-
- News
- Books
Featured Books
- design007 Magazine
Latest Issues
Current IssueShowing Some Constraint
A strong design constraint strategy carefully balances a wide range of electrical and manufacturing trade-offs. This month, we explore the key requirements, common challenges, and best practices behind building an effective constraint strategy.
All About That Route
Most designers favor manual routing, but today's interactive autorouters may be changing designers' minds by allowing users more direct control. In this issue, our expert contributors discuss a variety of manual and autorouting strategies.
Creating the Ideal Data Package
Why is it so difficult to create the ideal data package? Many of these simple errors can be alleviated by paying attention to detail—and knowing what issues to look out for. So, this month, our experts weigh in on the best practices for creating the ideal design data package for your design.
- Articles
- Columns
- Links
- Media kit
||| MENU - design007 Magazine
Growing Their Portfolio: Camtek’s One-Stop-Shop in Functional Inkjet Technology
April 20, 2015 | Barry Matties, I-Connect007Estimated reading time: 5 minutes
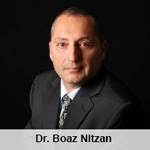
I caught up with Dr. Boaz Nitzan, VP of Functional Inkjet Technologies at Camtek recently, and the we discussed the company’s expanding portfolio into inkjet printing system for PCB solder mask & legend. The new system is designed to replace conventional coating, drying, exposure and development processes currently used in PCB manufacturing.
Barry Matties: Dr. Nitzan, why don’t you tell us about the functional inkjet technologies (FIT) division and what you’re doing at Camtek.
Dr. Boaz Nitzan: Camtek, for many years, was an automatic optical inspection company. It started as a business for PCB inspection and then purchased another company and now it does AOI both in the PCB and semiconductor industries. 2014 result showed revenues of $88.3 million with operating profit of $5.7 million.
A few years ago, Camtek purchased Printar, a company dealing with IJ printing for the PCB industry, in order to enlarge the portfolio. This startup was dealing with direct deposition of solder mask on the outer layers by inkjet technology. The project didn’t progress according to expectations. I joined Camtek two and half years ago and decided to attack the challenges from a different perspective.
We need to bear in mind that Camtek has a vast experience and knowhow in the AOI business which is peripheral process (inspection) to the PCB production line, while the Gryphon—Camtek’s functional IJ printing system for 3D surfaces for PCB solder mask & legend, is practically a manufacturing station and replaces a full “block” in the production line. FIT—Functional Inkjet Technologies—is a new division dealing with processes and manufacturing. This is how we are growing our portfolio: inspection from one side and process from the other. The FIT division developed the Gryphon.
It is a one-stop shop. In the current analog way, the process is based on seven steps: coating the solder mask and drying it, then exposing it either by exposure & film, or by LDI. Then is the development step followed by drying, again. Next is the legend printing, either by screen printing or by a digital dedicated printer. The last stage is final curing. Now we can get different panel looks by using different printing algorithms. For example, gloss, semi-matte, using the same solder mask that has already been approved by IPC 840.
The analogue process spreads over an area of 350 square meters, powered by four people operating this seven-step process. Gryphon requires only six square meters and one person, with a throughput of 15 panels per hour. This is totally revolutionary and replacing the analog process.
Matties: What about the curing?
Nitzan: Gryphon is curing while printing.
The critical difference is the alignment. Gryphon achieves a fantastic alignment by scanning the panel acquiring its surface real image, and using Camtek’s AOI system technology, which is implemented in the system
So now we have the real image of the specific side of the specific panel. Bear in mind that in one lot of 10–15 different panels, there's variation, due to the fact that there is a dimensional instability issues during the process of PCB manufacturing: skew, X/Y stretch, warp, etc. We are acquiring each side. Then, the CAD image is virtually overlaid on top of the real image that has been acquired. If there is a misregistration, the CAD is being manipulated according to the real image for full alignment, exactly one on top of the other. This is being done in the system’s computer. Only when full alignment is achieved is the new image translated into a printing “map” and the printer starts printing. The layers of the solder mask are perfectly placed on the outer, 3D surface of the PCB.
