-
- News
- Books
Featured Books
- design007 Magazine
Latest Issues
Current IssueProper Floor Planning
Floor planning decisions can make or break performance, manufacturability, and timelines. This month’s contributors weigh in with their best practices for proper floor planning and specific strategies to get it right.
Showing Some Constraint
A strong design constraint strategy carefully balances a wide range of electrical and manufacturing trade-offs. This month, we explore the key requirements, common challenges, and best practices behind building an effective constraint strategy.
All About That Route
Most designers favor manual routing, but today's interactive autorouters may be changing designers' minds by allowing users more direct control. In this issue, our expert contributors discuss a variety of manual and autorouting strategies.
- Articles
- Columns
- Links
- Media kit
||| MENU - design007 Magazine
Estimated reading time: 1 minute
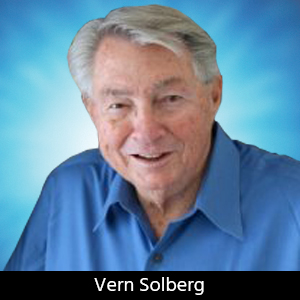
Embedding Components, Part 2
Technology and processes for embedding capacitor and inductor elements rely on several unique methodologies. Regarding providing capacitor functions, IPC-4821 defines two methodologies for forming capacitor elements within the PCB structure: laminate-based (copper-dielectric-copper) or planar process and non-laminate process using deposited dielectric materials.
Distributed (planar) capacitors
Considered the simplest solution and commonly used to replace discrete power supply decoupling capacitors the planar capacitors utilize closely spaced power and ground planes separated by a thin dielectric layer. The dielectric can be a layer of the glass-reinforced epoxy material, a thin layer of non-reinforced polymer, or a polymer sheet material filled with ceramic powder. This technique will provide significant capacitance and delivers very low inductance. The capacitance range for planar capacitors is 1pF to 1mF, dependent on the dielectric constant, material thickness and area.
Because the planar capacitance is proportional to the dielectric thickness between the power and ground planes, thin dielectrics are preferred. This will increase planar capacitance while reducing planar spreading inductance and minimizes overall board thickness. The reduction of planar spreading inductance also results in a lowering the impedance path while increasing the effectiveness of discrete capacitances.
The total capacitance of the power and ground pair is determined by the effective common (overlapping) area of the copper electrodes. This area, times the capacitance density, represents the total capacitance.
To read this entire article, which appeared in the June 2017 issue of The PCB Design Magazine, click here.
More Columns from Designer's Notebook
Designers Notebook: Basic PCB Planning Criteria—Establishing Design ConstraintsDesigners Notebook: Layer Stackup Planning for RF Circuit Boards
Designers Notebook: Addressing Future Challenges for Designers
Designers Notebook: Impact of Advanced Semiconductor Packaging on PCB Stackup
Designers Notebook: Implementing HDI and UHDI Circuit Board Technology
Designer's Notebook: Heterogeneous Integration and High-density SiP Technologies
Designers Notebook: PCB Design and IPC-CFX for Assembly Automation
Designer’s Notebook: What Designers Need to Know About Manufacturing, Part 2