-
- News
- Books
Featured Books
- design007 Magazine
Latest Issues
Current IssueAll About That Route
Most designers favor manual routing, but today's interactive autorouters may be changing designers' minds by allowing users more direct control. In this issue, our expert contributors discuss a variety of manual and autorouting strategies.
Creating the Ideal Data Package
Why is it so difficult to create the ideal data package? Many of these simple errors can be alleviated by paying attention to detail—and knowing what issues to look out for. So, this month, our experts weigh in on the best practices for creating the ideal design data package for your design.
Designing Through the Noise
Our experts discuss the constantly evolving world of RF design, including the many tradeoffs, material considerations, and design tips and techniques that designers and design engineers need to know to succeed in this high-frequency realm.
- Articles
- Columns
- Links
- Media kit
||| MENU - design007 Magazine
DFM 101: Final Finishes—HASL
February 14, 2023 | Anaya Vardya, American Standard CircuitsEstimated reading time: 3 minutes
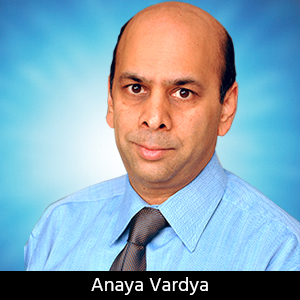
Introduction
One of the biggest challenges facing PCB designers is not understanding the cost drivers in the PCB manufacturing process. This article is the latest in a series that will discuss these cost drivers (from the PCB manufacturer's perspective) and the design decisions that will impact product reliability.
Final Finishes
Final finishes provide a surface for the component assembler to solder, wire bond, or conductively attach a component pad or lead to a pad, hole, or area of a PCB. The other use for a final finish is to provide a known contact resistance and life cycle for connectors, keys, or switches. The primary purpose of a final finish is to create electrical and thermal continuity with a surface of the PCB.
HASL (Hot Air Solder Leveling)
The next finish to discuss in this series is HASL. Choosing a surface finish means weighing the pros and cons associated with each, typically a combination of application, cost, and the properties of the finish. For example, Lead-free HASL is considered “RoHS” compliant (< 0.1% BW of finish, for Pb, Hg or Cd), while SnPb (tin/lead) HASL is not.
HASL is available in two versions: a tin/lead alloy and a lead-free option. HASL is a variable thickness metal alloy coating, typically 25 to 2000 µ in [0.65 to 50 µm] thick, designed to create a solderable surface and to maintain solderability over an extended period. Using specialized equipment, panels with exposed copper (pads and/or traces) are inserted into a vat of molten solder. A series of compressed hot-air knives then remove excess solder and “level” the surface before the solder solidifies and cools. HASL is the most prevalent and most solderable finish. Boards that have been HASL leveled will have a bright, silvery pad coloration. Solder thickness and uniformity on SMD pads is a function of pad size, pad orientation during processing, and HASL equipment. As pad size increases, thickness and uniformity decrease. This is caused by the high surface tension of solder and the airflow over pads that remove excess solder. Small pads (0.025" pitch SMD) will have a more uniform solder coating than large pads (0.050" x 0.050"). Large pads may be partially covered with a mound of solder while the rest of the pad is thin eutectic solder. Small pads may have the same condition depending on pad orientation during processing.
Pad orientation also contributes to solder thickness and uniformity. Fine-pitch SMD pads perpendicular to the direction of processing will have a uniform solder coating covering the entire pad. Fine-pitch SMD pads that are parallel to the direction of processing will have the leading half reduced to the thin eutectic solder with a mound of solder on the trailing half (eutectic solder is the optimum metal alloy to maximize solderability). Angled processing exposes both pad directions to similar air blasts resulting in more consistent pad thickness for similar pad sizes. 45-degree angle processing minimizes the pad orientation difference. HASL is not used for fine pitch components. This is because it increases fabrication and assembly rework for boards that have fine-pitch SMT devices with lead centers below 0.020" and presents coplanarity issues.
Pros and Cons of HASL
Pros
- Economical and widely available
- Excellent solderability
- Can be reworked at the fabricator
- Presents a very flat solder deposit
Cons
- Limited assembly reflow cycles, as the HASL process introduces a thermal shock before it gets to assembly
- Not suited for fine pitch (due to uneven surface height) or high aspect through-holes
- Standard SnPb HASL is not RoHS compliant
- Lead-free HASL requires different assembly soldering parameters
Understanding the cost drivers in PCB fabrication and early engagement between the designer and the fabricator are crucial elements that lead to cost-effective design success. Following your fabricator’s DFM guidelines is the first place to start.
Anaya Vardya is president and CEO of American Standard Circuits; co-author of The Printed Circuit Designer’s Guide to…?Fundamentals of RF/Microwave PCBs and The Printed Circuit Designer’s Guide to… Flex and Rigid-Flex Fundamentals; and author of The Printed Circuit Designer’s Guide to… Thermal Management: A Fabricator’s Perspective. Visit I-007eBooks.com to download these and other educational titles. He also co-authored “Fundamentals of Printed Circuit Board Technologies” and provides a discussion of flex and rigid flex PCBs at Real Time with… American Standard Circuits.
This article originally appeared in the January 2023 issue of Design007 Magazine.
Suggested Items
Driving Innovation: Direct Imaging vs. Conventional Exposure
07/01/2025 | Simon Khesin -- Column: Driving InnovationMy first camera used Kodak film. I even experimented with developing photos in the bathroom, though I usually dropped the film off at a Kodak center and received the prints two weeks later, only to discover that some images were out of focus or poorly framed. Today, every smartphone contains a high-quality camera capable of producing stunning images instantly.
Hands-On Demos Now Available for Apollo Seiko’s EF and AF Selective Soldering Lines
06/30/2025 | Apollo SeikoApollo Seiko, a leading innovator in soldering technology, is excited to spotlight its expanded lineup of EF and AF Series Selective Soldering Systems, now available for live demonstrations in its newly dedicated demo room.
Indium Corporation Expert to Present on Automotive and Industrial Solder Bonding Solutions at Global Electronics Association Workshop
06/26/2025 | IndiumIndium Corporation Principal Engineer, Advanced Materials, Andy Mackie, Ph.D., MSc, will deliver a technical presentation on innovative solder bonding solutions for automotive and industrial applications at the Global Electronics A
Fresh PCB Concepts: Assembly Challenges with Micro Components and Standard Solder Mask Practices
06/26/2025 | Team NCAB -- Column: Fresh PCB ConceptsMicro components have redefined what is possible in PCB design. With package sizes like 01005 and 0201 becoming more common in high-density layouts, designers are now expected to pack more performance into smaller spaces than ever before. While these advancements support miniaturization and functionality, they introduce new assembly challenges, particularly with traditional solder mask and legend application processes.
Knocking Down the Bone Pile: Tin Whisker Mitigation in Aerospace Applications, Part 3
06/25/2025 | Nash Bell -- Column: Knocking Down the Bone PileTin whiskers are slender, hair-like metallic growths that can develop on the surface of tin-plated electronic components. Typically measuring a few micrometers in diameter and growing several millimeters in length, they form through an electrochemical process influenced by environmental factors such as temperature variations, mechanical or compressive stress, and the aging of solder alloys.