-
- News
- Books
Featured Books
- design007 Magazine
Latest Issues
Current IssueProper Floor Planning
Floor planning decisions can make or break performance, manufacturability, and timelines. This month’s contributors weigh in with their best practices for proper floor planning and specific strategies to get it right.
Showing Some Constraint
A strong design constraint strategy carefully balances a wide range of electrical and manufacturing trade-offs. This month, we explore the key requirements, common challenges, and best practices behind building an effective constraint strategy.
All About That Route
Most designers favor manual routing, but today's interactive autorouters may be changing designers' minds by allowing users more direct control. In this issue, our expert contributors discuss a variety of manual and autorouting strategies.
- Articles
- Columns
- Links
- Media kit
||| MENU - design007 Magazine
Estimated reading time: 10 minutes
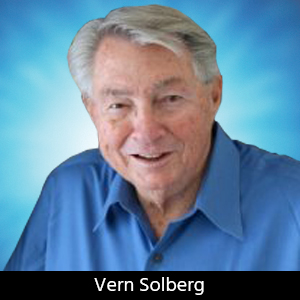
Designers Notebook: Embedding Resistor Elements—Part 2
The decision to embed passive components within the PCB structure is commonly prompted by two key barriers: restricted surface area and interconnect complexity. The PCB’s functionality may also require a significant number of semiconductor packages, often requiring very close coupling to meet their target performance potential. Regarding surface area challenges, many companies are confronted with the need to reduce end-product size to maintain a competitive edge in a particular market, or to satisfy the anticipated needs of their customer base.
Over 70% of the components occupying space on a typical printed circuit board are passive (resistors, capacitors, inductors). Although most passive components are minimal in size, they can occupy up to 50% of the board’s surface area. Transferring most of the resistor elements onto the subsurface layers of the PCB will enable the designer the opportunity to optimize semiconductor placement, reduce circuit board size (typical of that illustrated in Figure 1), and ultimately achieve the most efficient interconnect between principal functions.
As an alternative to the thick-film resistor process detailed in Part 1 of this topic, a significant number of PCB fabricators are offering embedded thin-film resistor capability. In comparing the thick-film resistor forming process, photo-lithography has replaced the printing and dispensing of paste-like resist materials to define the embedded resistors’ geometry. Many circuit board fabricators prefer the coated copper foil technology because the composite material’s base value range is more precise than the deposited thick-film alternative, ensuring that the value and tolerance of the formed resistor element is more likely to meet customer expectation.
Base Materials for Thin-Film Resistor Forming
To begin, a resistive alloy coating is deposited onto copper foil to create the base material for embedded resistor applications. The resistive alloy is electrodeposited or deposited onto the copper foil using a roll-to-roll sputtering process. Resistive alloy thickness determines the overall resistance value (ohms/sq.) of the coated copper foil. Alloys commonly applied for embedded resistor applications include nickel phosphorous (NiP), chromium silicon monoxide (CrSiO), nickel chromium aluminum silicon (NCAS), and nickel chromium (NiCr). The sheet resistance of nickel-chrome alloy film containing 20% chromium, as an example, will furnish the designer with a resistance range as high as 3 K-ohms.
Resistor Element Planning
Typical of the discrete resistor element, the formed resistor will span the area between two copper lands. The shape of the resistance material between the copper lands can be a simple square, a series of squares to form a rectangle, or a shape designed to maximize resistor element length while minimizing area.
Initial planning:
- Identify resistors for embedding.
- Establish R-value and target tolerance.
- Determine power rating requirement.
- Define finished element geometry.
- Select location (layer) and orientation.
The power dissipation is the rate at which resist energy is lost in elements. The power capability for embedded resistors will depend on the physical size of the resistor elements, temperature rating of the surrounding substrate materials, and the board stack-up. In the end it boils down to how the heat generated is managed. Typical power dissipation for most thin-film resistor designs operating at an ambient of less than 70°C is approximately 1/10 to 1/8 watt.
Typical of the thick-film composites, the base values of the thin-film resist-coated copper foil sheet materials are based on a single square geometry. While terminating resistor values are predominantly 50 ohms, and pull-up resistors fall in a range between 1K ohm and 10K ohm, these base values can be extended to furnish significantly higher resistor elements.
Implementation:
- Establish land pattern (termination) geometry.
- Define overall element dimensions.
- Select optimum element position.
- Plan most efficient circuit interface.
- Provide features for test probe access.
