-
- News
- Books
Featured Books
- smt007 Magazine
Latest Issues
Current IssueIntelligent Test and Inspection
Are you ready to explore the cutting-edge advancements shaping the electronics manufacturing industry? The May 2025 issue of SMT007 Magazine is packed with insights, innovations, and expert perspectives that you won’t want to miss.
Do You Have X-ray Vision?
Has X-ray’s time finally come in electronics manufacturing? Join us in this issue of SMT007 Magazine, where we answer this question and others to bring more efficiency to your bottom line.
IPC APEX EXPO 2025: A Preview
It’s that time again. If you’re going to Anaheim for IPC APEX EXPO 2025, we’ll see you there. In the meantime, consider this issue of SMT007 Magazine to be your golden ticket to planning the show.
- Articles
- Columns
Search Console
- Links
- Media kit
||| MENU - smt007 Magazine
SJIT, Solder Joint Integrity Test, To Find Latent Defects in Printed Wiring Board Assembly
April 29, 2015 | Hiroshi Yamazaki, Hioki E.E. CorporationEstimated reading time: 5 minutes
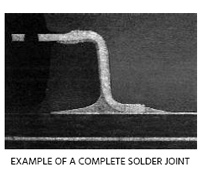
To find defects of solder joint in printed wiring board assembly, quite a few test methods have been developed so far. Capacitance method and IEEE 1149.1 or boundary scan method are often used to find opens between component leads and pads on a printed wiring board. These methods, however, can find complete opens or complete shorts only. Latent defects that can be complete defect after several years have not been found by the conversational method.
We have developed a method to find such latent defects by using 4-wire small resistance measurement technique and have built in a flying-probe in-circuit tester. It measures the resistance between component leads and pads, and checks the volume of the solder. Because the volume of the solder is inversely proportional to the resistance in-between, resistance measurement can be a way to test the solderability.
This technique is industry proven. A lot of manufacturing plants which produce printed board assembly used in automotive have adapted it. The printed wiring board assembly for automotive must endure vibration. Thus if a board assembly has a latent defect, it can bring a serious accident. In my presentation, I would like to introduce the importance of SJIT, Solder Joint Integrity Test, and a technique of SJIT.
Testing Printed Wiring Board Assembly
Printed wiring board assemblies, PWBA, are tested several times after production.The tests are categorized as production test, board-level test and system test.[1]Usually, automatic optical inspection, AOI, is done in process of production and used to not only checks component placements but also monitor the yield of the production.
The Board-level test stage follows in-process inspection at the production stage. In this stage, board assemblies are tested structurally first. Either in-circuit test or boundary-scan method or sometimes both of them are used for structural tests. The structural test, especially in-circuit test, has another purpose. It works as a pre-check for next functional test. In the functional test, power sources should be applied to the board assembly to be tested. Thus if the board assembly is not structurally complete, it can be damaged while the functional test.
The board-level structural test is done, functional tests of board-level and system-level follows.
Carrying out all the tests makes test cost increments. Thus in some cases, board-level tests are skipped and only system test is done. Moreover, in an extreme case, manufacturers do not test their products at all.
Omission of test items should be done as carefully as possible, however. It can be rebounded as a massive cost increment. Assume board-level tests including structural test and functional test are not done, and a defect is found afterwards.
Repair cost will be enormously increases as the production/test stage reaches the shipment. It is called"The 10X rule in PWBA tests."[2]
If a product including a defect comes out to the market, the problem will be much more serious.Think about the case of a car with a defective PWBA. The malfunction of the PWBA may relate to a car accident and give the driver injury. Once a defective PWBA is distributed in the market, its recall cost can be 100000X or much more.
Everyone wants to make test cost as low as possible, but as stated above, the loss will increase if test strategy is wrong. To determine test strategy, the following two factors should be considered.
1. Quality
Required degree of test quality largely depends on the quality that the products needs. A cheap complimentary toy for example does not need board-level test. If it does not work at the system level functional test, it may be thrown away.
2. Volume
How many the products is produced is another important factor to determine test strategy. For small volume production, tester may not be required, but for high volume manufacturing a dedicated tester and jigs may be required otherwise the test process can be a bottleneck.Page 1 of 2
Suggested Items
KYZEN to Focus on Aqueous Cleaning and Stencil Cleaning at SMTA Juarez
05/20/2025 | KYZEN'KYZEN, the global leader in innovative environmentally responsible cleaning chemistries, will exhibit at the SMTA Juarez Expo and Tech Forum, scheduled to take place Thursday, June 5 at the Injectronics Convention Center in Ciudad Jarez, Chihuahua.
Koh Young Installs 24,000th Inspection System at Top 20 EMS
05/14/2025 | Koh YoungKoh Young, the global leader in True 3D measurement-based inspection and metrology solutions, proudly announces the installation of its 24,000th inspection system at a Top 20 Global EMS in Thailand.
Indium’s Karthik Vijay to Present on Dual Alloy Solder Paste Systems at SMTA’s Electronics in Harsh Environments Conference
05/06/2025 | Indium CorporationIndium Corporation Technical Manager, Europe, Africa, and the Middle East Karthik Vijay will deliver a technical presentation on dual alloy solder paste systems at SMTA’s Electronics in Harsh Environments Conference, May 20-22 in Amsterdam, Netherlands.
SolderKing Achieves the Prestigious King’s Award for Enterprise in International Trade
05/06/2025 | SolderKingSolderKing Assembly Materials Ltd, a leading British manufacturer of high-performance soldering materials and consumables, has been honoured with a King’s Award for Enterprise, one of the UK’s most respected business honours.
Knocking Down the Bone Pile: Gold Mitigation for Class 2 Electronics
05/07/2025 | Nash Bell -- Column: Knocking Down the Bone PileIn electronic assemblies, the integrity of connections between components is paramount for ensuring reliability and performance. Gold embrittlement and dissolution are two critical phenomena that can compromise this integrity. Gold embrittlement occurs when gold diffuses into solder joints or alloys, resulting in mechanical brittleness and an increased susceptibility to cracking. Conversely, gold dissolution involves the melting away of gold into solder or metal matrices, potentially altering the electrical and mechanical properties of the joint.