-
- News
- Books
Featured Books
- design007 Magazine
Latest Issues
Current IssueAll About That Route
Most designers favor manual routing, but today's interactive autorouters may be changing designers' minds by allowing users more direct control. In this issue, our expert contributors discuss a variety of manual and autorouting strategies.
Creating the Ideal Data Package
Why is it so difficult to create the ideal data package? Many of these simple errors can be alleviated by paying attention to detail—and knowing what issues to look out for. So, this month, our experts weigh in on the best practices for creating the ideal design data package for your design.
Designing Through the Noise
Our experts discuss the constantly evolving world of RF design, including the many tradeoffs, material considerations, and design tips and techniques that designers and design engineers need to know to succeed in this high-frequency realm.
- Articles
- Columns
- Links
- Media kit
||| MENU - design007 Magazine
Sensible Design: When Coatings Go Wrong
August 23, 2016 | Phil Kinner, ElectrolubeEstimated reading time: 2 minutes
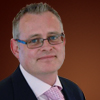
This month, I consider some of the more common, and often very frustrating, problems that may be encountered when coating electronic circuit boards and components. I also discuss some practical solutions.
As we all know, nothing in life is straightforward. In any engineering discipline, if there is the slightest chance that something might go wrong, you can bet your bottom dollar that it will. The secret is to be prepared for it. For the purposes of this column, I’m going to concentrate on the use of conformal coatings for the protection of electronic assemblies, highlighting some of the potential pitfalls associated with the choice of coating and the method of application. In each case, I will suggest an approach that should mitigate the majority of problems you are likely to encounter.
Problem: The quality and performance of a conformal coating material could be compromised according to the method of application.
This issue is commonly encountered when a product is transferred from one circuit manufacturer to another; for example, a product may be dip-coated in one country but selectively coated in another, with the specification requiring that the same material be used at both sites. The problem that arises here, however, is that using a material formulated for dip-coating in selective coating equipment can result in poor yield due to excessively fast drying and bubble entrapment.
One of my customers spent six months trying to solve a bubble issue internally, without realising that the root cause of this problem lay in the material formulation. After working with the customer, we found that by changing the solvent blend, the bubble entrapment issue could easily be resolved. Moreover, this solution simplified the process and reduced the cycle time. And since the non-volatile formulation remained the same, there was no need to re-qualify.
Problem: Achieving incorrect coating thickness, especially with acrylics.
The IPC specification allows a dry film thickness of between 30 and 130 microns, with the greater thickness being achieved by the application of multiple coating layers. Trying to achieve a 130-micron dry film thickness from a single selective-coating process with a solvent-based acrylic material is a recipe for a disaster, likely to result in excessive bubble formation, film shrinkage, coating delamination and additional stress on components. The result is poorer protection, rather than an improved overall level of circuit protection. Aiming for a uniform 30-50 microns and focusing on achieving perfect coverage at each application is a much better approach to improving the protection of electronic circuits.
Achieving the correct coating thickness is important; bear in mind that if the coating is too thick it can lead to entrapment of solvents in areas where the coating does not fully cure. Similarly, it can cause the coating to crack as it cures or as the result of changes in temperature, or due to mechanical shock and vibration.
To read this entire article, which appeared in the July 2016 issue of The PCB Design Magazine, click here.
Suggested Items
The Global Electronics Association Releases IPC-8911: First-Ever Conductive Yarn Standard for E-Textile Application
07/02/2025 | Global Electronics AssociationThe Global Electronics Association announces the release of IPC-8911, Requirements for Conductive Yarns for E-Textiles Applications. This first-of-its-kind global standard establishes a clear framework for classifying, designating, and qualifying conductive yarns—helping to address longstanding challenges in supply chain communication, product testing, and material selection within the growing e-textiles industry.
IPC-CFX, 2.0: How to Use the QPL Effectively
07/02/2025 | Chris Jorgensen, Global Electronics AssociationIn part one of this series, we discussed the new features in CFX Version 2.0 and their implications for improved inter-machine communication. But what about bringing this new functionality to the shop floor? The IPC-CFX-2591 QPL is a powerful technical resource for manufacturers seeking CFX-enabled equipment. The Qualified Product List (QPL) helps streamline equipment selection by listing models verified for CFX compliance through a robust third-party virtual qualification process.
Advancing Aerospace Excellence: Emerald’s Medford Team Earns Space Addendum Certification
06/30/2025 | Emerald TechnologiesWe’re thrilled to announce a major achievement from our Medford, Oregon facility. Andy Abrigo has officially earned her credentials as a Certified IPC Trainer (CIT) under the IPC J-STD-001 Space Addendum, the leading industry standard for space and military-grade electronics manufacturing.
Magnalytix and Foresite to Host Technical Webinar on SIR Testing and Functional Reliability
06/26/2025 | MAGNALYTIXMagnalytix, in collaboration with Foresite Inc., is pleased to announce an upcoming one-hour Webinar Workshop titled “Comparing SIR IPC B-52 to Umpire 41 Functional & SIR Test Method.” This session will be held on July 24, 2025, and is open to professionals in electronics manufacturing, reliability engineering, and process development seeking insights into new testing standards for climatic reliability.
IPC Rebrands as Global Electronics Association: Interview With Dr. John W. Mitchell
06/22/2025 | Marcy LaRont, I-Connect007Today, following a major announcement, IPC is embracing the rapid advancement of technology with a bold decision to change its name to the Global Electronics Association. This name more accurately reflects the full breadth of its work and the modern realities of electronics manufacturing. In this exclusive interview, Global Electronics Association President and CEO Dr. John W. Mitchell shares the story behind the rebrand: Why now, what it means for the industry, and how it aligns with the organization’s mission.