Gryphon can deal with different thicknesses of copper—25 microns, 60 microns, 70 microns, 80 microns, up to 120 microns. Each layer is approximately 17 microns. So a 3D image is actually being constructed layer by layer.
Matties: So you are saying it's a build-up?
Nitzan: Yes, it's a build-up. At the end of the build-up, using the first alignment, you take the other separation of the legend tiles, place it on top of the former solder mask separation and print it with the second array of inkjet print heads, using white ink for the legend tiles. It is a complete one-stop shop for solder mask, inkjet and legend tiles. Each side is printed in two minutes, one panel in four minutes and 15 panels per hour. The solder mask is IPC approved, UL approved for telecommunication, military and aerospace, and we are RoHS/REACH compliant.
Matties: Are there specific solder masks they have to use?
Nitzan: Yes, we have developed the solder mask.
Matties: Users have to buy your solder mask as well?
Nitzan: It's our solder mask and this is the business model. When you are developing solder mask for inkjet, or any ink for inkjet, it's very specific.
Matties: How do customers feel about that?
Nitzan: We don’t have enough feedback yet, however we assume that cooperation with known solder mask manufacturers will be acceptable.
Matties: Do you have this out in the field in practical application at this point?
Nitzan: Yes, there are currently four machines in full production: two in Israel and one here in the San Francisco Bay Area are already running production. And there is a demo center in Anaheim. The new system, the Gryphon SL will be available in May of this year.
Matties: So it's ready to go to market?
Nitzan: Yes, you can either buy it in a full configuration (i.e., solder mask and legend), or you can decide to purchase it withered (i.e., solder mask only), if you already have alternative processes for legend printing.
Currently, the throughput is not as fast as is needed for something like a Chinese high-volume manufacturer. Right now we are focusing on the American and European markets. Our next-generation machine will probably meet their needs.
Matties: Looking at the companies in America, obviously the ones with your AOI system are the first targets, right?
Nitzan: Yes, we're using Camtek's reputation, Camtek's sales force, etc. Camtek is currently running in 34 different countries, an install base of more than 2000 AOI systems around the globe, which is a lot of systems. We are using these channels to penetrate with this new technology.
Matties: Great, thanks for sharing this with us today.
Nitzan: Thank you, Barry.
Suggested Items
KYZEN to Highlight Understencil and PCB Cleaners at SMTA Querétaro Expo and Tech Forum
07/09/2025 | KYZEN'KYZEN, the global leader in innovative environmentally responsible cleaning chemistries, will exhibit at the SMTA Querétaro Expo & Tech Forum, scheduled to take place Thursday, July 24, at Centro de Congresos y Teatro Metropolitano de Querétaro.
Driving Innovation: Direct Imaging vs. Conventional Exposure
07/01/2025 | Simon Khesin -- Column: Driving InnovationMy first camera used Kodak film. I even experimented with developing photos in the bathroom, though I usually dropped the film off at a Kodak center and received the prints two weeks later, only to discover that some images were out of focus or poorly framed. Today, every smartphone contains a high-quality camera capable of producing stunning images instantly.
Hands-On Demos Now Available for Apollo Seiko’s EF and AF Selective Soldering Lines
06/30/2025 | Apollo SeikoApollo Seiko, a leading innovator in soldering technology, is excited to spotlight its expanded lineup of EF and AF Series Selective Soldering Systems, now available for live demonstrations in its newly dedicated demo room.
Indium Corporation Expert to Present on Automotive and Industrial Solder Bonding Solutions at Global Electronics Association Workshop
06/26/2025 | IndiumIndium Corporation Principal Engineer, Advanced Materials, Andy Mackie, Ph.D., MSc, will deliver a technical presentation on innovative solder bonding solutions for automotive and industrial applications at the Global Electronics A
Fresh PCB Concepts: Assembly Challenges with Micro Components and Standard Solder Mask Practices
06/26/2025 | Team NCAB -- Column: Fresh PCB ConceptsMicro components have redefined what is possible in PCB design. With package sizes like 01005 and 0201 becoming more common in high-density layouts, designers are now expected to pack more performance into smaller spaces than ever before. While these advancements support miniaturization and functionality, they introduce new assembly challenges, particularly with traditional solder mask and legend application processes.