-
- News
- Books
Featured Books
- design007 Magazine
Latest Issues
Current IssueShowing Some Constraint
A strong design constraint strategy carefully balances a wide range of electrical and manufacturing trade-offs. This month, we explore the key requirements, common challenges, and best practices behind building an effective constraint strategy.
All About That Route
Most designers favor manual routing, but today's interactive autorouters may be changing designers' minds by allowing users more direct control. In this issue, our expert contributors discuss a variety of manual and autorouting strategies.
Creating the Ideal Data Package
Why is it so difficult to create the ideal data package? Many of these simple errors can be alleviated by paying attention to detail—and knowing what issues to look out for. So, this month, our experts weigh in on the best practices for creating the ideal design data package for your design.
- Articles
- Columns
- Links
- Media kit
||| MENU - design007 Magazine
AltiumLive 2022: Keep Your Boards From Screaming with Eric Bogatin’s EMI Tips
January 26, 2022 | Andy Shaughnessy, Design007 MagazineEstimated reading time: 10 minutes
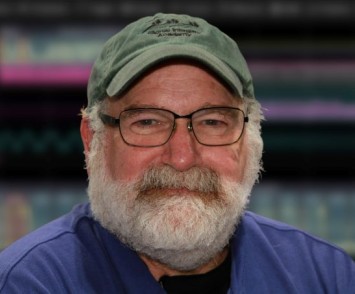
I recently spoke with Eric Bogatin, the “signal integrity evangelist,” about his AltiumLive keynote presentation, “How to Keep Your Boards from Screaming Like a Banshee.” Eric explains how attention to board structures during the early stages of PCB layout can keep EMI from becoming a problem in your design. He also discusses a feature of Altium Designer that some designers may not know about—a 2D field solver that's part of the Simbeor high-end electromagnetic measurement tool, but with a simple GUI that most designers can master right away.
Andy Shaughnessy: Eric, how are you? We’re here to discuss your upcoming presentation at AltiumLive. Tell us about your presentation. Are you going to scream like a banshee?
Eric Bogatin: No, but I do show a few examples of circuit boards that have been designed with what I call pathological features that will cause them to scream like a banshee. And I show scope measurements of a lot of noise on some of these boards. And I picked that title to refer to what I call pathological structures that are very common in a lot of boards I see, but they will almost always contribute to excess noise and should be avoided at all cost.
Shaughnessy: Is it like the definition of insanity, with designers doing the same thing over and over again and expecting different results?
Bogatin: Sure. I mention that I talk to a lot of students, a lot of engineers, and I hear this refrain over and over again. They say, “I don’t know why you’re telling me to change the way I design, because I’ve been building boards for 25 years and my boards work. And I don’t have to worry about all these things that you’re talking about.”
As you were saying, just because you’ve been doing the same thing repeatedly and your product worked, that doesn’t mean that it worked because of what you did. It may be working in spite of what you did. And you will absolutely encounter a design sometime in the future that’s pushing either shorter rise times, more signals, more current, or a lower noise margin. Those same design rules that might have worked in the past don’t work anymore.
There are two themes in this presentation: One is that after you figure out the connectivity, after all the things are connected the way they need to be connected in the schematic and then into the layout, then everything about the physical design and the layout is about noise control. And it’s really hard to use what you did in the last design as a measure of what’s good or bad if you’re not getting that feedback about how much noise you had. And, did it increase or decrease?
Just because it worked in the last design, if you’re not measuring the noise, you don’t know how bad it was. You don’t know how to use your judgment from the last design for future designs. I show examples of how to measure the excess noise that we care about and how to be sensitive to the impact of features on that noise.
Shaughnessy: It’s funny how EMI is still kind of like black magic for a lot of designers. I wonder why that is?
Bogatin: Well, EMI is hard to estimate. It’s hard to do the calculations. With single integrity, you can use rules of thumb, design guidelines, and you can try simple simulations. It does it really fast.
But for EMI it’s about far-field emissions, and gosh, that’s really hard to calculate with a simulation tool. The example I would show is that in order to fail an FCC Part 15 Class B test, all your product needs to do is radiate about 10 nanowatts of power in the narrow 120 kilohertz bandwidth. If you radiate more than 10 nanowatts of power in that bandwidth, you could fail an FCC test. That is an incredibly tiny amount of noise.
