-
- News
- Books
Featured Books
- design007 Magazine
Latest Issues
Current IssueShowing Some Constraint
A strong design constraint strategy carefully balances a wide range of electrical and manufacturing trade-offs. This month, we explore the key requirements, common challenges, and best practices behind building an effective constraint strategy.
All About That Route
Most designers favor manual routing, but today's interactive autorouters may be changing designers' minds by allowing users more direct control. In this issue, our expert contributors discuss a variety of manual and autorouting strategies.
Creating the Ideal Data Package
Why is it so difficult to create the ideal data package? Many of these simple errors can be alleviated by paying attention to detail—and knowing what issues to look out for. So, this month, our experts weigh in on the best practices for creating the ideal design data package for your design.
- Articles
- Columns
- Links
- Media kit
||| MENU - design007 Magazine
Cadence’s Clarity: 'I Can See Clearly Now'
December 3, 2020 | Clive "Max" Maxfield, Maxfield High-Tech ConsultingEstimated reading time: 11 minutes
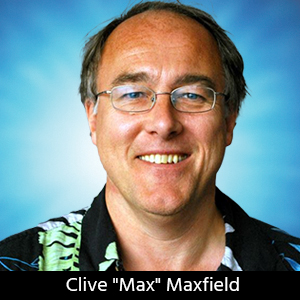
Do you recall the song “I Can See Clearly Now”? This catchy tune was first released by Johnny Nash in 1972, which was three years before I started my BSc in Control Engineering at Sheffield Hallam University, Yorkshire, England.
I’m humming the melody and thinking of the lyrics as I pen these words, except that I’ve just been looking at the Clarity 3D Transient Solver from Cadence, so the lyrics I’m hearing in my head are, “I can see clearly now the EMI is gone / I can see all EMC obstacles in my way / Here is that rainbow I've been praying for / It's gonna be a bright (bright) bright (bright) sunshiny day.”
The reason for my current mellowness is that, with extreme performance coupled with virtually unlimited capacity and scalability, the Clarity 3D Transient Solver opens the doors to previously unobtainable levels of system-level electromagnetic (EM) simulation for use in electromagnetic interference (EMI) and electromagnetic compatibility (EMC) analysis. When we use the word “system” in this context, we are talking about the ability to perform EM simulation at the chip, package, circuit board (including rigid boards, flex, and rigid flex), module, and multi-board/multi-module assemblies including connectors and cables. Phew!
EMI and EMC
Now, it’s easy to get confused here, so let’s briefly remind ourselves that EMI—which may also be referred to as radio-frequency interference (RFI) when in the radio frequency spectrum—is a disturbance generated by an external source that affects an electrical circuit by electromagnetic induction, electrostatic coupling, or conduction. Although sources of EMI can be environmental (e.g., electrical storms and solar radiation), they are more commonly caused by other electrical systems or electronic devices.
By comparison, EMC refers to the ability of electrical equipment and systems to function acceptably in their electromagnetic environment, whatever that may be. That is, the goal of EMC is the correct operation of different equipment in a common electromagnetic environment. This is achieved by limiting the unintentional generation, propagation, and reception of electromagnetic energy, which may result in EMI or even in physical damage if the EM source is of sufficient intensity.
The Way we Were
Just thinking of Clarity’s cornucopia of capabilities is causing me to have flashbacks to the way we used to do things in circa 1980 when I was starting my career. My first position was at International Computers Limited (ICL) as a member of a team designing central processing units (CPUs) for mainframe computers. And my first task was to design an ASIC, which was to be implemented at the 5-micron process node. My digital logic design was performed at the gate- and register-level of abstraction using pencil and paper.
Logic optimization was performed by another member of the team who was better at doing this that the rest of us. Functional validation was performed by all the members of the team looking at your schematics and asking pointed questions while you explained your logic and defended your decisions. Timing analysis was performed by you identifying any critical paths by eye and intuition, and then adding the gate delays and calculating the track delays by hand (no one I knew at that time could afford the state-of-the-art in 4-function electronic calculators).
I have no idea who performed the layout of the ASIC—that task was undertaken by another team—although I did hear that they also accomplished their tasks by hand. When the finished layout was presented to me, it was in the form of a ginormous ASCII text file, where ‘1’ characters indicated metal layer 1, ‘2’ characters indicated metal layer 2, ‘X’ characters indicated a via between metal layers 1 and 2, and so forth. Layout versus schematic (LVS) verification was performed by my printing this ASCII text file out in the form of around 20 strips each 20-feet long and 18-inches wide, using many rolls of sticky tape to form a gigantic rectangle in a large room that was reserved for this purpose, and then walking around (sans shoes) using colored crayons to mark off gates and tracks on my schematics and the corresponding transistors (silicon areas) and interconnect on the layout diagram.
One’s hope was to end up with everything in the schematic and layout colored appropriately; one’s fear was to discover discrepancies, or missing portions in the layout, or, as happened on occasion, to end up with unmarked areas in the layout that didn’t correspond to anything in the schematic, which resulted in some gnashing of teeth and rending of garb, let me tell you!
