-
- News
- Books
Featured Books
- smt007 Magazine
Latest Issues
Current IssueSupply Chain Strategies
A successful brand is built on strong customer relationships—anchored by a well-orchestrated supply chain at its core. This month, we look at how managing your supply chain directly influences customer perception.
What's Your Sweet Spot?
Are you in a niche that’s growing or shrinking? Is it time to reassess and refocus? We spotlight companies thriving by redefining or reinforcing their niche. What are their insights?
Moving Forward With Confidence
In this issue, we focus on sales and quoting, workforce training, new IPC leadership in the U.S. and Canada, the effects of tariffs, CFX standards, and much more—all designed to provide perspective as you move through the cloud bank of today's shifting economic market.
- Articles
- Columns
- Links
- Media kit
||| MENU - smt007 Magazine
Estimated reading time: 5 minutes
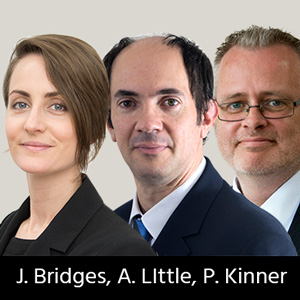
Sensible Design: Key Benefits of Resins and Differences From Coatings
Encapsulation resins are available in many forms, with numerous properties that would challenge even the most diligent chemist. While we appreciate that most manufacturers simply want a resin to do the job without wading through all the subtleties a resin has to offer, we also understand how critical it is to get the product detail right in order to make product selection as painless as possible. With so many varying options to protect electronic circuitry, there’s a lot of ground to cover. Depending on the application, sometimes a conformal coating may be more suitable, particularly with the two-part coating series that performs like a resin.
In this month’s column, I’m going to focus on the benefits of using a thermally conductive encapsulation resin and compare the difference between using a resin and a conformal coating. I will also look more closely at the best way to mix a resin pack and what to be wary of if air bubbles get trapped in the cured resin. Without further ado, let’s explore these frequently asked questions in our five-point format.
1. What are the benefits of a thermally conductive encapsulation resin?
As electronics have become smaller and more powerful over the years, the amount of heat generated per unit area on a PCB has increased as well, and it is well known that electronics will perform much better at low temperatures. Used for encapsulating PCBs or devices requiring effective thermal dissipation, thermally conductive resins are designed to allow heat to be dissipated away from sensitive components. The typical thermal conductivity of an unfilled resin is 0.20–0.35 W/mK. Whereas for a resin to be classified as being thermally conductive, it must have a thermal conductivity of >0.8W/mK. This is usually accomplished by using selected ceramic fillers, which offer a combination of thermal conductivity and chemical stability.
2. What are some key differences between resins and coatings?
The most noticeable differences are the methods of application (aerosol, conformal coating spray equipment, manual spray gun, and brushing for coatings, compared to mixing and dispensing equipment and resin packs for resins), the thickness of application (<100 microns for conformal coatings, <500 microns for thick coatings and >500 microns for resins), and approval ratings (coatings are generally approved to UL746, while for resins, it very much depends on the application). Because of the coating thickness, coatings occupy less space and have a low increase in overall weight compared to resins. There are both coatings and resins that are based on epoxy, polyurethane, and silicone chemistries, but there are also acrylate, acrylic, and parylene coatings that do not have a direct resin equivalent. 99% of resins are 100% solid systems, so they have low, or no VOCs released during curing, while many coatings are solvent-based, although there are two-component (2K) and UV curable acrylate systems that are also available as 100% solids.
3. Why would I choose a resin instead of a coating?
The choice between a resin or a coating is normally down to application specifics. If the unit involved is to be subject to long-term immersion in various chemicals, and subject to long-term thermal, and/or physical shock cycling, then a resin is generally preferred. Also, if there are a large number of large components on a PCB, it is generally better to use a resin to encapsulate these than to coat them. Another scenario where a resin would be preferable is when the unit will be used in a situation where it is not easily accessible, or long continuous service life is required. In this incidence, a resin would be recommended to provide the extra protection and durability needed.
4. What are the consequences of having air bubbles trapped in encapsulation resins, and does this impair performance?
Air bubbles can have a number of impacts upon the performance of the cured resin. Depending on the number and distribution of the bubbles, the actual thickness of the polymer layer applied will be decreased; hence, the level of protection will also be reduced, particularly against chemical attack. If there are air bubbles next to components, wiring, or tracks, then particularly when high voltages are applied, corona discharge can build up inside these voids and ultimately destroy the components or wiring. Voids also act ?as a weak point for thermal and physical shock, which can lead to the resin cracking in service.
5. Talk me through the best method for mixing a resin pack. Explain what can go wrong and why.
First, you need to remove the resin pack from the outer packaging. In the case of polyurethane and silicone resins, don’t remove them from the foil pack until ready to use. Lay the pack out onto a flat surface and remove the centre clip. Use the clip to push the resin from one half of the pack to the other, then pick the pack up in both hands and mix in a circular motion for a couple of minutes.
Place the pack back on the flat surface and use the clip to push the resin from the corners into the centre. Pick the pack up in both hands and continue mixing for a further minute.
Repeat pushing the resin from the corners into the centre of the pack and then continue to mix for another minute to ensure that the material is fully mixed and uniform colour. Use the clip to push the mixed resin to the side of the pack with the angled seam. Roll the pack film up so that the pack fits into the hand. Cut off the corner of the pack and then tilt the pack to dispense the resin, applying slight pressure as required to maintain the flow. If the material from the corners of the pack is not pushed into the centre of the pack, then unmixed material can be dispensed. If the resin is not mixed for long enough, then the resin may not cure, or it will have a patchy cure. In the case of filled resin systems, some sedimentation might have taken place over time, so it might take a little more mixing to ensure that the fillers are correctly distributed throughout the resin. With the optically clear resins, they will appear hazy when first mixed but this is perfectly normal and the haziness will disappear as the material reacts.
Conclusion
Every customer and project is different. While we can advise a customer as to which products are best suited to their needs, based on our years of experience, it all boils down to the unit, the dispensing method/equipment to be used, the curing times, and the temperature limitations that may be imposed during the production process. The more information that the customer can provide regarding the resin’s ultimate operating conditions—temperature range, likely chemical exposures, and so on—the better. See you next time for more resin-related tech tips. If you have any questions for us, please get in touch.
This column originally appeared in the September 2020 issue of Design007 Magazine.
More Columns from Sensible Design
Sensible Design: Automotive Conformal Coating ApplicationsSensible Design: Green Coats Are In
Sensible Design: Encapsulation Resins—PU vs. Epoxy
Sensible Design: Avoiding Conformal Coating Pitfalls
Sensible Design: Comparing Traditional and Bio-based Resins
Sensible Design: All Resins Are Not Created Equal
Sensible Design: Can Solvent-free UV-cure Coatings Increase Stability and Throughput?
Sensible Design: Optimize Your Thermal Management