-
- News
- Books
Featured Books
- design007 Magazine
Latest Issues
Current IssueShowing Some Constraint
A strong design constraint strategy carefully balances a wide range of electrical and manufacturing trade-offs. This month, we explore the key requirements, common challenges, and best practices behind building an effective constraint strategy.
All About That Route
Most designers favor manual routing, but today's interactive autorouters may be changing designers' minds by allowing users more direct control. In this issue, our expert contributors discuss a variety of manual and autorouting strategies.
Creating the Ideal Data Package
Why is it so difficult to create the ideal data package? Many of these simple errors can be alleviated by paying attention to detail—and knowing what issues to look out for. So, this month, our experts weigh in on the best practices for creating the ideal design data package for your design.
- Articles
- Columns
- Links
- Media kit
||| MENU - design007 Magazine
Understanding DFM and its Role in PCB Layout
April 14, 2015 | Rick Almeida, Downstream TechnologiesEstimated reading time: 2 minutes
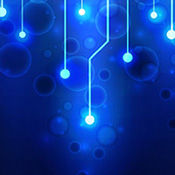
DFM, DRC, DFF, DFA, DFwhat? These are all terms used daily in the PCB design world regarding manufacturing analysis, and they are often used interchangeably. But what exactly is DFM and why is it such an important, but often ignored aspect of the PCB design process?
Let’s start by clarifying some terms. DFM is short for “design for manufacturability.” It is the process of arranging a PCB layout topology to mitigate problems that could be encountered during the PCB fabrication and assembly processes required to manufacture an electronic system. Addressing fabrication issues is what’s known as design for fabrication (DFF), and addressing assembly issues during design is known as design for assembly (DFA). The two together mostly make up DFM analysis—mostly.
In many cases, the term DRC, which stands for design rule checking, is also used interchangeably with DFM and creates further confusion. That’s understandable, because DRC issues detected in manufacturing can indeed have a direct impact on the manufacturability of a PCB. However, DRC is markedly different from DFF and DFA. Think of DRC as a hard pass/fail detection of a problem in a PCB. Either a problem exists or it doesn’t. In engineering, DRC is used to ensure that PCB layout connectivity accurately reflects the connectivity defined in a board’s associated schematic diagram. But connectivity is only one aspect of DRC. The “R” stands for rules. The rules are used largely to define the minimum spacing allowed between various PCB objects for the entire PCB or for individual layers, nets or areas on the PCB. In engineering, the spacing may have direct impact on circuit performance. In manufacturing, spacing may play a pivotal role in the ability to fabricate or assemble a PCB. As a result, DRC becomes a subset of DFM, but only if the rules used reflect a manufacturer’s requirements for spacing. Otherwise, DRC is used solely for electrical verification.
DFM’s two primary components, DFF and DFA, are more nuanced than DRC. While DRC detects very specific discrepancies from the intended interconnect, DFM identifies issues in the PCB topology that have the potential to create manufacturing problems. What’s more, a DRC defect will be present in every copy of the PCB built, so if there is a short missed in DRC, every PCB will contain the short, no matter how many PCBs are produced. By contrast, if the same PCB quantities contain DFM issues, problems may only manifest in some of the PCBs while others perform correctly as expected.
For example, a PCB layout containing very thin pieces of copper created in the design tool by rule would be correct per the schematic. And if spaced properly it would pass DRC. However, that same sliver, being so thin, could potentially detach on the physical PCB and inadvertently connect itself to other copper elements during assembly, thus creating shorts on some PCBs but not on others. So, the sliver would pass DRC verification, but in real-world manufacturing the sliver could cause some PCBs to fail. Without DFM, this problem would go on undetected and would result in scrap or rework.
This article originally appeared in the March 2015 issue of The PCB Design Magazine. To read this article in its entirety, click here.
Suggested Items
I-Connect007 Editor’s Choice: Five Must-Reads for the Week
07/11/2025 | Andy Shaughnessy, Design007 MagazineThis week, we have quite a variety of news items and articles for you. News continues to stream out of Washington, D.C., with tariffs rearing their controversial head again. Because these tariffs are targeted at overseas copper manufacturers, this news has a direct effect on our industry.I-Connect007 Editor’s Choice: Five Must-Reads for the Week
Digital Twin Concept in Copper Electroplating Process Performance
07/11/2025 | Aga Franczak, Robrecht Belis, Elsyca N.V.PCB manufacturing involves transforming a design into a physical board while meeting specific requirements. Understanding these design specifications is crucial, as they directly impact the PCB's fabrication process, performance, and yield rate. One key design specification is copper thieving—the addition of “dummy” pads across the surface that are plated along with the features designed on the outer layers. The purpose of the process is to provide a uniform distribution of copper across the outer layers to make the plating current density and plating in the holes more uniform.
Trump Copper Tariffs Spark Concern
07/10/2025 | I-Connect007 Editorial TeamPresident Donald Trump stated on July 8 that he plans to impose a 50% tariff on copper imports, sparking concern in a global industry whose output is critical to electric vehicles, military hardware, semiconductors, and a wide range of consumer goods. According to Yahoo Finance, copper futures climbed over 2% following tariff confirmation.
Happy’s Tech Talk #40: Factors in PTH Reliability—Hole Voids
07/09/2025 | Happy Holden -- Column: Happy’s Tech TalkWhen we consider via reliability, the major contributing factors are typically processing deviations. These can be subtle and not always visible. One particularly insightful column was by Mike Carano, “Causes of Plating Voids, Pre-electroless Copper,” where he outlined some of the possible causes of hole defects for both plated through-hole (PTH) and blind vias.
Trouble in Your Tank: Can You Drill the Perfect Hole?
07/07/2025 | Michael Carano -- Column: Trouble in Your TankIn the movie “Friday Night Lights,” the head football coach (played by Billy Bob Thornton) addresses his high school football team on a hot day in August in West Texas. He asks his players one question: “Can you be perfect?” That is an interesting question, in football and the printed circuit board fabrication world, where being perfect is somewhat elusive. When it comes to mechanical drilling and via formation, can you drill the perfect hole time after time?