these are deposited copper via fill and very high aspect ratio through-hole plating. The former meets HDI requirements and the latter, high-layer-count (40+ layers) boards like backplanes and chip tester boards. Both of these are high-value-added products that are attractive to manufacturers who specialize in leading-edge technology.
These requirements can only be met with two distinctive plating systems. The high aspect ratio plating is based on low electrolyte concentration with a specialized additive package specifically designed for this low current density plating application and an optimized plating cell setup. Via fill, on the other hand, requires a very high concentration of electrolyte with a specific additive package and a specific cell design.
To meet these specification requirements, the board shop is forced to seek new and advanced processes in every department in the manufacturing process. Acid copper plating comes under heavy scrutiny, as it is the process that forms the traces and the through-hole connectivity that conveys the signal from end-to-end of the final device.
Editor's Note: This article originally appeared in the May 2013 issue of The PCB Magazine.
More Columns from The Plating Forum
The Plating Forum: Reduction Assisted Immersion Gold for ENEPIG Surface FinishThe Plating Forum: Surface Finish Evolution from Conventional to Advanced
The Plating Forum: Plating in Electronic Applications
The Plating Forum: How the Pandemic Impacted PCB Manufacturing
The Plating Forum: The Significance of IPC ENIG Specification 4552 Revision B
The Plating Forum: The IPC Surface Finish Specifications
The Plating Forum: An Overview of Surface Finishes
The Plating Forum: DIG—The Next Generation