-
- News
- Books
Featured Books
- pcb007 Magazine
Latest Issues
Current IssueThe Hole Truth: Via Integrity in an HDI World
From the drilled hole to registration across multiple sequential lamination cycles, to the quality of your copper plating, via reliability in an HDI world is becoming an ever-greater challenge. This month we look at “The Hole Truth,” from creating the “perfect” via to how you can assure via quality and reliability, the first time, every time.
In Pursuit of Perfection: Defect Reduction
For bare PCB board fabrication, defect reduction is a critical aspect of a company's bottom line profitability. In this issue, we examine how imaging, etching, and plating processes can provide information and insight into reducing defects and increasing yields.
Voices of the Industry
We take the pulse of the PCB industry by sharing insights from leading fabricators and suppliers in this month's issue. We've gathered their thoughts on the new U.S. administration, spending, the war in Ukraine, and their most pressing needs. It’s an eye-opening and enlightening look behind the curtain.
- Articles
- Columns
- Links
- Media kit
||| MENU - pcb007 Magazine
Developing Advanced Substrates for Die Packaging and Test
April 20, 2023 | Dan Turpuseema, AltanovaEstimated reading time: 2 minutes
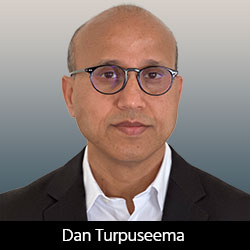
Semiconductor wafer-testing interface PCBs require a fine-pitch interposer/substrate to transfer a larger pitch (greater than 0.4 mm) to a fine pitch (less than 150 mm). The interposer, which serves as the electromechanical interface between the tester and the wafer requires fine pitch, high pin count, high I/O density, and vertical compliance.
Interposers are thus becoming a critical component for the testing interface. However, these boards are typically only available from a few high-end substrate manufacturers located in Asia. The associated longer lead times and single-source suppliers have made acquiring these boards a potential time-to-market showstopper for semiconductor manufacturers in need of them.
In early 2017, R&D Altanova (RDA) saw an opportunity in this space and began developing substrate technology to meet this need (Figure 1). In the beginning, we faced numerous challenges in identifying equipment, raw materials (e.g., dielectrics, process chemicals, and others), process know-how, and other requirements to accommodate low-volume, high-end applications.
Figure 1: This substrate for wafer probing is one example of the innovations developed by R&D Altanova to meet evolving manufacturing requirements.
Meeting the Need
Following a methodical approach, we used design of experiments (DOE) techniques to test different processes and materials on a small lab bench scale environment to check process yields, repeatability, reliability. This enabled us to slowly migrate to a low-volume semi-automatic production process for developing these new substrates.
Toward the end of 2017, we delivered the first 1-2-1 substrate 90 mm-pitch board with 10 mm lines and 15 mm spaces. Since then, we have continued to upgrade tools and develop processes to support high-end substrates.Today, we can build 12-2-12 or 12-n-12 (n-multilayer center core 24 layers), with 10 mm lines, 15 mm spaces for 100 mm x 100 mm boards.
Figure 2: This table lists the substrates R&D Altanova designed and manufactured between July and October 2022.
In 2022, we completed 50 new substrate designs and 3,500 PCBs of varying complexity (from 2-2-2 to 12-24-12) and board sizes (from 12 x 12 mm to 100 x 100 mm). Figure 2 lists the substrates we designed and manufactured between July and October 2022. Our primary focus was to build substrates for wafer testing, but supply-chain disruptions due to the COVID-19 pandemic opened a new market opportunity—creating substrates for die packaging. Figure 3 depicts a substrate cross-section, illustrating the low coefficient of thermal expansion (CTE) enabled by our approach, as well coplanarity and other specifics.
Figure 3: This example cross-section of substrate, post-thermal stress, illustrates the low CTE coplanarity and other beneficial parameters enabled by R&D Altanova’s development approach.
Looking Toward the Future
Even with supply-chain disruptions easing, we continue to add new customers to support the initial development work. This is due in large part to our ability to meet short delivery lead times of four to eight weeks, depending on project complexity.
We are excited to have expanded our offerings through the development of these innovative new substrates. As the demand for this technology continues to grow, we will continue to develop new substrates to meet customers’ requirements. Figure 4 shows our high-volume manufacturing (HVM) capabilities for redistribution layer (RDL) metal lift-off (MLO).
Figure 4: This table shows the manufacturing capabilities that R&D Altanova provides.
Acknowledgments
This development work was made possible thanks to the foresight of James Vincent Russell (R&D Circuits founder), the efforts of our stellar team of engineers, and the unflagging support of our president and CEO Seyed Paransun.
Dan Turpuseema is director of Substrate Technology, R&D Altanova (a subsidiary of Advantest America).
Suggested Items
Smarter Machines Use AOI to Transform PCB Inspections
06/30/2025 | Marcy LaRont, PCB007 MagazineAs automated optical inspection (AOI) evolves from traditional end-of-process inspections to proactive, in-line solutions, the integration of AI and machine learning is revolutionizing defect reduction and enhancing yields, marking a pivotal shift in how quality is managed in manufacturing.
Magnalytix and Foresite to Host Technical Webinar on SIR Testing and Functional Reliability
06/26/2025 | MAGNALYTIXMagnalytix, in collaboration with Foresite Inc., is pleased to announce an upcoming one-hour Webinar Workshop titled “Comparing SIR IPC B-52 to Umpire 41 Functional & SIR Test Method.” This session will be held on July 24, 2025, and is open to professionals in electronics manufacturing, reliability engineering, and process development seeking insights into new testing standards for climatic reliability.
The Death of the Microsection
06/26/2025 | Bob Neves, Reliability Assessment Solutions, Inc.I got my start out of college grinding and polishing PCB microsections. My thumbs are a bit arthritic today because of the experience (microsection grinders know what I mean). Back then, via structures were rather large, and getting to the center in six steps of grinding and polishing was easy compared to what my team has been doing recently at the lab.
Specially Developed for Laser Plastic Welding from LPKF
06/25/2025 | LPKFLPKF introduces TherMoPro, a thermographic analysis system specifically developed for laser plastic welding that transforms thermal data into concrete actionable insights. Through automated capture, evaluation, and interpretation of surface temperature patterns immediately after welding, the system provides unprecedented process transparency that correlates with product joining quality and long-term product stability.
Knocking Down the Bone Pile: Tin Whisker Mitigation in Aerospace Applications, Part 3
06/25/2025 | Nash Bell -- Column: Knocking Down the Bone PileTin whiskers are slender, hair-like metallic growths that can develop on the surface of tin-plated electronic components. Typically measuring a few micrometers in diameter and growing several millimeters in length, they form through an electrochemical process influenced by environmental factors such as temperature variations, mechanical or compressive stress, and the aging of solder alloys.