-
- News
- Books
Featured Books
- pcb007 Magazine
Latest Issues
Current IssueInventing the Future with SEL
Two years after launching its state-of-the-art PCB facility, SEL shares lessons in vision, execution, and innovation, plus insights from industry icons and technology leaders shaping the future of PCB fabrication.
Sales: From Pitch to PO
From the first cold call to finally receiving that first purchase order, the July PCB007 Magazine breaks down some critical parts of the sales stack. To up your sales game, read on!
The Hole Truth: Via Integrity in an HDI World
From the drilled hole to registration across multiple sequential lamination cycles, to the quality of your copper plating, via reliability in an HDI world is becoming an ever-greater challenge. This month we look at “The Hole Truth,” from creating the “perfect” via to how you can assure via quality and reliability, the first time, every time.
- Articles
- Columns
- Links
- Media kit
||| MENU - pcb007 Magazine
Estimated reading time: 1 minute
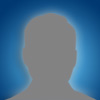
Contact Columnist Form
Design for Manufacturing: Mythbusting - Semi-additive Process Makes Sub-3/3 a Reality
Prudent PCB designers used to have good reasons for avoiding trace widths and spaces smaller than 3 mils beyond very short spans. But the 3-mil limitation is now becoming a thing of the past, thanks to the use of semi-additive fabrication by some board manufacturers. The main reason designers steered clear of sub-3-mil lines and spaces for more than short distances is etch factor.
The convergence of ever-greater circuit density and ever-higher data rates has reached the point where the chemistry of conventional PCB fabrication processes cannot be controlled tightly enough to consistently satisfy design needs. The traditional manufacture of PCBs begins with a laminate clad with copper on one or both sides. PCB manufacturers purchase clad laminates (cores) from suppliers in a wide range of substrate materials and copper thicknesses, and they also create laminates by bonding substrate materials in prepreg form with copper foils in a press.
Basically, traces are patterned by applying an etch resist to the copper surface, curing the resist by selectively exposing it to light where copper should be retained as traces and other features, and then etching away (subtracting) the unexposed resist and underlying copper in an acid bath. The objective is to produce traces whose cross-section is rectangular. However, the bath not only removes copper in the vertical direction but also eats some of it away at the sides of the traces horizontally underneath the resist, resulting in the sort of profile illustrated in Figure 1.
Figure 1: The etch factor (F) is the ratio of the trace height divided by how far the trace was eaten away at the top on one edge compared to the base. F = t/x.
Editor's Note: This column originally appeared in the April 2014 issue of The PCB Design Magazine.
Amit Bahl directs sales and marketing at Sierra Circuits, a PCB manufacturer in Sunnyvale, CA.
More Columns from Various Archived Columns
Slash Sheet Chaos: Is What You See, What You Get?Moisture in Materials: Avoiding Process Gremlins
Material Witness: Beat the Heat--A Non-Math Intro to Thermal Properties
Material Witness: Considerations in Using TC Materials for PWBs
Material Witness: Are Your Materials Up to the Challenge?
Material Witness: Thermal Oxidation of Materials, Part I
Material Witness: Thermal Oxidation of Materials, Part II
Material Witness: R.I.P. Speedboard C