-
- News
- Books
Featured Books
- design007 Magazine
Latest Issues
Current IssueProper Floor Planning
Floor planning decisions can make or break performance, manufacturability, and timelines. This month’s contributors weigh in with their best practices for proper floor planning and specific strategies to get it right.
Showing Some Constraint
A strong design constraint strategy carefully balances a wide range of electrical and manufacturing trade-offs. This month, we explore the key requirements, common challenges, and best practices behind building an effective constraint strategy.
All About That Route
Most designers favor manual routing, but today's interactive autorouters may be changing designers' minds by allowing users more direct control. In this issue, our expert contributors discuss a variety of manual and autorouting strategies.
- Articles
- Columns
- Links
- Media kit
||| MENU - design007 Magazine
Insulectro Works to Bridge the Fabricator/Designer Gap
December 19, 2019 | Barry Matties, I-Connect007Estimated reading time: 14 minutes
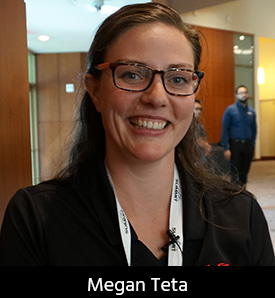
Barry Matties sat down with Insulectro’s Megan Teta and Mike Creeden to discuss trends they see in the materials market and how they’re working to bridge the gap between fabrication and design, including helping designers understand what they can do to make a board more manufacturable.
Barry Matties: First, give us a brief snippet of Insulectro and what you do.
Mega Teta: Insulectro sells all Isola and DuPont laminates in the industry. We’re aligned with some of the best-in-class suppliers. We also sell materials that go into almost every process inside of a PCB fabrication shop.
Matties: Mike, you recently joined Insulectro in a design engineering capacity. Talk a little bit about your new role.
Mike Creeden: I joined Insulectro this year in May as a technical director for design education. Our goal is that we can enable and empower our customers, the fabricators, and support the OEM market. Our goal is to help the OEMs make intelligent material decisions early.
Matties: One of the things that I hear in most of the presentations at AltiumLive Frankfurt is that materials matter very early on from the design point of view. Why is that so important?
Creeden: Megan and I were discussing that earlier. It’s part of the message we are attempting to bring to this week’s event. Materials matter now for three major reasons.
First, when a designer attempts to solve the layout, it’s often a very dense, complex physical layout puzzle. Materials are an integral part of the design because as circuitry becomes smaller, the pitch of the device is reduced, and you need to utilize reduced material sizes.
Second, as boards become smaller, their ability to be manufactured is more challenging.
And the third reason is circuit performance is getting higher. A higher-performance board has more criteria placed on the layout, and the material affects that because when most people connect to a board, they see a wire connecting two parts. They think that the voltage and current establish the transmission line, but that’s only partially true; they’re factors, but the energy exists within the dielectric material, which is the space between any signal or power plane and its return path. The materials matter because they are factors in the equation for signal/voltage performance.
Matties: And from your point of view, what trends are you seeing in materials right now?
Teta: We’re all about trying to maintain lower Dk and driving that loss down while still making the materials manufacturable. From the Isola side, all of our materials are glass-reinforced because it’s one of the easiest materials to drill, laminate, and maintain your registration and scalability, etc. We’re trying to use things like lower-Dk glasses and take copper foils that are thinner and thinner to drive all that loss down.
Matties: The last time I did an interview with Isola CEO Travis Kelly, we talked about the new factory being built. What’s the progress on that?
Teta: The presses are coming. In the U.S. market, prototyping is a big deal, so trying to get material as quickly as possible is critical. Also, with the high-speed digital market, there are a lot of different core offerings, so trying to keep all of that in stock is a little bit trickier. The new facility is aimed at making those laminates as quick as possible.
Matties: It seems like the strategy there were smaller lot sizes and more flexibility.
Teta: Exactly. There are going to be three brand new presses that will outperform old presses from the facility in Chandler, Arizona. These are going to be aimed at doing lower quantity with a higher mix.
Matties: One of the things that we hear a lot about is that the designers need to talk to the fabricators sooner than later. Part of the core strategy of Insulectro is bridging that gap, correct?
Creeden: Yes. If you complete your layout and then approach the fabricator, you may find out any one of your decisions along the line for solving the layout and feature size or satisfying electrical performance are unbuildable. If you’re finding that out at the end of the design phase, you may have to go back and start somewhere much earlier in the process, if not all the way at the beginning. Most companies’ design schedules cannot support that. Oftentimes, they will compromise, thus lowering the reliability, performance, or anything that might be unacceptable to their end customer.
