-
- News
- Books
Featured Books
- smt007 Magazine
Latest Issues
Current IssueIntelligent Test and Inspection
Are you ready to explore the cutting-edge advancements shaping the electronics manufacturing industry? The May 2025 issue of SMT007 Magazine is packed with insights, innovations, and expert perspectives that you won’t want to miss.
Do You Have X-ray Vision?
Has X-ray’s time finally come in electronics manufacturing? Join us in this issue of SMT007 Magazine, where we answer this question and others to bring more efficiency to your bottom line.
IPC APEX EXPO 2025: A Preview
It’s that time again. If you’re going to Anaheim for IPC APEX EXPO 2025, we’ll see you there. In the meantime, consider this issue of SMT007 Magazine to be your golden ticket to planning the show.
- Articles
- Columns
Search Console
- Links
- Media kit
||| MENU - smt007 Magazine
Industry 4.0: Who Benefits?
July 13, 2015 | Michael Ford, Mentor Graphics Valor DivisionEstimated reading time: 2 minutes
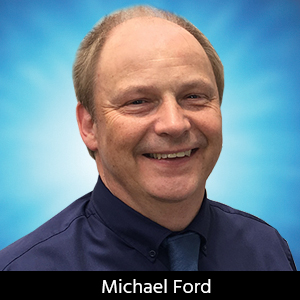
Benefits and return on investment (ROI) are not as black-and-white as you might think, and as engineers would like them to be. The reality is that even tangible reductions in cost may not be realized unless enabling factors are in place that allow savings to happen. For example, if an operator’s time in a certain position is reduced by half, it leaves the other half of the operator’s work that must be done, which means that the full reduction in the worker’s time can only be realized if the remainder work can be reliably redistributed across other operators. For an increase in productivity to bring significant change to the bottom-line of a manufacturing business, there must also be the opportunity to increase the business volume to fill the gap. Thus, the intangible side of this equation is scrutinized more as the tangible side diminishes.
The good news is that control and management software for SMT/PCB assembly manufacturing provide different sources of benefit, from which engineers can usually find just a single tangible return that can be enough to justify the purchase of a sophisticated system. However, focus on the vast majority of the rest of the system may be lost. This risk might not be thought through, adding tangible burdens and costs to the other areas of the operation rather than benefits. After installation of a new system, these effects can blow away the benefits that were identified as part of the ROI justification.
After many cycles of this experience have occurred already in most PCB assembly manufacturing companies, people are realizing that innovation and investment in new systems may affect them in ways that are less than optimum, resulting in certain groups within the organization resisting pretty much every major innovation. The real problem is that they often are not wrong.
Now, along comes Industry 4.0, which, whether fully and properly understood or not, will certainly trigger a significant amount of “automated” objection from the shop floor. For those who fully understand the nature of Industry 4.0, which is that automated communication and decision-making happen between pieces of equipment supported by sophisticated software, this can represent a nightmare scenario.
This may be a tough environment in which to introduce innovations, but this does not mean that Industry 4.0 is going to go away. One key reason is that the ideas and principles of Industry 4.0 have been a top-down initiative of the German federal government who were specifically looking for ways to create the computerization of the manufacturing industry. They may perceive Industry 4.0 as a way to reduce the overhead of low-skill labor and to address the competition of low-cost labor resources in other countries.
Editor's Note: This article originally appeared in the July 2015 issue of SMT Magazine.
Suggested Items
Real Time with... IPC APEX EXPO 2025: Aster—Enhancing Design for Effective Testing Strategies
04/18/2025 | Real Time with...IPC APEX EXPOWill Webb, technical director at Aster, stresses the importance of testability in design, emphasizing early engagement to identify testing issues. This discussion covers the integration of testing with Industry 4.0, the need for good test coverage, and adherence to industry standards. Innovations like boundary scan testing and new tools for cluster testing are introduced, highlighting advancements in optimizing testing workflows and collaboration with other tools.
Real Time with… IPC APEX EXPO 2025: Schmoll America Showcasing Four Advanced Machines
03/05/2025 | Real Time with...IPC APEX EXPOIn an expansive booth, Schmoll America is showcasing three advanced Schmoll machines and one from Impex, its partner company. Kurt emphasizes Schmoll's commitment to growth and excellence as Schmoll America approaches its first anniversary. Stop by booth 4123 to see the action.
Smart Factory Insights: The Costs of Legacy Thinking
12/01/2021 | Michael Ford -- Column: Smart Factory InsightsAs humans, we learn facts, gain impressions, create solutions, put practices into place, and move onto our next challenge. Over time, our intent is to create a legacy of value, but in many cases, we are creating legacies in a different sense. Our knowledge, experience, and creations age or become superseded, but there is resistance to replace or update. An increasing gap develops between perception and reality. Younger, more agile peers take advantage, get ahead, and we look away, thinking that they don’t know what they are doing. Though a natural human phenomenon, decision-makers in manufacturing today need to bear this mind more than ever.
Managing Cyber-Threats Within Electronics Manufacturing
11/16/2018 | Neil Sharp, JJS ManufacturingThe rise of the 4th Industrial Revolution (4IR) has brought with it digital interconnectivity that offers unprecedented opportunities for original equipment manufacturers (OEMs). But with that openness there also comes risk—the threat of the loss of data, the theft of capital or intellectual property, and the disruption of access to systems or operational technology—all of which can impede businesses and impact on trade.
IoT: Driving Change in Manufacturing
10/15/2018 | Stephen Las Marias, I-Connect007In the manufacturing world, the Internet of Things (IoT) can be seen as an element of Industry 4.0. The idea behind it is that factories would evolve to become smarter, to become a lot more flexible—to be able to make the products that customers want, basically at any time that they need.