I also have no idea who designed the chip packaging including assigning pins to signals. Once LVS had been performed and everything had been signed off, with managers literally writing their monikers on the “ready for packaging” release, I didn’t hear or see anything until the packaged devices appeared several weeks later. Meanwhile, the PCB team had been performing their magic, which means someone must have told them what the pin assignments were going to be.
I didn’t become involved in PCB layout myself until a couple of years later when I was working for a small startup called Cirrus Designs. We had a mega-expensive system whose name I no longer remember, but it involved a large digitizing desk and mouse along with two large (for the time) monitors: one black-and-white where you issued command-line text-based instructions like “Place a pad at X=xxx and Y=yyy” and the other in color where you saw the results. The whole thing was powered by a fridge-sized computer. It was horrible. The best thing that happened to this system was when it overheated and caught fire, but that’s a story for another day!
When it came to things like EMI and EMC, as far as I know there were no simulation and analysis tools up to the task (we were more than happy if our deskside computers were powerful enough to run a screen editor). Apart from simply “winging it,” the only option available to us in those days was to build a physical prototype of the full system, send it out to a specialist company that had an anechoic chamber (also known as an EMC chamber) for EMI and EMC testing, and await the results in dread anticipation. In addition to costing lots of money, this could take weeks before we saw any results. If anything failed, and something almost invariably did, it was back to the drawing board. Thinking back, it’s amazing we actually managed to get any products out of the door.
Confiscating Chaos and Confusion
As radio commentator, motivational speaker, and author Steve Maraboli famously said in his book Life, The Truth, and Being Free, “It’s a lack of clarity that creates chaos and frustration.” Even though this book was published 11 years ago at the time of this writing, it’s as though Steve was peering into the future and channeling how Cadence’s Clarity 3D Transient Solver can confiscate chaos, confusion, and frustration, thereby making developer’s lives happier, easier, and more productive.
Cadence has state-of-the-art design and analysis tools for every portion of the design flow—chip design, package design, and board/module design. What is less well known is that, for the past few years, Cadence has been ramping up its capabilities in system-level simulation, analysis, and verification space (where no one can hear you scream) with tools like the Clarity 3D Transient Solver. In addition to performing EM simulation for EMI and EMC analysis and verification on chips, packages, and boards, the Clarity 3D Transient Solver means that it’s now possible to perform such simulations on full systems comprising multiple boards/modules, connectors, cables, and enclosures.
Let’s take a step back and think about this a bit. As we previously discussed, the traditional way of performing EMI/EMC verification involves building a physical prototype of the system and testing it in an anechoic chamber. It comes as no surprise to learn that it is horrendously expensive in terms of development time, resources, money, and time-to-market to build physical prototypes, test them, find problems, attempt to fix those problems, and then perform the whole cycle over and over again. It’s obviously a much better solution to perform EM simulation to detect, identify, and resolve problems early in the design cycle, only building a physical prototype and performing real-world testing a single time at the end of the development process. The problem, of course, is finding an EM simulator that has the capacity and performance to simulate the full system, otherwise you have to partition things into smaller and smaller pieces, in which case you know only how these pieces work in isolation.
Page 1 of 2
Suggested Items
Digital Twin Concept in Copper Electroplating Process Performance
07/11/2025 | Aga Franczak, Robrecht Belis, Elsyca N.V.PCB manufacturing involves transforming a design into a physical board while meeting specific requirements. Understanding these design specifications is crucial, as they directly impact the PCB's fabrication process, performance, and yield rate. One key design specification is copper thieving—the addition of “dummy” pads across the surface that are plated along with the features designed on the outer layers. The purpose of the process is to provide a uniform distribution of copper across the outer layers to make the plating current density and plating in the holes more uniform.
Meet the Author Podcast: Martyn Gaudion Unpacks the Secrets of High-Speed PCB Design
07/10/2025 | I-Connect007In this special Meet the Author episode of the On the Line with… podcast, Nolan Johnson sits down with Martyn Gaudion, signal integrity expert, managing director of Polar Instruments, and three-time author in I-Connect007’s popular The Printed Circuit Designer’s Guide to... series.
Showing Some Constraint: Design007 Magazine July 2025
07/10/2025 | I-Connect007 Editorial TeamA robust design constraint strategy balances dozens of electrical and manufacturing trade-offs. This month, we focus on design constraints—the requirements, challenges, and best practices for setting up the right constraint strategy.
Elementary, Mr. Watson: Rein in Your Design Constraints
07/10/2025 | John Watson -- Column: Elementary, Mr. WatsonI remember the long hours spent at the light table, carefully laying down black tape to shape each trace, cutting and aligning pads with surgical precision on sheets of Mylar. I often went home with nicks on my fingers from the X-Acto knives and bits of tape all over me. It was as much an art form as it was an engineering task—tactile and methodical, requiring the patience of a sculptor. A lot has changed in PCB design over the years.
TTCI Joins Printed Circuit Engineering Association to Strengthen Design-to-Test Collaboration and Workforce Development
07/09/2025 | The Test Connection Inc.The Test Connection Inc. (TTCI), a leading provider of electronic test and manufacturing solutions, is proud to announce its membership in the Printed Circuit Engineering Association (PCEA), further expanding the company’s efforts to support cross-functional collaboration, industry standards, and technical education in the printed circuit design and manufacturing community.