-
- News
- Books
Featured Books
- design007 Magazine
Latest Issues
Current IssueShowing Some Constraint
A strong design constraint strategy carefully balances a wide range of electrical and manufacturing trade-offs. This month, we explore the key requirements, common challenges, and best practices behind building an effective constraint strategy.
All About That Route
Most designers favor manual routing, but today's interactive autorouters may be changing designers' minds by allowing users more direct control. In this issue, our expert contributors discuss a variety of manual and autorouting strategies.
Creating the Ideal Data Package
Why is it so difficult to create the ideal data package? Many of these simple errors can be alleviated by paying attention to detail—and knowing what issues to look out for. So, this month, our experts weigh in on the best practices for creating the ideal design data package for your design.
- Articles
- Columns
- Links
- Media kit
||| MENU - design007 Magazine
Predictive Engineering: Happy Holden Discusses True DFM
October 4, 2017 | Andy Shaughnessy, PCBDesign007Estimated reading time: 2 minutes
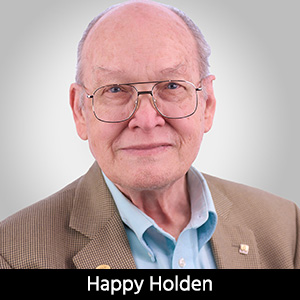
Happy Holden has been involved in DFM for over 45 years, since he first started working at HP and optimized their PCB design and manufacturing processes. Naturally, for this issue, Barry Matties and Andy Shaughnessy made it a priority to get Happy’s thoughts on DFM, and what true DFM entails.
Andy Shaughnessy: Happy, why don’t you start by telling us about your position on DFM, and why true DFM, to you, means that PCB designers and engineers should utilize predictive engineering.
Happy Holden: If you use the term “predictive engineering,” you're not going to get much recognition, because that's a term I use. What most people consider design for manufacturing, or DFX, is software that finds errors in design. Especially in CAM tooling put out by Valor, if a manufacturer puts in his design builds in a minimum, then the DFX software scans through that and finds what’s cautionary and that all requirements are met. That's all done after the fact.
For me, DFM was introduced when HP took up DFM. It was kind of invented by Professors Peter Dewhurst and Geoffrey Boothroyd. Anyway, DFM and DFMA (design for manufacturing and assembly) were really invented by these two American professors in New England. They wrote a book about it, Product Design for Manufacture & Assembly. It later became software.
Their whole philosophy centered on ways to figure out how to do it right the first time. Their book is about the nature of performance during design that allow you to decide if this is going to be easy to assemble. I think the more important component, that Hitachi and the Japanese took it up, was whether the product could be built by automation? That's really significant what Hitachi did with the philosophy. They not only took the ‘do it right the first time’ approach but then asked how they could do it simple enough that robots and automation can build it? The Japanese did this because they wanted to build all these first-generation products in a building next door in Japan and not ship it offshore like Americans were doing.
Contrast that with Apple Inc. Apple designs products that are impossible to automate. They're so complex. They're really fanciful, but they have to be built by human hands. You've got 86,000 17-year-old teenage girls in Shenzhen building these Apple products. Foxconn put up money to install 1 million robots to replace these girls. Today only about 400 robots have been installed out of that 1 million, because they found out the products they're building for the Americans can’t be automated.
I refer to DFM as being designed for manufacturing the first time. We're not just designing it, running software, finding the errors, going back, redesigning it, checking again, going back and re-spinning it, until it works. I'm alone in this definition unless you happen to be knowledgeable about Dewhurst and Boothroyd, which most people in printed circuits aren't.
To read this entire article, which appeared in the September 2017 issue of The PCB Design Magazine, click here.
Suggested Items
Delta Electronics Thailand Ranked Among Asia’s Top Corporates at the Alpha Southeast Asia 15th Institutional Investor Awards
07/14/2025 | Delta ElectronicsDelta Electronics (Thailand) Public Company Limited, a global leader in power management and smart green solutions, has been recognized by global investors for its excellence in investor relations and corporate governance, earning top ranking in the “Most Improved Investor Relations” at the Alpha Southeast Asia 15th Annual Institutional Investor Awards for Corporates, held on June 30, 2025, in Singapore.
Kimball Electronics' Pride Month Celebrations
07/14/2025 | Kimball ElectronicsAt Kimball Electronics, we believe in fostering a culture of inclusion, respect, and belonging. This June, our global teams came together to celebrate PRIDE Month with meaningful actions that reflect our commitment to the LGBTQ+ community.
NOTE Posts Interim Report for Q2 2025
07/14/2025 | NOTENOTE reports stable second-quarter results for 2025 with continued profitability and strong cash flow, reaffirming its growth strategy despite a challenging market environment.
Scanfil, MB Elettronica to Join Forces
07/14/2025 | ScanfilFinnish Scanfil, the largest European stock exchange listed Electronic Manufacturing Service company in terms of turnover, and Italian MB Elettronica (“MB”) from Cortona Arezzo have agreed to join forces.
PCBAA’s David Schild: Where U.S. Electronics Manufacturing Stands Today
07/14/2025 | Marcy LaRont, I-Connect007As the U.S. Congress looks toward a summer break, David Schild of PCBAA discusses the growing momentum in U.S. electronics manufacturing policy, emphasizing bipartisan support for reshoring efforts, the importance of targeted tax incentives, and the challenges posed by global competition. He highlights PCBAA’s growth, advocacy on Capitol Hill, and the need for sustained investment to revitalize the PCB industry.