-
- News
- Books
Featured Books
- design007 Magazine
Latest Issues
Current IssueShowing Some Constraint
A strong design constraint strategy carefully balances a wide range of electrical and manufacturing trade-offs. This month, we explore the key requirements, common challenges, and best practices behind building an effective constraint strategy.
All About That Route
Most designers favor manual routing, but today's interactive autorouters may be changing designers' minds by allowing users more direct control. In this issue, our expert contributors discuss a variety of manual and autorouting strategies.
Creating the Ideal Data Package
Why is it so difficult to create the ideal data package? Many of these simple errors can be alleviated by paying attention to detail—and knowing what issues to look out for. So, this month, our experts weigh in on the best practices for creating the ideal design data package for your design.
- Articles
- Columns
- Links
- Media kit
||| MENU - design007 Magazine
Microvias Can Be Stacked in Certain Package Densities
October 13, 2022 | I-Connect007 Editorial TeamEstimated reading time: 2 minutes
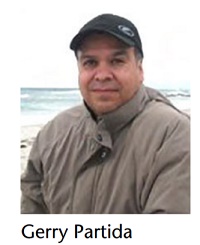
Summit Interconnect’s Gerry Partida recently spoke with the I-Connect007 Editorial Team about his research into root causes of weak microvias. Rather than a single manufacturing process cause, Gerry suggests that microvia reliability is the culmination of several material interactions and that contrary to popular belief, microvias can still be stacked in small, tight packaging densities. He highlights the need for simulation, as well as some of his findings that he plans to publish in a paper at IPC APEX EXPO 2023.
Nolan Johnson: Gerry, I understand your team has been doing some research into microvia stacking and will have a paper at the upcoming IPC APEX EXPO on this topic. What have you been learning?
Gerry Partida: Remember back in the early days of HDI, we would stack microvias as deep and plentiful as we wanted to? Then people started experiencing intermittent failures. Boards got hot, the components would fail, and it went back and forth. Manufacturing did something wrong, the assembler overbaked the boards, and it would go back and forth again. A lot of designs started to suffer, especially certain military products that would stack microvias. We would ask, “Why isn’t it working? Why does it work when it does work?” Most of the microvias that were stacked originally were small BGA packages. They were 0.4 mm or 0.5 mm, and those densities drove you to stack. These designs often were for the commercial OEMs, but if something failed, the commercial guys didn’t come back to discuss the issues.
But for the military guys who have ASICS that cost hundreds of thousands of dollars each, the stakes are much higher. If it is for space, then it can only be assembled once for flight; it cannot be taken off and reused. The military packaging then was a much wider pitch than the commercial guys who were stacking microvias initially.
When we looked at where the failures were happening, they were still happening with the commercial guys who were going three or four deep stacking microvias. They weren’t trying to make short, squatty, wide-diameter microvias because they were using thicker dielectrics to get wider lines for impedance. Consequently, we went for a time where there really didn’t seem to be a problem. Then it became, “We see a fracture at the target pad on the stack of the microvias,” and everybody thought there was a weakness in the electroless copper.
We all came up with these rules of thumb: Don’t stack more than two. A lot of DOEs were done, and they almost always concluded, “Do two stacks, then stagger off.” That seemed to work. Even fabricators we would work with had rules like, “Keep your aspect ratio for a single microvia at 0.75 to one. If you’re stacking them, keep them at 0.6 to one.” That seemed to work; we got good results.
Now, during this time we employed reflow resistance testing to monitor the strength of connections in the finished product. We started learning more about what works, and what doesn’t work. Some designs would slip through, where they do a three-stack on tight pitch, and they were passing. We were asking that if our rule of thumb was only two, then why is it working at three? When you look at the design, it’s a 0.4 mm pitch.
To read this entire conversation, which appeared in the September 2022 issue of PCB007 Magazine, click here.
Suggested Items
I-Connect007 Editor’s Choice: Five Must-Reads for the Week
07/11/2025 | Andy Shaughnessy, Design007 MagazineThis week, we have quite a variety of news items and articles for you. News continues to stream out of Washington, D.C., with tariffs rearing their controversial head again. Because these tariffs are targeted at overseas copper manufacturers, this news has a direct effect on our industry.I-Connect007 Editor’s Choice: Five Must-Reads for the Week
Digital Twin Concept in Copper Electroplating Process Performance
07/11/2025 | Aga Franczak, Robrecht Belis, Elsyca N.V.PCB manufacturing involves transforming a design into a physical board while meeting specific requirements. Understanding these design specifications is crucial, as they directly impact the PCB's fabrication process, performance, and yield rate. One key design specification is copper thieving—the addition of “dummy” pads across the surface that are plated along with the features designed on the outer layers. The purpose of the process is to provide a uniform distribution of copper across the outer layers to make the plating current density and plating in the holes more uniform.
Trump Copper Tariffs Spark Concern
07/10/2025 | I-Connect007 Editorial TeamPresident Donald Trump stated on July 8 that he plans to impose a 50% tariff on copper imports, sparking concern in a global industry whose output is critical to electric vehicles, military hardware, semiconductors, and a wide range of consumer goods. According to Yahoo Finance, copper futures climbed over 2% following tariff confirmation.
Happy’s Tech Talk #40: Factors in PTH Reliability—Hole Voids
07/09/2025 | Happy Holden -- Column: Happy’s Tech TalkWhen we consider via reliability, the major contributing factors are typically processing deviations. These can be subtle and not always visible. One particularly insightful column was by Mike Carano, “Causes of Plating Voids, Pre-electroless Copper,” where he outlined some of the possible causes of hole defects for both plated through-hole (PTH) and blind vias.
Trouble in Your Tank: Can You Drill the Perfect Hole?
07/07/2025 | Michael Carano -- Column: Trouble in Your TankIn the movie “Friday Night Lights,” the head football coach (played by Billy Bob Thornton) addresses his high school football team on a hot day in August in West Texas. He asks his players one question: “Can you be perfect?” That is an interesting question, in football and the printed circuit board fabrication world, where being perfect is somewhat elusive. When it comes to mechanical drilling and via formation, can you drill the perfect hole time after time?