You can have the most beautiful, wonderful signal integrity design and power integrity design, but it doesn’t take very much to fail that FCC, EMI, or EMC test. Unfortunately, just because you pass signal integrity requirements, that isn’t a guarantee you’re going to pass the EMI or EMC emission tests. That’s part of why it’s such a big challenge.
Shaughnessy: What are some of the takeaways from your presentation?
Bogatin: The number one message is that you must have continuous return paths for your signals. As soon as you start violating that rule, if you have copper fill in a signal layer, for instance, those kinds of things will contribute to excess pathological noise.
I show examples of how you’re going to scream like a banshee if you don’t pay attention to those return paths. That’s the number one thing. It’s not the only thing, obviously, but it’s a really important thing. There’s another feature that I strongly recommend and I’ve had this discussion with other layout engineers: Is copper pour on signal layers good or bad? There are some mechanical issues about warpage and why it’s used, and even that is an important issue but a separate question. But electrically, is copper pour on signal layers good or bad? I have found in most of the designs that use copper pour, they add the copper pour on the top signal there because they have done a lot of routing in the ground planes and that’s their way of thinking, “I’m just going to throw copper out. That’s the return path. It’ll be good.”
But in fact, because of how the return currents find their way around, between going up and down and all around, even though you have shorting vias between the floating copper, your board can still radiate a lot. I show an example of a commercial two-layer board with copper pour on top and bottom, connected with return vias, and I show the same board designed with a nice return plane and the measured near-field radiate emissions from the bottom of the board; they’re literally orders of magnitude different.
It’s an example of why, if you don’t measure it, you don’t know. The noise that is there isn’t going to cause bit errors necessarily on these particular boards, but you have to measure the noise to know how bad it is.
Shaughnessy: If you don’t measure, you don’t know what you don’t know.
Bogatin: Yes, exactly. I show a couple different techniques of how to measure this kind of noise as well in the keynote. And then I’m doing another talk about a feature that I consider a hidden gem in Altium Designer that many engineers don’t know about. It’s a built-in 2D field solver. Altium signed a deal with Yuri Shlepnev’s company, Simberian. They’ve integrated the 2D field solver part of Simbeor into Altium Designer. It’s really easy to use, easy to access, but it requires enough mouse clicks that sometimes it’s hard to find. I show how to access the 2D field solver so that you can calculate with Yuri’s 2D field solver tool, what the characteristic impedance, is either analyze it or synthesize it, for stackup. It’s easy to use, and really accurate. And it’s available for anybody with Altium.
Shaughnessy: Wow. I know Yuri has a hell of a tool.
Bogatin: It is a great tool. He’s my go-to expert on electromagnetics and numerical simulation. But his tool itself, Simbeor, is not for the faint of heart. It’s a fully 3D field solver. You’ve got to know about using a fully 3D field solver. But the piece that’s integrated into Altium Designer uses their own user interface for it. So, it’s literally as easy as typing in some numbers on a calculator, and it only uses the engine behind the scenes, and it’s really accurate.
Shaughnessy: That sounds great. You don’t have to be an electromagnetics expert to use it.
Bogatin: No. I love this feature, and I don’t think it’s used enough. I don’t think engineers know about it enough or they’re intimidated. I show examples of how to access it and how to use it. And I compare it with a popular tool, Saturn PCB, that does kind of online calculations. And I show sometimes they’re comparable in accuracy, but other times they’re not. And how do you know? Well, that’s where if it’s available always use the 2D field solver, because you always get a more accurate result.
Shaughnessy: That’s great. I know a lot of the 3D field solvers are aimed at the users at the top of the “tool triangle” that we often talk about, mainly the signal integrity and EMC engineers by trade.
Bogatin: That’s right. Simbeor is a really powerful fully 3D field solver. It’s a little easier to use compared to some of the others, but all of them are hard to use because they’re dealing with very complicated effects. And that’s what’s great about what Altium did when they integrated it. There’s an easy-to-use user interface. That makes it trivial to you. Every layout engineer should be using it. I love that feature and I think more engineers should know about it. And if you got Altium, hey, you get the 2D field solver built into it.
Shaughnessy: Great. Anything else you want to mention?