Matties: Are you focusing on reaching OEMs and connecting them with fabricators with the designer in that mix? What’s your model?
Creeden: For the most part, OEMs already are connected to the fabricators, and Insulectro currently is working with most all fabricators. Our goal is to accomplish change together. Therefore, we call it our ACT (Accomplishing Change Together) Program, whereby we work with the fabricators, helping them support their customers. For example, we don’t want to suggest a new material at the last minute. If it’s a new material, we want the OEM to be in contact with their fabricator alerting them early. We’re eager to make sure that the fabricators are prepared to best serve the end goals. Timely material choices help to ensure adequate delivery, stocking, and that process issues are met. Megan can speak to delivery and stocking issues. We value being able to deliver all these materials very quickly.
Teta: Insulectro is a stocking distributor, and we also have some manufacturing, cutting down materials, drilling holes, etc. Our goal is to get the material as fast as possible. We’re also working on our customer portal and making sure the fabricators can see in real-time what’s in our inventory and where it is. For example, a fabricator might San Jose sometimes will call and go to pick up the material the same day; we’re able to do that because they can see what we have in stock.
With material availability, we also understand that we need to maintain certain standard materials that are always going to be in stock. And that’s what’s important about talking to the designers and ensuring that when they build their stack-ups, they use the materials that we have. Isola does a great job of having a lot of different things available, but you don’t want to have something that is going to be used by two different customers.
Matties: Back to my point about connecting the OEM with the fabricator, I understand that connection, but I was talking more about you going to the OEM and being the connector between the OEM and fabricators in many ways.
Teta: Our goal is to work with the fabricator and have them bring us into their customers, so we go on sales calls with the OEMs all the time.
Matties: It’s kind of the reverse. You’re becoming an extension of the fabrication marketing department with brilliant expertise.Page 1 of 2
Testimonial
"We’re proud to call I-Connect007 a trusted partner. Their innovative approach and industry insight made our podcast collaboration a success by connecting us with the right audience and delivering real results."
Julia McCaffrey - NCAB GroupSuggested Items
How Good Design Enables Sustainable PCBs
08/21/2025 | Gerry Partida, Summit InterconnectSustainability has become a key focus for PCB companies seeking to reduce waste, conserve energy, and optimize resources. While many discussions on sustainability center around materials or energy-efficient processes, PCB design is an often overlooked factor that lies at the heart of manufacturing. Good design practices, especially those based on established IPC standards, play a central role in enabling sustainable PCB production. By ensuring designs are manufacturable and reliable, engineers can significantly reduce the environmental impact of their products.
50% Copper Tariffs, 100% Chip Uncertainty, and a Truce
08/19/2025 | Andy Shaughnessy, I-Connect007If you’re like me, tariffs were not on your radar screen until a few months ago, but now political rhetoric has turned to presidential action. Tariffs are front-page news with major developments coming directly from the Oval Office. These are not typical times. President Donald Trump campaigned on tariff reform, and he’s now busy revamping America’s tariff policy.
Global PCB Connections: Understanding the General Fabrication Process—A Designer’s Hidden Advantage
08/14/2025 | Markus Voeltz -- Column: Global PCB ConnectionsDesigners don’t need to become fabricators, but understanding the basics of PCB fabrication can save you time, money, and frustration. The more you understand what’s happening on the shop floor, the better you’ll be able to prevent downstream issues. As you move into more advanced designs like HDI, flex circuits, stacked vias, and embedded components, this foundational knowledge becomes even more critical. Remember: the fabricator is your partner.
MKS’ Atotech to Participate in IPCA Electronics Expo 2025
08/11/2025 | AtotechMKS Inc., a global provider of enabling technologies that transform our world, announced that its strategic brands ESI® (laser systems) and Atotech® (process chemicals, equipment, software, and services) will showcase their latest range of leading manufacturing solutions for printed circuit board (PCB) and package substrate manufacturing at the upcoming 17th IPCA Show to be held at Pragati Maidan, New Delhi from August 21-23, 2025.
MKS Showcases Next-generation PCB Manufacturing Solutions at the Thailand Electronics Circuit Asia 2025
08/06/2025 | MKS Instruments, Inc.MKS Inc, a global provider of enabling technologies that transform our world, today announced its participation in Thailand Electronics Circuit Asia 2025 (THECA 2025), taking place August 20–22 at BITEC in Bangkok.