-
- News
- Books
Featured Books
- pcb007 Magazine
Latest Issues
Current IssueSales: From Pitch to PO
From the first cold call to finally receiving that first purchase order, the July PCB007 Magazine breaks down some critical parts of the sales stack. To up your sales game, read on!
The Hole Truth: Via Integrity in an HDI World
From the drilled hole to registration across multiple sequential lamination cycles, to the quality of your copper plating, via reliability in an HDI world is becoming an ever-greater challenge. This month we look at “The Hole Truth,” from creating the “perfect” via to how you can assure via quality and reliability, the first time, every time.
In Pursuit of Perfection: Defect Reduction
For bare PCB board fabrication, defect reduction is a critical aspect of a company's bottom line profitability. In this issue, we examine how imaging, etching, and plating processes can provide information and insight into reducing defects and increasing yields.
- Articles
- Columns
- Links
- Media kit
||| MENU - pcb007 Magazine
Estimated reading time: 1 minute
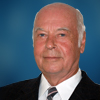
Contact Columnist Form
Pressure in Hot Roll Lamination of Dry Film Photoresist
Lamination Pressure
In lamination, we are trying to achieve good contact between the resist and the substrate surface by making the resist flow to conform to the surface topography. Flow is achieved by lowering the resist viscosity through heat, and by applying a pressure differential for a certain time to cause the flow. The photoresist is exposed to these conditions depends on the rpm of the hot rolls, the hot roll diameter, and to some extent on the pressure as it affects the footprint width in the nip. The pressure may be transmitted to the lamination rolls pneumatically, hydraulically, mechanically, or a combination of these means. This column focuses on pressure as an important variable that needs to be controlled and optimized.
Non-uniform pressure can cause a variety of problems such as dry film resist wrinkles shown in Figure 1.
If the hot roll surface has a localized recessed area (e.g., a cut caused by a knife during manual trimming of film), this will be a spot of low pressure, resulting in poor resist conformation to the board surface, which in turn can cause opens in a print and etch process.
Conversely, if there is a protrusion on the roll surface (e.g., caused by a particle adhering to the roll surface) this becomes a spot of high pressure, which causes resist thinning that can lead to a variety of defects.
It is well understood that higher lamination pressure will result in improved dry film resist conformation to the board surface. However, there are practical limitations to increasing the lamination pressure due to the design of a particular model of automatic cut sheet laminator. Even if a high-pressure setting is compatible with the design of the laminator, it may be difficult to take advantage of the higher pressure because the lamination rolls bend under the increased pressure. Roll bending results in an uneven roll footprint on the resist. The footprint is narrow at the center of the rolls and wider at the ends. This means that the pressure on the resist at the center is less than at the ends (Figure 2).
Read the full column here.
Editor's Note: This column originally appeared in the August 2014 issue of The PCB Magazine.
More Columns from Karl's Tech Talk
Karl's Tech Talk: Digital Imaging UpdateKarl’s Tech Talk: Electronic Packaging Levels
Green Legislation and the Impact on Electronic Materials and Processes
Digital Imaging Revisited
Dry Film Photoresist Thickness Selection Criteria
Quick-Turn Circuit Board Shops
Optical Interconnects
Signal Loss