-
- News
- Books
Featured Books
- smt007 Magazine
Latest Issues
Current IssueSupply Chain Strategies
A successful brand is built on strong customer relationships—anchored by a well-orchestrated supply chain at its core. This month, we look at how managing your supply chain directly influences customer perception.
What's Your Sweet Spot?
Are you in a niche that’s growing or shrinking? Is it time to reassess and refocus? We spotlight companies thriving by redefining or reinforcing their niche. What are their insights?
Moving Forward With Confidence
In this issue, we focus on sales and quoting, workforce training, new IPC leadership in the U.S. and Canada, the effects of tariffs, CFX standards, and much more—all designed to provide perspective as you move through the cloud bank of today's shifting economic market.
- Articles
- Columns
- Links
- Media kit
||| MENU - smt007 Magazine
Estimated reading time: 4 minutes
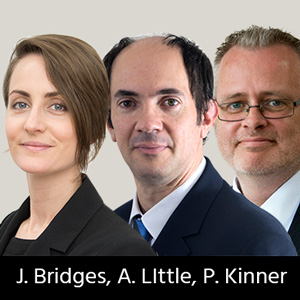
Conformal Coatings: An Evolving Science
In my previous column, I touched upon the environmental impact of conformal coatings and how the industry is striving to find new formulations—principally water-based, solvent-free materials—that have minimal environmental impact. In this column, I will return to the Q&A formula that my colleagues have adopted in past issues and attempt to answer trending queries from our customer base on coating properties, selections, and applications.
In addition, I hope to shed more light on coating problems posed by electronics miniaturization, which is certainly exercising the minds of designers and production engineers from a growing cohort of customers in the consumer electronics sector. Without further ado, here are five of the best questions that frequently arise when we enter preliminary consultations with our clients.
In an ideal world, what combination of properties would a coating exhibit?
The performance requirements of conformal coatings continue to become ever-challenging as electronic assemblies are subjected to increasingly hostile operating environments. The perfect conformal coating would retain high elasticity at both high and low temperature extremes and maintain its properties at high temperatures with no out-gassing. It would also provide an excellent barrier to moisture in humid environments and where there is a risk of liquid water splash. It would be highly resistant to solvents and corrosive gases but be easy to remove when repairs or modifications need to be carried out. Ultimately, the perfect coating would be intelligent, self-applying, and free of charge—but that’s a whole different ball game!
On a more serious note, an ideal coating should also be solvent-free, and as I pointed out in my previous column in this series, there has been some progress in this area. A new range of innovative VOC-free, fast-curing, high-performance two-part conformal coatings are now available for application by selective coating. The two-part (2K) solvent-free selective coating process is an enabling technological breakthrough that allows all their benefits to be realized.
How does the design of the board impact the choice of coating material?
The design of the board doesn’t directly affect the choice of coating material, although it will determine which application methods can be used to apply the coating. Certain materials are difficult to use in a dip process due to the material curing prematurely (e.g., moisture curing and UV-curable materials), so it could be said that the choice of coating is indirectly related to the board design.
The use of single component UV-curable materials has grown significantly over the past decade with rapid cure yielding productivity benefits for many. However, the current single- part UV materials often suffer cure issues when applied to boards containing tall components that shadow the exposure to UV light and necessitate out-of-focus cure heights and reduce light intensity and degree of cure. Consequently, a secondary cure mechanism must be introduced into UV curing—typically a moisture-activated or heat-activated mechanism.
What electrical properties are typically required of conformal coatings?
Conformal coatings form a protective, insulating layer. The most common electrical parameter tested is surface insulation resistance (SIR) testing, a measurement often taken before and after coating and subsequent exposure to harsh conditions to determine the long-term insulation performance of the coating. The coating should also have high dielectric strength, the minimum level required determined by the inter-track separation and potential difference between adjacent tracks.
Dielectric properties are an important consideration where the signal integrity of the circuit is concerned. Conformal coatings applied to such circuits must not affect signal integrity and the coating’s dielectric constant and loss are parameters that must be considered when making a material selection and determining the coating thickness. Other than this, dielectric strength, breakdown, and withstand are commonly measured and reported properties that enable designers to ensure sufficient spacing between components and determine how much closer components can be spaced than without coating materials applied.
How is the best application method of coating materials defined?
There isn’t necessarily a best method to apply a conformal coating. The application method chosen for an assembly will depend upon what existing equipment is available to the manufacturer, the coating processes in use, take time (the average time interval between the start of production of one unit and the start of the next), and the design of the assembly. This includes areas of the circuit that must be coated and those that must not (connectors, switches, etc.).
The best application method would ensure that each board to be coated receives coating coverage on all required metal surfaces at a sufficient thickness to afford protection against the environment. These requirements will change from each board design and environment and will invariably need to be tested and verified ahead of the production run.
How has the trend for miniaturization affected the development of coatings?
The trend towards miniaturization is most evident in consumer electronics and has led to the development of ultra-thin coating materials with thicknesses of less than 12 microns. This, in combination with internal gasketing and better case design, has enabled the production of vastly more water-resistant mobile phones and other handheld devices.
In more traditional applications, such as aerospace and automotive, there is a double issue of finer pitch components (reduced space between conductors) and a need to reduce weight, resulting in less protection being afforded by the board’s housing. The impact of this is that coatings need to function more as a primary mitigation strategy against the environment. As a result, the performance requirements of these coating materials have increased dramatically, especially with regards to condensation resistance.
Visit I-007eBooks to download your copy of Electrolube's micro eBook today:
The Printed Circuit Assembler's Guide to... Conformal Coatings for Harsh Environments
More Columns from Sensible Design
Sensible Design: Automotive Conformal Coating ApplicationsSensible Design: Green Coats Are In
Sensible Design: Encapsulation Resins—PU vs. Epoxy
Sensible Design: Avoiding Conformal Coating Pitfalls
Sensible Design: Comparing Traditional and Bio-based Resins
Sensible Design: All Resins Are Not Created Equal
Sensible Design: Can Solvent-free UV-cure Coatings Increase Stability and Throughput?
Sensible Design: Optimize Your Thermal Management