-
- News
- Books
Featured Books
- pcb007 Magazine
Latest Issues
Current IssueThe Hole Truth: Via Integrity in an HDI World
From the drilled hole to registration across multiple sequential lamination cycles, to the quality of your copper plating, via reliability in an HDI world is becoming an ever-greater challenge. This month we look at “The Hole Truth,” from creating the “perfect” via to how you can assure via quality and reliability, the first time, every time.
In Pursuit of Perfection: Defect Reduction
For bare PCB board fabrication, defect reduction is a critical aspect of a company's bottom line profitability. In this issue, we examine how imaging, etching, and plating processes can provide information and insight into reducing defects and increasing yields.
Voices of the Industry
We take the pulse of the PCB industry by sharing insights from leading fabricators and suppliers in this month's issue. We've gathered their thoughts on the new U.S. administration, spending, the war in Ukraine, and their most pressing needs. It’s an eye-opening and enlightening look behind the curtain.
- Articles
- Columns
- Links
- Media kit
||| MENU - pcb007 Magazine
Estimated reading time: 1 minute
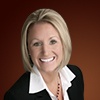
The Short Scoop: Stencils for QFNs
Quad flatpacks, no leads (QFNs) and dual flatpacks, no leads (DFNs) are becoming more popular component packages, in part because they are ideal for small, hand-held devices. As stencil manufacturers, our thoughts immediately turn to the question, how do we design and manufacture a stencil for these devices? What materials should be used? What types of coatings? How should the apertures be designed to get the best solder paste release? How can we accommodate the reduced footprint and keep-out areas? QFNs present many challenges to the assembly printing process, but the short scoop is that with proper stencil design, correct stencil technology selection (laser, electroform, and nano-coat), and consideration for the effects of PCB soldermask layout choices, these challenges can be overcome.
QFNs have a very small form factor--they are typically 0.85 mm thick with a body size from 3 mm up to 12 mm. This allows for smaller and lighter packages. Most QFNs have a metal pad on the underside for grounding and heat conduction. The leads and ground plane conductor are flat and in the same plane on the bottom of the package. DFNs have a similar center metal pad, but have leads on only two sides. This ground plane provides excellent electrical conductivity and offers better heat sink thermal properties when compared to other SMT packages. All these advantages make QFNs a good choice for high density electronics. So let’s discuss the problems that arise when using these components and what you can do to handle the printing challenges associated with fabrication.Read the full column here.Editor's Note: This column originally appeared in the October 2013 issue of SMT Magazine.
More Columns from The Short Scoop
Adapting Stencils to Manufacturing Challenges in 2015The Short Scoop: Stencil Printing in PCB Cavities
The Short Scoop: Printing Two-level PCBs in One Step with a 3D Electroform Stencil
The Short Scoop: Improving Stencil Printing Results
The Short Scoop: More Stencil Questions (and the Answers!)
The Short Scoop: Selecting a Stencil Frame
The Short Scoop: Screen Printing Solutions for Small Die & Precision
The Short Scoop: 10 Common Stencil Questions