-
- News
- Books
Featured Books
- design007 Magazine
Latest Issues
Current IssueShowing Some Constraint
A strong design constraint strategy carefully balances a wide range of electrical and manufacturing trade-offs. This month, we explore the key requirements, common challenges, and best practices behind building an effective constraint strategy.
All About That Route
Most designers favor manual routing, but today's interactive autorouters may be changing designers' minds by allowing users more direct control. In this issue, our expert contributors discuss a variety of manual and autorouting strategies.
Creating the Ideal Data Package
Why is it so difficult to create the ideal data package? Many of these simple errors can be alleviated by paying attention to detail—and knowing what issues to look out for. So, this month, our experts weigh in on the best practices for creating the ideal design data package for your design.
- Articles
- Columns
- Links
- Media kit
||| MENU - design007 Magazine
Mentor Tools: Optimized for Flex and Rigid-flex Design
August 1, 2019 | Andy Shaughnessy, Design007 MagazineEstimated reading time: 2 minutes
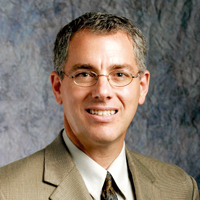
With the launch of the new Flex007 section in Design007 Magazine, we asked David Wiens, product marketing manager with Mentor, a Siemens Business, to tell us about their tools’ flex and rigid-flex design capabilities. As David explains, today’s higher-end design software tools are optimized for flex design, making workarounds a thing of the past.
Andy Shaughnessy: What are your customers’ biggest challenges in designing rigid-flex?
David Wiens: Engineering teams have designed advanced rigid-flex products for years using a series of workarounds to their EDA tools, often verifying with paper dolls. Rigid-flex designs require advanced stackup constructs (e.g., multiple outlines, each with its own stackup, and new materials). There are also additional rules that need to be applied, including bend/fold control with collision clearances, curve routing with arcs and teardrops, hatched plane fill shapes, component placement limits in flex areas, and fabrication rules around board stiffeners and coverlays. The workarounds naturally take longer to implement and often result in errors because the design must be checked manually. This can lead to a non-optimized product because once something is designed, nobody wants to go back and make ECOs. Some errors, such as copper micro-cracks, create long-term product reliability issues. Manufacturing is also a challenge. Design teams must align with their manufacturer to understand the costs of different rigid-flex structures—costs can go up quickly—and optimize the hand-off from design to manufacturing.
Shaughnessy: Tell us about the rigid-flex design capabilities in the latest versions of Mentor’s tools.
Wiens: Our solution supports flex, rigid, or rigid-flex with a common set of functionality. Native support for flex/rigid-flex extends across the flow, from initial stackup definition through design validation and manufacturing outputs, eliminating time-consuming workarounds.
It starts with an independent stackup for each rigid or flex element; these can easily be modified or overlapped. This approach limits the board outline and stackup modifications necessary when the shape of the board changes. With flex stackups, there are additional materials and layer types to model, such as cover layers, stiffeners, and adhesives. These materials are intelligent and are understood at design verification as well as the hand-off to manufacturing. Control of where bends occur is critical, so a bend area object defines the location, radius, angle, and origin. Attributes also define placement, routing (e.g., via utilization, trace corners, trace width changes, etc.) and plane metal (e.g., hatch/cross-hatch) rules in the area.
For place and route, each rigid-flex area has its own external/internal layers, so parts can be placed on any external layer (including flex regions and/or in cavities) with appropriate pads and openings automatically handled. During routing, true arcs are utilized to minimize stress fractures in flex regions, and they adhere to the constraint-driven, correct-by-design methodology for which we’re known. Curved teardrops are automatically generated and maintained dynamically. Due to the automation throughout layout, design changes are easy and safe.
To read this entire interview, which appeared in the July 2019 issue of Design007 Magazine, click here.
Suggested Items
I-Connect007 Editor’s Choice: Five Must-Reads for the Week
07/18/2025 | Nolan Johnson, I-Connect007It may be the middle of the summer, but the news doesn’t quit, and there’s plenty to talk about this week, whether you’re talking technical or on a global scale. When I have to choose six items instead of my regular five, you know it’s good. I start by highlighting my interview with Martyn Gaudion on his latest book, share some concerning tariff news, follow that up with some promising (and not-so-promising) investments, and feature a paper from last January’s inaugural Pan-European Design Conference.
Elephantech Launches World’s Smallest-Class Copper Nanofiller
07/17/2025 | ElephantechJapanese deep-tech startup Elephantech has launched its cutting-edge 15 nm class copper nanofiller – the smallest class available globally. This breakthrough makes Elephantech one of the first companies in the world to provide such advanced material for commercial use.
Copper Price Surge Raises Alarms for Electronics
07/15/2025 | Global Electronics Association Advocacy and Government Relations TeamThe copper market is experiencing major turbulence in the wake of U.S. President Donald Trump’s announcement of a 50% tariff on imported copper effective Aug. 1. Recent news reports, including from the New York Times, sent U.S. copper futures soaring to record highs, climbing nearly 13% in a single day as manufacturers braced for supply shocks and surging costs.
I-Connect007 Editor’s Choice: Five Must-Reads for the Week
07/11/2025 | Andy Shaughnessy, Design007 MagazineThis week, we have quite a variety of news items and articles for you. News continues to stream out of Washington, D.C., with tariffs rearing their controversial head again. Because these tariffs are targeted at overseas copper manufacturers, this news has a direct effect on our industry.I-Connect007 Editor’s Choice: Five Must-Reads for the Week
Digital Twin Concept in Copper Electroplating Process Performance
07/11/2025 | Aga Franczak, Robrecht Belis, Elsyca N.V.PCB manufacturing involves transforming a design into a physical board while meeting specific requirements. Understanding these design specifications is crucial, as they directly impact the PCB's fabrication process, performance, and yield rate. One key design specification is copper thieving—the addition of “dummy” pads across the surface that are plated along with the features designed on the outer layers. The purpose of the process is to provide a uniform distribution of copper across the outer layers to make the plating current density and plating in the holes more uniform.