-
- News
- Books
Featured Books
- design007 Magazine
Latest Issues
Current IssueShowing Some Constraint
A strong design constraint strategy carefully balances a wide range of electrical and manufacturing trade-offs. This month, we explore the key requirements, common challenges, and best practices behind building an effective constraint strategy.
All About That Route
Most designers favor manual routing, but today's interactive autorouters may be changing designers' minds by allowing users more direct control. In this issue, our expert contributors discuss a variety of manual and autorouting strategies.
Creating the Ideal Data Package
Why is it so difficult to create the ideal data package? Many of these simple errors can be alleviated by paying attention to detail—and knowing what issues to look out for. So, this month, our experts weigh in on the best practices for creating the ideal design data package for your design.
- Articles
- Columns
- Links
- Media kit
||| MENU - design007 Magazine
Stop Over-specifying Your Materials
May 25, 2023 | I-Connect007 Editorial TeamEstimated reading time: 3 minutes
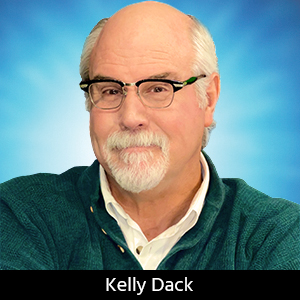
Columnist Kelly Dack has had a pretty wide range of experiences. As a PCB designer, he has sat behind the desk at an NPI company, an OEM, a fabricator, and now an EMS provider. We asked him to share a few thoughts on the materials selection process and how it could be improved.
Kelly also explains how overly zealous PCB designers make things too complicated by over-specifying their materials, which leads to confusion once the board goes to volume production overseas. Are you over-constraining your material choices?
Andy Shaughnessy: Kelly, what is your process for material selection? Walk us through it.
Kelly Dack: Sure. I actually wrote a guideline for our customers that explains the material selection process. As mentioned, over-specification in the EMS realm is rampant and problematic from the standpoint of scaling products to volume overseas. This guide has a section on laminated materials that includes a simple, tried-and-true material specification. It says, “Materials: laminated glass epoxy resin type FR-4 series or equivalent per IPC-4101 with a Tg of greater than or equal to xxx.” This is a number that we can modify. We say, for instance, 170°C, and a Td (time to delamination) temperature of greater than 3XX°C. Those are all movable numbers that designers can edit.
That’s how we specify our laminate materials for printed circuit boards, unless the performance criteria dictates that it needs to go further and get more specific—for example, high-performance signal integrity constraints, impedance control, or exotic materials. But otherwise, FR-4 laminates cover 85–95% of our customers’ design requirements.
Shaughnessy: Where do designers typically go to find this information? What documents or guidelines should they use?
Dack: Many designers use their company’s documentation template or go to their elders and learn through knowledge that has been passed down. I just went through a bunch of our customers’ designs and fabrication drawings, and I found plenty of examples of customer material specification. Many of them call out a specific IPC-4101 slash number, and it’s usually the same slash number each time. It’s either 4101/26 or /21.
Shaughnessy: IPC has said that slash sheets were not ever meant for designers to use; they’re mainly a way for PCB supplier purchasing and marketing departments to communicate with buyers.
Dack: I’m glad to hear that confirmation as it was my understanding as well. This all came from the MIL-S-13949 spec back in the mil-spec days, most of which has been replaced by IPC standards. But we are seeing some of our customers’ designs specifying laminates by using slash numbers and I get the feeling it’s just because of tribal knowledge. If you look at most of the designs, they appear to be basic, not really requiring a specific material. The board would work fine with a generic glass-epoxy laminate because it has no impedance control or performance criteria. We just print and etch some copper onto it, create a circuit, and it moves electrons.
It’s usually only when we get into the super high-speed design in the gigahertz range where we have to start thinking about loss tangents and permittivities. Here’s the challenge: How much do you constrain? If you’re building your PCB design down at the local prototype shop, which will build a board any way you want, everybody seems fat and happy. But when you want to build 1 million boards, you must introduce a low-cost constraint because you can’t pay $1,000 a board and make a profit. You scale to volume to get cost savings. To realize maximum cost savings, this has always been done offshore. But designers must realize that offshore suppliers don’t have access to all the materials and capabilities that U.S. prototype companies have. Over-specification of laminate materials by composition, performance characteristics, or a trademarked source creates a terrible, but avoidable ordering situation, putting quotes on hold every single day. The simple fact is that it causes our offshore PCB suppliers to request and obtain approval for material substitutions before they can proceed.
To read this entire conversation, which appeared in the May 2023 issue of Design007 Magazine, click here.
Suggested Items
I-Connect007 Editor’s Choice: Five Must-Reads for the Week
07/11/2025 | Andy Shaughnessy, Design007 MagazineThis week, we have quite a variety of news items and articles for you. News continues to stream out of Washington, D.C., with tariffs rearing their controversial head again. Because these tariffs are targeted at overseas copper manufacturers, this news has a direct effect on our industry.I-Connect007 Editor’s Choice: Five Must-Reads for the Week
Digital Twin Concept in Copper Electroplating Process Performance
07/11/2025 | Aga Franczak, Robrecht Belis, Elsyca N.V.PCB manufacturing involves transforming a design into a physical board while meeting specific requirements. Understanding these design specifications is crucial, as they directly impact the PCB's fabrication process, performance, and yield rate. One key design specification is copper thieving—the addition of “dummy” pads across the surface that are plated along with the features designed on the outer layers. The purpose of the process is to provide a uniform distribution of copper across the outer layers to make the plating current density and plating in the holes more uniform.
Trump Copper Tariffs Spark Concern
07/10/2025 | I-Connect007 Editorial TeamPresident Donald Trump stated on July 8 that he plans to impose a 50% tariff on copper imports, sparking concern in a global industry whose output is critical to electric vehicles, military hardware, semiconductors, and a wide range of consumer goods. According to Yahoo Finance, copper futures climbed over 2% following tariff confirmation.
Happy’s Tech Talk #40: Factors in PTH Reliability—Hole Voids
07/09/2025 | Happy Holden -- Column: Happy’s Tech TalkWhen we consider via reliability, the major contributing factors are typically processing deviations. These can be subtle and not always visible. One particularly insightful column was by Mike Carano, “Causes of Plating Voids, Pre-electroless Copper,” where he outlined some of the possible causes of hole defects for both plated through-hole (PTH) and blind vias.
Trouble in Your Tank: Can You Drill the Perfect Hole?
07/07/2025 | Michael Carano -- Column: Trouble in Your TankIn the movie “Friday Night Lights,” the head football coach (played by Billy Bob Thornton) addresses his high school football team on a hot day in August in West Texas. He asks his players one question: “Can you be perfect?” That is an interesting question, in football and the printed circuit board fabrication world, where being perfect is somewhat elusive. When it comes to mechanical drilling and via formation, can you drill the perfect hole time after time?