-
- News
- Books
Featured Books
- design007 Magazine
Latest Issues
Current IssueShowing Some Constraint
A strong design constraint strategy carefully balances a wide range of electrical and manufacturing trade-offs. This month, we explore the key requirements, common challenges, and best practices behind building an effective constraint strategy.
All About That Route
Most designers favor manual routing, but today's interactive autorouters may be changing designers' minds by allowing users more direct control. In this issue, our expert contributors discuss a variety of manual and autorouting strategies.
Creating the Ideal Data Package
Why is it so difficult to create the ideal data package? Many of these simple errors can be alleviated by paying attention to detail—and knowing what issues to look out for. So, this month, our experts weigh in on the best practices for creating the ideal design data package for your design.
- Articles
- Columns
- Links
- Media kit
||| MENU - design007 Magazine
Embedded Inductors with Laser Machined Gap
December 17, 2018 | Jim Quilici, Radial ElectronicsEstimated reading time: 14 minutes
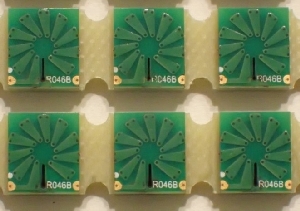
Energy efficiency is a major driver in the evolution of electronics and electronics packaging. To manage power consumption, portable appliances such as smartphones, tablets, e-readers, etc., often use multiple supply voltages and DC/DC converters. Most are based on switch mode power conversion (SMPC). In a power converter, inductors and transformers are used to temporarily store energy during switching cycles. They also have the function of filtering noise. The power magnetics are often the largest and most expensive devices in the circuit. Integrating the magnetics into either a power converter module or system board can significantly reduce size and cost of the power converter function.
Embedded magnetics offer a means for integrating the magnetic functions into a PCB substrate. Ferromagnetic cores are embedded into a PCB substrate, and the inductive windings are implemented using photolithography and standard PCB processes. Rather than building one-at-a-time, devices are arrayed on a PCB panel and fabricated using automated and batch process. In most instances, the embedded core will be a ring shaped (toroid), since this is the most efficient shape in terms of delivering high inductance per turn and containing the induced magnetic flux. Additionally, toroids are a relatively easy shape to manufacture and generally inexpensive compared to other core shapes. Common materials are pressed ceramic ferrites and tape-wound amorphous metals.
Figure 1: Embedded magnetic construction.
As indicated above, inductors and transformers are used in power converters to temporarily store energy during a switching event. A key metric of magnetic materials is their ability to store magnetic flux energy. When current is driven through a conductor wound around a magnetic core material, it produces a magnetic field (H) which induces a magnetic flux (B) in the underlying core material. The current energy is temporarily converted to magnetic flux and stored within the magnetic core. The flux, B, is essentially the field density within the core. B has units of Tesla (T) (or Gauss, G; 10,000 G = 1 T) and H is the measure of magnetizing field strength and has the units of Oersteds (Oe; 1 A/m = 4 x 10-3 Oe). B and H are closely related to voltage and current, where the flux density is proportional to the applied voltage and the magnetizing force, H, is proportional to current. The relationship between the field and flux is tied by the materials permeability, μ.
(1) B = μ H
Flux density may also be expressed in terms of inductance and drive current, as characterized through the relationship:
(2) B = LI/NAc
where L is the inductance, I is the drive current, N is the number of windings and Ac is the cross section area of the core.
Designers often use the B-H curve to analyze the relationship between the drive voltage and drive current. Figure 2 identifies that magnetic materials have a flux saturation level, BSAT, which is the state where the magnetic core has reached peak flux density. At that point, the core cannot store more energy, regardless of the amplitude of drive voltage. For ferrite materials, saturation occurs in the range of 0.350 to 0.550 T (Tesla is a unit of magnetic flux density.), depending on the composition. Cores with high permeability will saturate with modest currents. To allow higher drive currents, a gap is often introduced into the magnetic flux path. This effectively reduces the permeability of the core material and results in a reduction of the inductance of the windings. As depicted in Figure 2, gapping the core flattens out the B-H curve. Reducing the inductance allows the core to store energy from higher drive currents.
Figure 2: Typical B-H graph for an ungapped and gapped ferrite core.