As noted, the “square” geometry represents the basic ohm value of the resistive material. The designer can increase the resistance value by simply extending the length of the resistor pattern with additional squares or partial square segments (Figure 2).
The resist-coated copper foil will become an integral part of the multilayer circuit board construction that, when processed, will furnish both formed resistor elements and provide general interconnect functions. The formed NiP resistor element examples (Figure 3) represent a subsurface interconnect layer prepared for lamination within a multilayer PCB.
After chemically removing copper and defining the resistor image, the now exposed nickel-phosphorous resistive material exhibits a matte grey finish.
To enable efficient utilization of the primary base value of the coated foils, the element geometry can be extended further in length to provide a broad range of resistor values. When the resistor element length becomes too long, however, it can restrict or block efficient circuit routing paths. To compress the surface area required for the more complex resistor elements, it is common practice to compress the physical area using a “serpentine” configuration typical of that exhibited in Figure 4.
The design rules for the serpentine-configured resistor pattern are significantly different than the straight bar configuration detailed above. When developing the resistor element in a serpentine configuration the designer must adjust the basic value at each corner of the serpentine pattern. The square geometry located at each corner transition will furnish a value that is only one-half the resist material’s base value. The 19-square resistor pattern illustrated in Figure 5 represents a 15K-ohm resistor utilizing 1K-ohm base value material.
Regarding individual resistor tolerance control, thin-film material suppliers note that most circuit board fabricators will anticipate a resistor tolerance at or less than 20%. The resulting tolerance will be dependent on the precision of the image and etch process. Precise etch control will repeatedly produce resistors with a tolerance range encompassed by what the fabricator can maintain on controlled impedance lines and the published sheet tolerance. Variation of the tolerance can be minimized by maintaining a uniform element width (> 200-micron) for the resistor patterns and fine-tuning the resistor element length to achieve the required target resistor value. But the designer must keep in mind that over specifying resistor tolerance will likely impact processing costs.
Sourcing Thin-Film Resistive Materials
Resist coating can be furnished on any copper foil thickness, but thicknesses of 12 µm, 18 µm (0.5 oz) and 35 µm (1 oz) are likely to be more available because they are commonly selected for a wide range of multilayer organic circuit board applications. The two leading suppliers of the copper foils furnished with the resistive coatings in North America are Ohmega Technologies LLC. and Ticer Technologies.[1]
Materials provided for resistor formation from Ohmega Technologies are described as a subtractive technology where the base material preparation begins with a thin-film resist-coated copper foil laminated onto a glass-reinforced dielectric. In preparation, the company first electrodeposits a thin coating of nickel phosphorous (NiP) alloy onto the copper foil’s matte or tooth side. Base resist values of the Ohmega coated copper foils range from 10 ?/sq to 377 ?/sq (Table 1).
The power dissipation is the rate at which resist energy is lost in elements. The power capability for embedded resistors will depend on the physical size of the resistor elements, temperature rating of the surrounding substrate materials, and the board stack-up. In the end it boils down to how the heat generated is managed. Typical power dissipation for most thin-film resistor designs operating at an ambient of less than 70 °C is approximately 1/10 to 1/8 watt.
Coated foil materials can be furnished as a foil only product or pre-laminated to a variety of standard FR-4, polyimide, or more specialized microwave substrate materials. The pre-laminated material can be furnished directly from Ohmega Technologies as well as other sources, including Arlon, Rogers, and Taconic. The company also offers a NiP material with a sheet resistivity of 377 ohms per square, which was developed for a range of specialized applications that include high impedance and frequency selective surfaces, antenna arrays, or as radar absorbing materials for resistive cards.
Three variations of resistive-coated thin-film on copper foils are available from Ticer Technologies that provide a specific range of resist coatings: nickel-chromium (NiCr), nickel chromium-aluminum-silicon (NCAS) and chromium-silicon-monoxide (CrSiO). Individually, these alloy compositions can furnish a broad range of base resist values from 25 ohms to 1K ohms. Table 2 details the sheet resistance value range, tolerance and the maximum power dissipation factor for the three resistance alloy compositions noted.
Ticer Technologies resistive-coated copper foil material is furnished in sheet form or as a product pre-laminated onto standard ROHS-compliant FR-4 glass-reinforced resin material or any number of reinforced specialty resins from a vast network of global material suppliers.
Resistor Process Sequence
The resistor forming process will include two or three etch steps, depending on the resistor alloy selected. The process flow illustrated in Figure 6 from Ticer Technologies represents a two-stage chemical etching sequence for their nickel chromium (NiCr) resistive material.
