-
- News
- Books
Featured Books
- design007 Magazine
Latest Issues
Current IssueProper Floor Planning
Floor planning decisions can make or break performance, manufacturability, and timelines. This month’s contributors weigh in with their best practices for proper floor planning and specific strategies to get it right.
Showing Some Constraint
A strong design constraint strategy carefully balances a wide range of electrical and manufacturing trade-offs. This month, we explore the key requirements, common challenges, and best practices behind building an effective constraint strategy.
All About That Route
Most designers favor manual routing, but today's interactive autorouters may be changing designers' minds by allowing users more direct control. In this issue, our expert contributors discuss a variety of manual and autorouting strategies.
- Articles
- Columns
- Links
- Media kit
||| MENU - design007 Magazine
Estimated reading time: 6 minutes
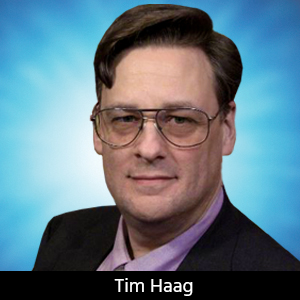
The Basics of Hybrid Design, Part 2
In the first part of this series, we discussed the basics of hybrid design from the PCB designer’s perspective, and here we will continue that discussion. We are seeing more and more of our customers exploring the world of hybrid design, and we are getting new customers for whom hybrid design is their sole focus. The world of hybrid design is growing and we have lots of hybrid specific functionality built into our software that helps designers meet and conquer the unique hybrid design requirements that they are faced with.
And yet many designers out there (and I used to be one of them), have no idea of what is meant when people start talking about hybrid design. It is therefore not uncommon for designers to avoid the subject directly while hoping to pick up little cues and pointers from others indirectly so that they are no longer in the dark. If that description sounds uncomfortably close to where you are, then read on! My hope is that this three-part series will help you by serving as a basic introduction into the world of hybrid design.
If you haven’t had a chance to read the first column in this series in last month’s issue, please go back and give it a read. To summarize, a hybrid design is an alternate to the standard PCB. Hybrids are generally smaller and more robust than PCBs, making them better suited for extreme environment conditions such as moisture, vibration, or heat. We are focusing the dis-cussion in these columns on LTCC hybrids (low-temperature, co-fired ceramics), although there are other hybrid types as well. Another topic we covered last month was substrate materials and operating temperatures. We also talked about how hybrids are manufactured using an additive screen print process. This differs from the standard PCB manufacturing process which is a subtractive (copper etching) process. And now, let’s press on.
Design software for hybrids is similar to design software for PCBs, albeit with some important differences and enhancements. Due to the differences in fabricating hybrids from regular PCBs (screen printing conductors and dielectric materials onto a substrate instead of compositing separate layers of copper and dielectric material), the need for a specific CAD layer to match a specific board layer does not apply. However, a hybrid design still requires separation between the different conductive and dielectric materials, so the standard method of setting up layers in design software is still the foundation of the design database. Therefore a hybrid design still has layers designated in the layout application, but the names of the layers will be different then what you might see in a PCB layout. Instead of “Top,” “Bottom,” and “Inner” signal layers, you will instead see layers described as “Metal_Top,” “Wire_1,” “Wire_2,” and “Metal_Bottom.” There may also be layers devoted completely to power or ground as in a PCB, but remember that they will be conductive material that is screen printed on instead of being an actual copper layer.
Routing conductors (wires) in a hybrid design on positive layers is done essentially the same way as routing traces in a standard PCB design. The conductors will carry intelligent net information the same way as a trace does in a PCB design, and the CAD application will account for their connectivity and net rule requirements. But instead of only designing layers for connectivity as a PCB would require, a hybrid also requires the design of its dielectric material as well.
Just as in a PCB, hybrid conductors need to be isolated from other conductors that are printed above or below them. And just as in a PCB, a dielectric material is used to provide this insulation. The difference is that in a hybrid the dielectric material will not be an actual composited layer as it would be in a PCB. Instead it will be added by another screen printing process. Once it is in place, screen printing of conductive material can be added on top of it to continue the hybrid buildup.
Solid layers of dielectric material are designed in the CAD application in a similar way to how an area fill or a power plane is designed for a PCB. Therefore the positive area fill or negative power plane algorithms in PCB design software lend themselves well for this, with one exception: They must be enhanced to account for the lack of intelligent net information that they would carry in a PCB. Remember, this is dielectric material which has no need for net information to be assigned to it. The key here for PCB designers is to remember that when you are looking at a hybrid design’s dielectric layers in your CAD application, they are not fills or planes even though they may look like what you are traditionally used to seeing as a fill or a plane. And to further complicate matters, there may still be layers in a hybrid design that are devoted to being an actual conductive power fill or plane.
One thing that PCB designers may not be aware of that is very different in hybrid design is the use of crossover dielectric material. As we have discussed, full layers of dielectric material can be designed into a hybrid. But in a hybrid design you may have a situation where there are only a few spots between two adjacent conductor layers where wires are crossing over each other. Obviously these points need to be isolated from each other with dielectric material to keep them from shorting, but to add another layer of full dielectric material for only these few locations would be unnecessary. Instead, hybrid designers have at their disposal the ability to add crossover dielectric material.
Remember that, although we are using the term “layers” when talking about our CAD application, the actual hybrid design will be fabricated by screen printing material from the bottom up. Therefore if we have shorts in only a couple of locations between two adjacent layers of conductors, we can instead insert a small amount of dielectric material to isolate those shorts in only those specific locations. To do this within our CAD application we will designate a new CAD layer for this dielectric cross-over material, but it will only have an image on it in those specific locations where the isolation is needed. When the hybrid design is fabricated, those areas of crossover dielectric material will be screen printed over the wires on the bottom that would otherwise be shorted, and then the next layer of wires will be screen printed over the top of that.
Hybrid design CAD software has built-in routines specifically for generating crossover dielectric areas. These areas will match the area of wires that are shorting together to provide full insulation, and they can be applied manually or generated automatically depending on the needs of the design.
Designing hybrid vias is also significantly different than what most PCB designers will be used to. In a standard PCB design, the board is usually drilled after the layers are composited together. In a hybrid design, however, vias are not drilled. Remember, the hybrid design is built from the substrate up by a screen printing process that prints both conductive mate-rial and dielectric material. Therefore vias are created by either screen printing a spot of conductive material, or by not screen printing dielectric material at that same location leaving a void. Because of this, standard drilling files are not needed in a hybrid design as the creation of vias is managed completely by the screen printing processes.
And with that we have reached the end of Part 2 of this series.
This column originally appeared in The PCB Design Magazine's April Issue
More Columns from Tim's Takeaways
Tim’s Takeaways: One for the ArchivesTim’s Takeaways: The Art of Technical Instruction
Tim’s Takeaways: PCB Design and Manufacturing—Let’s Work Together
Tim’s Takeaways: Take It From Scotty, Simple Really is Better
Tim’s Takeaways: Human Ingenuity and the Rigid-flex PCB
Tim’s Takeaways: How I Learned Advanced Design Strategies
Tim’s Takeaways: Batter Up—Stepping Up to the Substrate
Tim’s Takeaways: Tribal Knowledge—Not the Villain You Thought