A gap is produced by placing a small cut through the core. Gapping is a common method for reducing the inductance and enabling the core to be driven at higher currents before reaching saturation. It also serves to stabilize the performance of a core over different operating temperatures and drive currents. Basically, gapping the core reduces the effective permeability. The relative permeability for a gapped core can be calculated by the equation:
(3) μr' = μr / (1 +( g x μr /le)
where g is the gap distance and le is the path length of the flux around the circumference of the core. In many instances, the reduction in permeability by gapping will exceed 10x. It may seem counterproductive to create materials and core structures with high permeability and then diminish them with a gap. However, this is necessary to add stability and allow higher drive currents. There is always the option of using powdered iron core materials, which are often described as having a distributed gap. These materials generally have permeability’s less than 100 and are generally more expensive due to the precious metals used in their construction and limited number of suppliers. With conventional ferrites, we can apply a gap to achieve permeability values between 100 and 1000, which reduces the number of windings required to achieve a specific inductance. Reducing the number of windings is beneficial in reducing resistance loss in the windings. Also powdered iron materials generally exhibit higher core loss which can also impact the power converters efficiency. Core losses are a result of an alternating magnetic field in a core material. The core losses are due to hysteresis, eddy current and residual losses in the core material and is dissipated as heat.
Figure 3: Example of a gapped toroid.
Figure 4 shows a typical graph of permeability vs. temperature for a 2000 permeability manganese zinc (MnZn) material, which is typically used for power applications. Here, we see wide variations over temperature. Gapping the core reduces the permeability to about 350 and flattens out the characteristics over the full temperature range. This is important for applications that need to perform to at temperatures below 0°C.
This brings us to a design methodology. Once the designer determines the inductance required for an application, it is then a matter of over designing for much higher inductance, in anticipation that the inductance will be diminished after the core has been gapped.
Figure 4: Ferrite permeability vs. temperature (1500 permeability @ 25°C).
For power converters, embedded magnetics are useful in applications ranging up to 60 W. The power capability is primarily dictated by core sizes that are suitable for embedding into a PCB substrate. The PCB construction is limited by the PCB thickness and height (thickness) of the core. Practical applications include power to a microprocessor, battery chargers and LED lighting. There are many semiconductor SMPC controllers on the market tailored specifically for these applications. Most of these devices operate with switching speeds ranging from 500 kHz to 2 MHz. At these switching speeds, inductors in the range of 1 µH to 10 µH are commonly used. For this investigation, a test coupon was designed with indictors ranging from 2.2 µH to 10 µH. The 10 µH configuration is the focus of this paper. Generally, for power applications, it is best to select MnZn ferrite materials with permeability in the range of 2K to 3K, due to their core loss properties. In this gapping experiment, however, cores with 5K permeability were selected simply because this value was available in the author’s inventory. This difference in permeability is not significant in this particular experiment. Once the gap is applied, the core’s inductance per turn is dominated by the gap with. The differences in the initial permeability only accounts for minor difference in the final inductance.
Page 1 of 3
Suggested Items
Copper Price Surge Raises Alarms for Electronics
07/15/2025 | Global Electronics Association Advocacy and Government Relations TeamThe copper market is experiencing major turbulence in the wake of U.S. President Donald Trump’s announcement of a 50% tariff on imported copper effective Aug. 1. Recent news reports, including from the New York Times, sent U.S. copper futures soaring to record highs, climbing nearly 13% in a single day as manufacturers braced for supply shocks and surging costs.
I-Connect007 Editor’s Choice: Five Must-Reads for the Week
07/11/2025 | Andy Shaughnessy, Design007 MagazineThis week, we have quite a variety of news items and articles for you. News continues to stream out of Washington, D.C., with tariffs rearing their controversial head again. Because these tariffs are targeted at overseas copper manufacturers, this news has a direct effect on our industry.I-Connect007 Editor’s Choice: Five Must-Reads for the Week
Digital Twin Concept in Copper Electroplating Process Performance
07/11/2025 | Aga Franczak, Robrecht Belis, Elsyca N.V.PCB manufacturing involves transforming a design into a physical board while meeting specific requirements. Understanding these design specifications is crucial, as they directly impact the PCB's fabrication process, performance, and yield rate. One key design specification is copper thieving—the addition of “dummy” pads across the surface that are plated along with the features designed on the outer layers. The purpose of the process is to provide a uniform distribution of copper across the outer layers to make the plating current density and plating in the holes more uniform.
Trump Copper Tariffs Spark Concern
07/10/2025 | I-Connect007 Editorial TeamPresident Donald Trump stated on July 8 that he plans to impose a 50% tariff on copper imports, sparking concern in a global industry whose output is critical to electric vehicles, military hardware, semiconductors, and a wide range of consumer goods. According to Yahoo Finance, copper futures climbed over 2% following tariff confirmation.
Happy’s Tech Talk #40: Factors in PTH Reliability—Hole Voids
07/09/2025 | Happy Holden -- Column: Happy’s Tech TalkWhen we consider via reliability, the major contributing factors are typically processing deviations. These can be subtle and not always visible. One particularly insightful column was by Mike Carano, “Causes of Plating Voids, Pre-electroless Copper,” where he outlined some of the possible causes of hole defects for both plated through-hole (PTH) and blind vias.