-
- News
- Books
Featured Books
- smt007 Magazine
Latest Issues
Current IssueWhat's Your Sweet Spot?
Are you in a niche that’s growing or shrinking? Is it time to reassess and refocus? We spotlight companies thriving by redefining or reinforcing their niche. What are their insights?
Moving Forward With Confidence
In this issue, we focus on sales and quoting, workforce training, new IPC leadership in the U.S. and Canada, the effects of tariffs, CFX standards, and much more—all designed to provide perspective as you move through the cloud bank of today's shifting economic market.
Intelligent Test and Inspection
Are you ready to explore the cutting-edge advancements shaping the electronics manufacturing industry? The May 2025 issue of SMT007 Magazine is packed with insights, innovations, and expert perspectives that you won’t want to miss.
- Articles
- Columns
- Links
- Media kit
||| MENU - smt007 Magazine
Masking for Parylene Deposition
July 21, 2015 | Sean Horn, Vice President, Diamond-MT Inc.Estimated reading time: 3 minutes
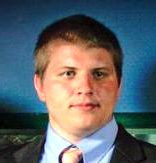
Parylene deposition is a complicated process that needs to be effectively monitored to ensure its superior levels of protection and performance. However, inappropriately applied parylene can sometimes have an adverse effect on the functionality, integrity, and performance of an assembly or component. Masking selected regions of a substrate is an essential part of the parylene coating process.
Examples of potential product failure
Parylene conformal coating does an incomparable job of protecting product substrates from harsh, unpredictable operating environments of all kinds. However, while most of parylene's key properties—barrier strength, dielectric, flexibility, lubricity, etc.—are exceptionally useful to a part or assembly, much depends on where the conformal coating is applied. Because parylene coatings are so effective, covering inappropriate areas of a component can have a negative impact on its overall performance, defeating the basic purpose for parylene application.
In this respect:
- Most points of electrical contact and many moving parts benefit from masking, which keeps the parylene from covering them.
- Conformal coating would render them ineffective, unable to either accept an electrical charge or move as designed.
In the case of printed circuit boards (PCBs) and similar electrical devices, parylene's superior dielectric qualities are detrimental, precisely because they conduct electricity poorly. Masking ensures electrical contact points are uncovered and operable, allowing them to fulfill their function. Parylene covering of moving parts can not only retard their motion, and thus impede their functionality, but will also damage the coating itself, diminishing the overall integrity of the parylene coating throughout the component.
Masking provides the best solution yet devised for these circumstances, which are common to many of parylene's product uses. By ensuring the circuit board, contact point or moving part remains uncoated, while the remainder of the product is effectively and conformally covered, masking resolves these issues; the many advantages of parylene are accessed, without suppressing the product's ability to function as designed.
The parylene masking process
While very necessary, the parylene masking process is also costly and time-consuming. Several steps encompass the masking process and ensure proper implementation:
- Appropriate identification of the regions NOT to be covered during deposition is essential. It may be necessary to diagram these areas of the assembly or component to ensure they are accurately designated.
- Parylene masking materials need to be prepared and applied to these selected areas; the objective is to avoid allowing coating into areas that need to remain uncoated.
- Peal-able masking compounds are applied to the selected product regions and permitted to fully dry. The peal-able mask is later peeled off exposing the masked regions.
- Materials commonly used for parylene masking include non-ammoniated or water-soluble liquid latex, as well as a wide range of pealable tapes and tape dots.
- Customized masking boots and caps are also among standard masking conventions for parylene conformal coating.
- After the masking process is fully complete, the parylene is applied, covering the entire substrate. In these cases, the parylene covers the masking materials, rather than the actual substrate surface.
- When the parylene has reached its appropriate coating consistency, it is pealed or otherwise removed from the masked areas, along with the underlying masking substance. This process assures the fine, durable pinhole-free covering produced by parylene is retained throughout unmasked areas, without cracking or otherwise disturbing the coating's superior conformal qualities.
Do it right
You'll want to make sure the masking process is properly implemented. Not only is this necessary to preserve the product's integrity, guaranteeing it works as designed, but also because of parylene's superiority as a conformal coating. Very simply, once bonded to a substrate, parylene is exceptionally difficult to remove. If masking is unsuccessful, further time and expense will be wasted removing parylene from the product's sensitive regions, potentially damaging the conformal coating throughout the product. The expensive, time-consuming processes of both masking and coating will have to be repeated to assure product functionality and protection.
Testimonial
"The I-Connect007 team is outstanding—kind, responsive, and a true marketing partner. Their design team created fresh, eye-catching ads, and their editorial support polished our content to let our brand shine. Thank you all! "
Sweeney Ng - CEE PCBSuggested Items
Real Time with... IPC APEX EXPO 2025: Axxon—Leading Innovations in Dispensing Technology
04/04/2025 | Real Time with...IPC APEX EXPOAxxon-Mycronic showcases its four major divisions this year, highlighting their focus on dispensing technology and conformal coating for electronics. Jeff Leal, Director of Business Development and Strategy, explains how his company is expanding into North America, particularly in Mexico and Europe, backed by a strong customer service model.
Nordson Electronics Solutions Introduces ASYMTEK Select Coat SL-1040 Ultrasonic Cleaning Station for Maintaining Conformal Coating Equipment
02/13/2025 | Nordson Electronics SolutionsNordson Electronics Solutions, a global leader in reliable electronics manufacturing technologies, announces their latest technology innovation for conformal coating systems, the ASYMTEK Select Coat® SL-1040 Ultrasonic Cleaning Station (patent pending) to keep nozzles and needles clean, and prevent clogging during production
ViTrox Showcases Revolutionary Industry 4.0 Full Turnkey SMT PCBA Inspection Solutions at Productronica Germany 2023
09/13/2023 | ViTroxViTrox, which aims to be the world’s most trusted technology company, is thrilled to announce that we will be participating in Productronica Germany, at Booth #A2.504, from 14th to 17th November 2023, in International Congress Center München (ICM), Munich, Germany.
Dymax 9771 Conformal Coating Receives MIL-I-46058C Certification for PCBA
09/12/2023 | DymaxDymax, a leading manufacturer of light-curing materials and equipment, is pleased to announce that their ground-breaking AR conformal coating, 9771, has completed the rigorous qualification testing for Military Specification MIL-I-46058C. This UL94V0 and UL746E recognized dual-cure coating has also been approved to the IPC-CC-830B standard and fully complies with RoHS2 Directives 2015/863/EU.
Embark on an Innovative Journey: Mexico Technology Day 2023 by ViTrox & SMTo
09/12/2023 | ViTroxViTrox, which aims to be the world’s most trusted technology company, is thrilled to announce that we will be partnering with our trusted Sales Channel Partner (SCP) in Mexico, SMTo Engineering SA de CV, to bring to you our Mexico Technology Day 2023.