With respect to circuit layer preparation, fabricators are able to image and chemically etch the circuit layers using standard subtractive PCB processing. As far as chemistry, the printed circuit board industry commonly employs cupric chloride etchants for the primary circuit image and resistive layer width definition. A second etch step is required to selectively remove copper to define the length of the resistor elements. This process requires a different chemistry to ensure only copper removal without altering or degrading the remaining resistive element geometry.
Power Dissipation
As far as handling power, the manufacturers state that power density is defined as the total power dissipated divided by the effective surface area. The power density of the resistor element increases as the area decreases. All other conditions illustrate that for the same power input, the temperature rise will depend on the area of the resistor. In other words, the resistors with a larger surface area can dissipate more power than a narrow geometry, provided that all conditions remain the same. If space is available, design the resistor element to be as wide as possible. Additionally, when the resistors are buried within the layers of the circuit board, the physical and thermal characteristics of the substrate material (the total thickness of the substrate and the collective number of copper layers) will directly affect heat dissipation from the fully assembled circuit board.
Omega Technologies notes that electrical current should not exceed the rated current-carrying capacity of the resistor because excessive current could cause permanent damage to the formed resistor element.[2]
In-Process Testing
Prior to further circuit layer lamination, the resistor elements’ value and tolerance must be validated. The “flying probe” test is widely used to validate the embedded resistor elements’ target value before lamination of additional circuit layers. Most flying probe testers can also perform signal integrity testing as well as identify the location of opens and shorts. To enable test probe access, dedicated land features must be provided for each formed resistor element. Lands provided for test probe access must not be arranged in a way that would require probes to cross over or contact other probes. When laser trimming is required to fine-tune a resistor element, the probe contact must not interfere with laser access while making a trim. For best test and trim accuracies, the test lands should be near to the resistor-to-circuit termination point to ensure precise resistor value measurement.
When developing land geometry for test-probe access, probe tip shape and dimensions will determine the minimum land size. Test system manufacturers state that probes have a placement tolerance of 50 ?m (0.002”) in each of the X, Y, and Z axes. The land pattern diameter must be greater than the probe tip to accommodate probe positional tolerances and allow for uniform probe pressure and pad scrub. First-time users should refer to their circuit board supplier to determine the suitability of their test equipment and availability of the required software for testing the embedded resistor elements.
Design Tools
Most software developers are currently furnishing the necessary tools to implement the embedded resistor elements within the multilayer circuit board. Material suppliers suggest that the CAD designer consider using Mentor, Allegro, Intergraph, and PAD Power PCB in conjunction with an Excel program to aid in developing the more complex resistor element geometries. While several resistor elements will likely remain on the outer surface of the finished circuit board, the embedded resistors will require a unique reference designator to avoid procurement errors. For example, a surface-mounted resistor will be defined as R110 while the embedded or buried resistor will be labeled BR110 on the schematic diagram and material list.
Implementation Issues and Concerns
Formed passive resistor element values and tolerance that range between 5–10% will likely meet the operational criteria of the final product but altering the value after lamination will not be an option. Due to the physical stresses experienced during PCB lamination and assembly processing, target values of resistors may drift outside the specified resistance target, and laser trimming will not be practical. When the specified values of the resistor elements require tolerance in the 1-2% range, I strongly advise the circuit board designer to retain these higher precision resistors as discrete surface mount components for placement onto the circuit board’s outer surface(s).
References
- Ohmega Technologies has been acquired by Quantic Electronics, a business unit of Arcline Investments which focuses on specialty component materials. More recently, Quantic also acquired Ticer Technologies. The company stated that it plans to maintain multi-plant resistive foil operations for both OhmegaPly and Ticer TCR materials.
- For more information refer to the Power Dissipation Guidelines contained within the Resistor Calculators on both Ticer’s and Ohmega’s websites.
This column originally appeared in the June 2021 issue of Design007 Magazine.
More Columns from Designer's Notebook
Designers Notebook: Basic PCB Planning Criteria—Establishing Design ConstraintsDesigners Notebook: Layer Stackup Planning for RF Circuit Boards
Designers Notebook: Addressing Future Challenges for Designers
Designers Notebook: Impact of Advanced Semiconductor Packaging on PCB Stackup
Designers Notebook: Implementing HDI and UHDI Circuit Board Technology
Designer's Notebook: Heterogeneous Integration and High-density SiP Technologies
Designers Notebook: PCB Design and IPC-CFX for Assembly Automation
Designer’s Notebook: What Designers Need to Know About Manufacturing, Part 2