-
- News
- Books
Featured Books
- design007 Magazine
Latest Issues
Current IssueAll About That Route
Most designers favor manual routing, but today's interactive autorouters may be changing designers' minds by allowing users more direct control. In this issue, our expert contributors discuss a variety of manual and autorouting strategies.
Creating the Ideal Data Package
Why is it so difficult to create the ideal data package? Many of these simple errors can be alleviated by paying attention to detail—and knowing what issues to look out for. So, this month, our experts weigh in on the best practices for creating the ideal design data package for your design.
Designing Through the Noise
Our experts discuss the constantly evolving world of RF design, including the many tradeoffs, material considerations, and design tips and techniques that designers and design engineers need to know to succeed in this high-frequency realm.
- Articles
- Columns
- Links
- Media kit
||| MENU - design007 Magazine
EIPC Summer Conference 2022: Day 2 Review
June 29, 2022 | Pete Starkey, I-Connect007Estimated reading time: 11 minutes
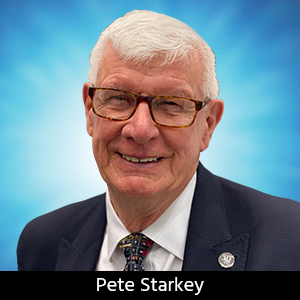
Örebro, Sweden on June 15 brought a bright and early start to Day 2 of the EIPC Summer Conference for those who had enjoyed the previous evening’s networking dinner, but had resisted the temptation to over-indulge or to carry on their long-awaited catch-up conversations with old friends into the small hours. All but a few were in their seats for 9 a.m., awake and attentive for Session 4 of the conference, on the theme of new process technologies, moderated by Martyn Gaudion, CEO of Polar Instruments.
As digital technologies continue to change the shape of electronics manufacturing, Dr. Kai Keller, director of business development with Notion Systems in Germany, put a perspective on the realities of additive digital processes with his reference to the Gartner Hype Cycle, the graphical depiction of a common pattern that arises with each new technological innovation. Beginning with a technology trigger, the curve rises rapidly through a peak of inflated expectation before promptly declining into a trough of disillusionment from which it progresses steadily up a slope of enlightenment and matures toward a plateau of productivity.
Commenting that manufacturing electronics is a wasteful undertaking, particularly regarding the consumption of enormous volumes of water, Dr. Keller set out to explore the potential for additive functional manufacturing of full electronic devices, taking as an example the inkjet printing of OLEDs from its origins in 2004 to the mass production of high resolution OLED monitors in 2021. “It might take long, but additive production processes will prevail in the end, simply because they make sense,” he said.
The focus of his presentation was the inkjet printing of solder mask on PCBs, and again he reviewed the history of its development from 2003 to the present day, when the technology is well proven and market adoption of inkjet solder mask is ongoing.
Keller outlined the principles of the process, discussed data preparation and full workflow integration, and reviewed the results. As well as high repeatability, the benefits of digital inkjet solder mask included no mask in holes, no mask on pads, adjustable thickness, and small and reliable solder dams. He went into detail on their natural bump profile: their wider base gave improved adhesion, with no undercut areas to trap chemicals or dirt. And he showed many real examples illustrating precise dimensional control.
The development team at Notion Systems continues to work on increasing the digital additive process window, and has realised more than 40 different additive production processes for conductives, dielectrics, resists, adhesives, active layers, optics, and coatings.
Novel nickel-free surface finishes for next-generation PCB technologies was the topic of the presentation from Dr. Kunal Shah, president and chief scientist at LiloTree in the United States.
Dr Shah remarked that high frequency PCBs was one of the fasted growing areas in the electronics industry and that a novel approach in surface finish was essential to obtain optimum performance and better reliability of electronic assemblies.
Although electroless nickel/immersion gold (ENIG) was currently the most widely used finish for high-end PCBs, it was not optimal for 5G frequencies because of high insertion loss due to the nickel layer. ENIG could also suffer from hyper-corrosion issues and brittle solder joint failures.
Current alternatives for 5G PCBs included direct immersion gold, electroless palladium immersion gold, and electroless palladium autocatalytic gold, although there were still concerns in terms of higher insertion loss and brittle solder joints. Higher thicknesses of precious metals were not cost-effective and not eco-friendly.
Shah described a novel nickel-free surface finish, with 50 nanometres of cyanide-free gold on copper treated with a nano-engineered barrier layer. The finish was characterised by robust solder joints with thin and distinct intermetallics. It was cost effective because of its significantly lower precious metal thickness than current alternatives. The new finish used a simple plating set-up of four process tanks and four rinse tanks.
The insertion loss of the nickel-free finish was almost identical to that of bare copper over the 0–100GHz frequency range, there was negligible change in contact resistance through six reflow cycles and the nano-engineered barrier layer prevented diffusion of copper into gold, leaving the surface corrosion-free. The process was cyanide-free, halogen-free, and RoHS and REACH compliant. As well as low insertion loss, it enabled robust solder joints with no brittle intermetallic failures.Page 1 of 3
Suggested Items
Driving Innovation: Direct Imaging vs. Conventional Exposure
07/01/2025 | Simon Khesin -- Column: Driving InnovationMy first camera used Kodak film. I even experimented with developing photos in the bathroom, though I usually dropped the film off at a Kodak center and received the prints two weeks later, only to discover that some images were out of focus or poorly framed. Today, every smartphone contains a high-quality camera capable of producing stunning images instantly.
Hands-On Demos Now Available for Apollo Seiko’s EF and AF Selective Soldering Lines
06/30/2025 | Apollo SeikoApollo Seiko, a leading innovator in soldering technology, is excited to spotlight its expanded lineup of EF and AF Series Selective Soldering Systems, now available for live demonstrations in its newly dedicated demo room.
Indium Corporation Expert to Present on Automotive and Industrial Solder Bonding Solutions at Global Electronics Association Workshop
06/26/2025 | IndiumIndium Corporation Principal Engineer, Advanced Materials, Andy Mackie, Ph.D., MSc, will deliver a technical presentation on innovative solder bonding solutions for automotive and industrial applications at the Global Electronics A
Fresh PCB Concepts: Assembly Challenges with Micro Components and Standard Solder Mask Practices
06/26/2025 | Team NCAB -- Column: Fresh PCB ConceptsMicro components have redefined what is possible in PCB design. With package sizes like 01005 and 0201 becoming more common in high-density layouts, designers are now expected to pack more performance into smaller spaces than ever before. While these advancements support miniaturization and functionality, they introduce new assembly challenges, particularly with traditional solder mask and legend application processes.
Knocking Down the Bone Pile: Tin Whisker Mitigation in Aerospace Applications, Part 3
06/25/2025 | Nash Bell -- Column: Knocking Down the Bone PileTin whiskers are slender, hair-like metallic growths that can develop on the surface of tin-plated electronic components. Typically measuring a few micrometers in diameter and growing several millimeters in length, they form through an electrochemical process influenced by environmental factors such as temperature variations, mechanical or compressive stress, and the aging of solder alloys.