-
- News
- Books
Featured Books
- design007 Magazine
Latest Issues
Current IssueCreating the Ideal Data Package
Why is it so difficult to create the ideal data package? Many of these simple errors can be alleviated by paying attention to detail—and knowing what issues to look out for. So, this month, our experts weigh in on the best practices for creating the ideal design data package for your design.
Designing Through the Noise
Our experts discuss the constantly evolving world of RF design, including the many tradeoffs, material considerations, and design tips and techniques that designers and design engineers need to know to succeed in this high-frequency realm.
Learning to Speak ‘Fab’
Our expert contributors clear up many of the miscommunication problems between PCB designers and their fab and assembly stakeholders. As you will see, a little extra planning early in the design cycle can go a long way toward maintaining open lines of communication with the fab and assembly folks.
- Articles
- Columns
Search Console
- Links
- Media kit
||| MENU - design007 Magazine
DownStream: What a Long EDA Trip it’s Been
June 8, 2016 | Andy Shaughnessy, PCBDesign007Estimated reading time: 2 minutes
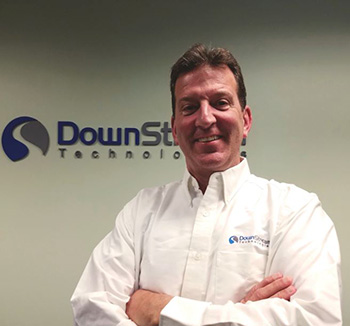
No doubt about it: DownStream Technologies co-founder Joe Clark is an EDA veteran, with a history that dates back to the very beginning of EDA tools through the merger madness of the late ‘90s and beyond. I sat down with Joe during IPC APEX EXPO, and asked him about some of the changes he’s seen, and the direction of DownStream as it enters its 15th year.
Andy Shaughnessy: Joe, why don't you start off by giving everybody a real quick background about yourself and DownStream?
Joe Clark: I actually began in EDA with a company called GenRad, or General Radio, which manufactured automatic test equipment (ATE) for verifying PCBs. The application there was mostly for functional testing. We created a PCB simulator to simulate the board and test if, for a given set of inputs, the outputs were correct. From that we ventured into simulation tools for custom components as custom ICs started to make an appearance in the market.
I went to work for Racal-Redac in the late ‘80s and early ‘90s before I moved to PADS Software, where I spent 10 years of my time. There we merged with Innoveda, which was formerly Viewlogic, and from there we spun out in 2002 to create DownStream Technologies.
Shaughnessy: And 2002 was a great year to launch a start-up.
Clark: That's a very good point. When I think about how long we've been doing DownStream it seems like it was only a couple of years ago, but it has been 15 years. When we spun out, it was really a bad time: The tech bubble had burst and then there was 9/11 and all the terrible things that surrounded that. It was just a bad time in general. Our view was the EDA industry up until then had focused primarily on what we called the upstream processes, like specifying the design, creating the schematic, the layout and so on, very few companies were focusing on the back end of the process, where we actually build things.
Shaughnessy: Where all the mistakes are.
Clark: Exactly. Our belief was that in the whole process of NPI, new product introduction, it was equally important to focus on the front end, the upstream processes, as it was to focus on the back end, the manufacturing process – where we build things. Our vision for DownStream was to be the company that helps companies to bridge the gap or chasm between the “upstream” design processes and the “downstream” physical processes. This was an area of new product development that we believed would move from something that was “nice to do” to “mission critical”.
Now, 15 years later, our vision was correct. Today, when you hear companies today talk about where they are focusing it is on the downstream processes. How do we improve that hand-off from design to manufacturing? A company’s time for realizing a return on their products is always shrinking. The technology itself is always advancing, geometries continue to shrink, and flex circuits and embedded components are now a reality. The complexities have increased enough that is it no longer good enough to take the design and do the proverbial “hand it off over the wall.”
Companies need to understand the manufacturing process and prepare the upstream processes to deal with them. Basically in a nutshell, where DownStream fits into the equation is we help companies bridge that gap, that chasm, between the upstream and downstream processes and how their products are built.
To read this entire article, which appeared in the May 2016 issue of The PCB Design Magazine, click here.
Suggested Items
Rehm Thermal Systems Mexico: Ten Years of Growth and Innovation in an Emerging Market
06/03/2025 | Rehm Thermal SystemsOver ten years ago, Luis A. Garcia began his success story at Rehm Thermal Systems. On May 15, 2013, he initially joined as a member of the Rehm USA team.
IPC Launches New Wire Harness Design Course Led by Defense Industry Expert
06/03/2025 | I-Connect007 Editorial TeamIPC is expanding its educational offerings with a new online course designed to provide foundational knowledge in wire harness and cable design. The course, Introduction to Wire Harness Design I, is led by a seasoned mechanical engineer and subject matter expert in military cable systems working at FNSS Defense Systems in Turkey.
Cicor Closes Strategic Partnership with Mercury and Strengthens Market Leadership in the European Defense Sector
06/03/2025 | CicorCicor Group announces today the successful completion of the strategic supply partnership with Mercury Mission Systems International S.A. (Mercury) announced in April.
Mycronic’s Global Technologies Acquires Surfx in the US
06/03/2025 | MycronicMycronic’s Global Technologies division has acquired Surfx Technologies, a company headquartered in the US, providing atmospheric plasma solutions for surface treatment, including cleaning and active oxide removal.
Quasar Medical to Acquire Nordson MEDICAL Design and Development business in Galway, Ireland and Tecate, Mexico
06/02/2025 | Quasar MedicalQuasar Medical, a global leader in the manufacturing of interventional and complex minimally invasive devices, announced it has signed a definitive agreement with Nordson Corporation to acquire its design and development contract manufacturing businesses in Galway, Ireland, and Tecate, Mexico.