-
- News
- Books
Featured Books
- pcb007 Magazine
Latest Issues
Current IssueInventing the Future with SEL
Two years after launching its state-of-the-art PCB facility, SEL shares lessons in vision, execution, and innovation, plus insights from industry icons and technology leaders shaping the future of PCB fabrication.
Sales: From Pitch to PO
From the first cold call to finally receiving that first purchase order, the July PCB007 Magazine breaks down some critical parts of the sales stack. To up your sales game, read on!
The Hole Truth: Via Integrity in an HDI World
From the drilled hole to registration across multiple sequential lamination cycles, to the quality of your copper plating, via reliability in an HDI world is becoming an ever-greater challenge. This month we look at “The Hole Truth,” from creating the “perfect” via to how you can assure via quality and reliability, the first time, every time.
- Articles
- Columns
- Links
- Media kit
||| MENU - pcb007 Magazine
Estimated reading time: 1 minute
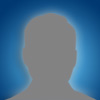
Contact Columnist Form
Conversations with...Integrated Micro-Electronics Inc.
I-Connect007 editor Richard Ayes recently interviewed Rafael Nestor Mantaring, vice president for design and development at Philippines-based EMS firm Integrated Micro-Electronics Inc. (IMI), who discusses the benefits and impact of printed electronics for the electronics manufacturing industry and the current challenges the technology faces.
Richard Ayes: Printed electronics has been around for a long time, but during the past few years, it has become of the hottest topics in the industry. What can you say about the developments in this space?
Rafael Nestor Mantaring: While the past few years have seen rapid developments in this field, the applications are still limited or very niche. That is because active circuits produced using printed electronics suffer in performance and require a larger area when compared to circuits fabricated using conventional substrates. But it has its space: in displays, thin batteries, solar panels--although still at a very low efficiency--wearable electronics, and sensors.
Ayes: From your perspective, what is the impact of printed electronics in the EMS/PCBA industry?
Mantaring: I don’t expect it to have any significant impact in the short to medium term. Because the applications are very niche, EMS companies may not find the target markets or applications attractive. Furthermore, suppliers will likely do their own manufacturing. After all, one of the attractions of printed electronics is that it supposedly can be done with relatively inexpensive equipment.
Ayes: What are the benefits of PE in electronics manufacturing?
Mantaring: One of the promises of printed electronics is being able to prototype circuits inexpensively and by yourself. This could accelerate the development of electronic products in the future. On the other hand, printed electronics has the potential of supplying components with special requirements to EMS companies. For example, very thin batteries and very flexible assemblies.
Ayes: What about the challenges in this space?
Mantaring: The challenges are producing faster, more efficient, and smaller circuits. This requires developing the right materials: that is, the inks that are “printed” on the chosen substrate and the high-resolution printing equipment.Read the full column here.Editor's Note: This column originally appeared in the August 2014 issue of SMT Magazine.
More Columns from Various Archived Columns
Slash Sheet Chaos: Is What You See, What You Get?Moisture in Materials: Avoiding Process Gremlins
Material Witness: Beat the Heat--A Non-Math Intro to Thermal Properties
Material Witness: Considerations in Using TC Materials for PWBs
Material Witness: Are Your Materials Up to the Challenge?
Material Witness: Thermal Oxidation of Materials, Part I
Material Witness: Thermal Oxidation of Materials, Part II
Material Witness: R.I.P. Speedboard C