-
- News
- Books
Featured Books
- pcb007 Magazine
Latest Issues
Current IssueSales: From Pitch to PO
From the first cold call to finally receiving that first purchase order, the July PCB007 Magazine breaks down some critical parts of the sales stack. To up your sales game, read on!
The Hole Truth: Via Integrity in an HDI World
From the drilled hole to registration across multiple sequential lamination cycles, to the quality of your copper plating, via reliability in an HDI world is becoming an ever-greater challenge. This month we look at “The Hole Truth,” from creating the “perfect” via to how you can assure via quality and reliability, the first time, every time.
In Pursuit of Perfection: Defect Reduction
For bare PCB board fabrication, defect reduction is a critical aspect of a company's bottom line profitability. In this issue, we examine how imaging, etching, and plating processes can provide information and insight into reducing defects and increasing yields.
- Articles
- Columns
- Links
- Media kit
||| MENU - pcb007 Magazine
Virtual Verification Station From CIMS Enhances AOI Capabilities
June 28, 2019 | Barry Matties, I-Connect007Estimated reading time: 4 minutes
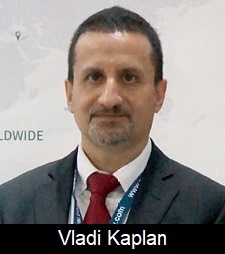
CIMS is a company well-known in the PCB industry for its automated optical inspection (AOI) solutions. At this year’s CPCA Show, Marketing and Technical Director Vladi Kaplan spoke to Barry Matties about a number of addons CIMS designed to further enhance their AOI capabilities and systems. Vladi described their Virtual Verification Station (VVS)—a server that pulls images of defects from the AOI as well as additional defect data collection, metrology, and classification capabilities—CIMS Quality Center (CQC), and Software Development Kit (SDK) as well as trends he sees with laser via inspection.
Barry Matties: Vladi, you are introducing a new product at the 2019 CPCA Show. Can you tell us about that?
Vladi Kaplan: Yes, our product is the Virtual Verification Station (VVS), and it is designed to reduce physical verification. The idea is to look at the images as seen by AOI in an intermediate stage before the board goes to physical verification on the verification stations and remove most of the false calls. In many cases, the image can easily tell the user if there’s oxidation, something that looks like dust, or defects in areas that you’re less concerned about. Then, you can remove them from verification, and everything that goes to physical verification will be either real defects or defects that you want to have a closer look at or you’re unsure about based on an AOI-grabbed image.
We’ve also built it to show you simulated color images that are almost indistinguishable from video images of verification stations, although it is still a grabbed image from AOI. It’s not straightforward colorization like taking a black and white picture and making it colored; this process is much smarter than that. We use complex AI-based algorithms to make the images look natural, making it easier to figure out if it’s a real defect or a false call. This technology relies on many factors that enable the VVS to find the most optimal way to colorize various images. If you look at those images, you can’t tell if either they’re video or simulated.
Another thing I want to highlight is the automatic classification. At this stage, we can classify critical defects, such as opens, shorts, etc. The next generation of the software will be able to go further and classify more types of defects, such as small nicks, protrusions, or false calls. The biggest challenge is to classify false calls because they can appear in many different ways, which is why we need to employ AI. We’ll have to see how far it can take us because it’s still a developing field. Will it be able to completely replace physical verification? That’s still an open question. I don’t believe it’s possible in the near term. There’s still going to be some physical verification, but that’s where we’re going and what customers are asking from us. Everybody wants to reduce physical verification, so that’s the idea.
Another product is CIMS Quality Control, or sometimes we call it the CIMS Quality Center (CQC). The idea is to display aggregated live quality information from AOI—for example, how many opens and shorts we detected, where the defects are located, and what’s the yield. The live data as it comes out of AOI is displayed in one configurable dashboard. In this example, you can see only one type of information but the user can set as many dashboards as they want. For instance, you can have utilization in real time and see how many panels you’ve already scanned, how many panels have been verified, what the yield is, and if it goes up or down. If your shorts go up, it can trigger an alarm, so you know in real time that you have to fix something within the process and so on.
We want to make it very visual and feed this information in real time so that you can have it on your laptop or big monitor in the AOI room, for example, so that anyone can look at it. You can set up different types of graphs or charts that are most relevant for you. If you’re a production manager, you may be more interested in utilization, and quality control personnel will be more interested in types of defects, their location, and where they’re coming from.
Matties: What do you mean when you said it’s in “real time?” Because this isn’t an inline process.
Kaplan: It’s AOI in real time, so as information comes out of AOI or verification, that’s typically where you capture it. That’s when you know for sure what type of defect it is, so as soon as you make that decision, information is displayed immediately. It’s accumulating and you can have it for a day, for the last hour, for even for the last 30 days, but you get the most value if it’s live.
That’s why we call it the Quality Control Center; it provides the quality data as it comes in rather than waiting until electrical test, for example, when it would be too late the fix the process. And it’s a pretty simple program that can run on any computer; you don’t need specific hardware to run it. All of the data comes out of our server. We centralize the data collection from our AOI and VVS systems. Everything goes into one server, and this program pulls out the data and extracts all of the information that you’re interested in.
Matties: Is there a server at the customer’s location or a server at your location?
Kaplan: There’s a server at the customer’s location where all of the data is consolidated.
To read the full article, which appeared in the June 2019 issue of PCB007 Magazine, click here.
Suggested Items
TRI Unveils New Platform for Diverse Board Sizes
07/14/2025 | TRITest Research, Inc. (TRI), the leading test and inspection systems provider for the electronics manufacturing industry, proudly introduces a new size configuration for SPI and AOI Models.
Specially Developed for Laser Plastic Welding from LPKF
06/25/2025 | LPKFLPKF introduces TherMoPro, a thermographic analysis system specifically developed for laser plastic welding that transforms thermal data into concrete actionable insights. Through automated capture, evaluation, and interpretation of surface temperature patterns immediately after welding, the system provides unprecedented process transparency that correlates with product joining quality and long-term product stability.
Smart Automation: The Power of Data Integration in Electronics Manufacturing
06/24/2025 | Josh Casper -- Column: Smart AutomationAs EMS companies adopt automation, machine data collection and integration are among the biggest challenges. It’s now commonplace for equipment to collect and output vast amounts of data, sometimes more than a manufacturer knows what to do with. While many OEM equipment vendors offer full-line solutions, most EMS companies still take a vendor-agnostic approach, selecting the equipment companies that best serve their needs rather than a single-vendor solution.
Keysight, NTT, and NTT Innovative Devices Achieve 280 Gbps World Record Data Rate with Sub-Terahertz for 6G
06/17/2025 | Keysight TechnologiesKeysight Technologies, Inc. in collaboration with NTT Corporation and NTT Innovative Devices Corporation (NTT Innovative Devices), today announced a groundbreaking world record in data rate achieved using sub-THz frequencies.
Priority Software Announces the New, Game-Changing aiERP
06/12/2025 | Priority SoftwarePriority Software Ltd., a leading global provider of ERP and business management software announces its revolutionary aiERP, leveraging the power of AI to transform business operations.