Bogatin: I should mention two things. One I’ve got a couple new books out from Artech House that I think are really relevant for circuit board design. One of them is about designing transmission lines—designing, characterizing, and measuring transmission lines. The last book just came out a couple months ago about prototype design. I really think of it as an introduction to signal integrity. When do you worry about SI? I mentioned this concept: First you design for connectivity, and then you worry about noise control.
How do interconnects create noise? That means the interconnects are not electrically transparent anymore. How do they generate noise? I go through quite a lot of detail about how to think about interconnects and the noise they generate.
In this book, I also discuss risk reduction and just thinking about risk. When you’re building a prototype and you get a development schedule, the earlier in the design cycle you can find and fix problems, the shorter the development cycle, the lower the cost. So much of prototyping, the first article design, is about risk management. I talk a lot about how you engineer prototypes with high confidence that it’s going to work.
I use this as the textbook in my class on circuit board design at CU. When you’re getting your head around this idea of how to engineer the prototypes, thinking about interconnects being not transparent and managing the risk, you want to think of worst-case scenarios.
You want to fix the problems before they happen, rather than test it and then having to go back and fix it. You want to engineer the solutions in the design right at the beginning. Those two books are out now. I’m a professor at CU and editor of Signal Integrity Journal. I’m also a fellow at Teledyne LeCroy, which has graciously offered a three-month complimentary subscription to the Signal Integrity Academy website to all AltiumLive attendees.
If any attendees want to listen to the six signal integrity classes that I’ve done over the years, they’re all up at Signal Integrity Academy. There’s a little promo code in my presentation for a three-month complimentary subscription to the Signal Integrity Academy. If your I-Connect007 readers are interested, the promo code is ALT21. You can get you a three-month complimentary subscription.
Shaughnessy: Very good. Well, great talking to you, Eric. Thank you.
Bogatin: Thanks, Andy.
Watch Eric Bogatin's presentation “How to Keep Your Boards from Screaming Like a Banshee” below.
Suggested Items
I-Connect007 Editor’s Choice: Five Must-Reads for the Week
07/18/2025 | Nolan Johnson, I-Connect007It may be the middle of the summer, but the news doesn’t quit, and there’s plenty to talk about this week, whether you’re talking technical or on a global scale. When I have to choose six items instead of my regular five, you know it’s good. I start by highlighting my interview with Martyn Gaudion on his latest book, share some concerning tariff news, follow that up with some promising (and not-so-promising) investments, and feature a paper from last January’s inaugural Pan-European Design Conference.
Elephantech Launches World’s Smallest-Class Copper Nanofiller
07/17/2025 | ElephantechJapanese deep-tech startup Elephantech has launched its cutting-edge 15 nm class copper nanofiller – the smallest class available globally. This breakthrough makes Elephantech one of the first companies in the world to provide such advanced material for commercial use.
Copper Price Surge Raises Alarms for Electronics
07/15/2025 | Global Electronics Association Advocacy and Government Relations TeamThe copper market is experiencing major turbulence in the wake of U.S. President Donald Trump’s announcement of a 50% tariff on imported copper effective Aug. 1. Recent news reports, including from the New York Times, sent U.S. copper futures soaring to record highs, climbing nearly 13% in a single day as manufacturers braced for supply shocks and surging costs.
I-Connect007 Editor’s Choice: Five Must-Reads for the Week
07/11/2025 | Andy Shaughnessy, Design007 MagazineThis week, we have quite a variety of news items and articles for you. News continues to stream out of Washington, D.C., with tariffs rearing their controversial head again. Because these tariffs are targeted at overseas copper manufacturers, this news has a direct effect on our industry.I-Connect007 Editor’s Choice: Five Must-Reads for the Week
Digital Twin Concept in Copper Electroplating Process Performance
07/11/2025 | Aga Franczak, Robrecht Belis, Elsyca N.V.PCB manufacturing involves transforming a design into a physical board while meeting specific requirements. Understanding these design specifications is crucial, as they directly impact the PCB's fabrication process, performance, and yield rate. One key design specification is copper thieving—the addition of “dummy” pads across the surface that are plated along with the features designed on the outer layers. The purpose of the process is to provide a uniform distribution of copper across the outer layers to make the plating current density and plating in the holes more uniform.