-
- News
- Books
Featured Books
- design007 Magazine
Latest Issues
Current IssueShowing Some Constraint
A strong design constraint strategy carefully balances a wide range of electrical and manufacturing trade-offs. This month, we explore the key requirements, common challenges, and best practices behind building an effective constraint strategy.
All About That Route
Most designers favor manual routing, but today's interactive autorouters may be changing designers' minds by allowing users more direct control. In this issue, our expert contributors discuss a variety of manual and autorouting strategies.
Creating the Ideal Data Package
Why is it so difficult to create the ideal data package? Many of these simple errors can be alleviated by paying attention to detail—and knowing what issues to look out for. So, this month, our experts weigh in on the best practices for creating the ideal design data package for your design.
- Articles
- Columns
- Links
- Media kit
||| MENU - design007 Magazine
Failure Mode: Hole Wall Pullaway
September 16, 2015 | Paul Reid, ConsultantEstimated reading time: 1 minute
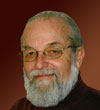
Hole wall pullaway (HWPA) is an insidious defect that is not usually a cause of electrical failure. What happens with HWPA is that the copper plating in a plated through-hole (PTH) is pulled away from the dielectric of the drilled hole wall. The hole must not be filled with any sort of a hole fill in order to see HWPA.
There are two distinct types of HWPA: stress-relieving and stress-inducing. In stress-relieving HWPA, the condition appears to distress the PTH, allowing it to survive hundreds or thousands of thermal cycles without failure. In stress-inducing HWPA, the stress appears to greatly increase, causing the PTH to fail in just a few thermal cycles. What we consider a failure is an increase greater than 10% in the overall resistance in the circuit. A crack that partially bridges the copper at the internal interface is enough to cause a failure.
This column is based on my experience in test reliability of interconnect stress test (IST) coupons. I am addressing HWPA that features moderate to severe outgassing. There may be HWPA due to thermal stressing of the board without any significant outgassing, but this type of HWPA is subtle, and it presents as a dark line between the plating and the dielectric of the hole wall. This type of HWPA is rarely detected.
Stress-Relieving HWPA
Stress-relieving is the most common type of HWPA. It appears that the adhesion of copper plating to the dielectric is reduced most likely due to problems with the application of electroless copper plating adhering to the dielectric of the hole wall. At the same time, the adhesion is strong at the copper’s internal interconnection. In fact, experience suggests that the adhesion of the electroless copper is stronger than the copper plating. This process frequently produces strong interconnections to copper inner layers. This condition may result in a hole wall that looks like a stack of forward or backward “Ds” running the length of the hole where the top and the bottom of the “Ds” is at an internal interconnect.
To read this entire article, which appeared in the August 2015 issue of The PCB Design Magazine, click here.
Suggested Items
I-Connect007 Editor’s Choice: Five Must-Reads for the Week
07/11/2025 | Andy Shaughnessy, Design007 MagazineThis week, we have quite a variety of news items and articles for you. News continues to stream out of Washington, D.C., with tariffs rearing their controversial head again. Because these tariffs are targeted at overseas copper manufacturers, this news has a direct effect on our industry.I-Connect007 Editor’s Choice: Five Must-Reads for the Week
Digital Twin Concept in Copper Electroplating Process Performance
07/11/2025 | Aga Franczak, Robrecht Belis, Elsyca N.V.PCB manufacturing involves transforming a design into a physical board while meeting specific requirements. Understanding these design specifications is crucial, as they directly impact the PCB's fabrication process, performance, and yield rate. One key design specification is copper thieving—the addition of “dummy” pads across the surface that are plated along with the features designed on the outer layers. The purpose of the process is to provide a uniform distribution of copper across the outer layers to make the plating current density and plating in the holes more uniform.
Trump Copper Tariffs Spark Concern
07/10/2025 | I-Connect007 Editorial TeamPresident Donald Trump stated on July 8 that he plans to impose a 50% tariff on copper imports, sparking concern in a global industry whose output is critical to electric vehicles, military hardware, semiconductors, and a wide range of consumer goods. According to Yahoo Finance, copper futures climbed over 2% following tariff confirmation.
Happy’s Tech Talk #40: Factors in PTH Reliability—Hole Voids
07/09/2025 | Happy Holden -- Column: Happy’s Tech TalkWhen we consider via reliability, the major contributing factors are typically processing deviations. These can be subtle and not always visible. One particularly insightful column was by Mike Carano, “Causes of Plating Voids, Pre-electroless Copper,” where he outlined some of the possible causes of hole defects for both plated through-hole (PTH) and blind vias.
Trouble in Your Tank: Can You Drill the Perfect Hole?
07/07/2025 | Michael Carano -- Column: Trouble in Your TankIn the movie “Friday Night Lights,” the head football coach (played by Billy Bob Thornton) addresses his high school football team on a hot day in August in West Texas. He asks his players one question: “Can you be perfect?” That is an interesting question, in football and the printed circuit board fabrication world, where being perfect is somewhat elusive. When it comes to mechanical drilling and via formation, can you drill the perfect hole time after time?