-
- News
- Books
Featured Books
- design007 Magazine
Latest Issues
Current IssueAll About That Route
Most designers favor manual routing, but today's interactive autorouters may be changing designers' minds by allowing users more direct control. In this issue, our expert contributors discuss a variety of manual and autorouting strategies.
Creating the Ideal Data Package
Why is it so difficult to create the ideal data package? Many of these simple errors can be alleviated by paying attention to detail—and knowing what issues to look out for. So, this month, our experts weigh in on the best practices for creating the ideal design data package for your design.
Designing Through the Noise
Our experts discuss the constantly evolving world of RF design, including the many tradeoffs, material considerations, and design tips and techniques that designers and design engineers need to know to succeed in this high-frequency realm.
- Articles
- Columns
Search Console
- Links
- Media kit
||| MENU - design007 Magazine
Estimated reading time: 7 minutes
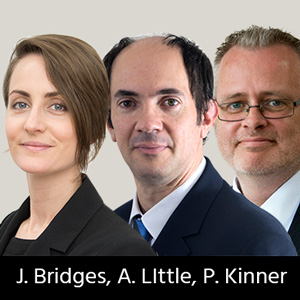
Sensible Design: Let’s Take Down the Heat on Resins
This month, I continue my series on how resins are currently playing a vital role in the modern world, while also offering an insight into their thermal conductivity, suitability for RF applications, and exploring a new era of bio-based encapsulation resins that not only improve the environment at large, but also end-use reliability and increased consumer satisfaction.
1. Thermally conductive encapsulation resins: Why would you use one of these over a conventional thermal paste or TIM?
Thermal pastes are often applied between heat-generating components and heat sinks to maximise heat transfer, improve device reliability, and extend lifetime. This is due to their high thermal conductivity values and, when applied as a thin bond line, they exhibit low thermal resistance. By applying a thin, uniform layer of a thermal interface material, it is possible to obtain the maximum efficiency of heat dissipation. It is also important to consider the operating temperature conditions; in the case of LEDs where devices are switched on and off regularly, this results in the unit going through a thermal cycle, heating up once switched on and cooling again when powered down. Over the lifetime of the product, many thermal cycles take place, and this may affect the positioning of a thermal paste over time. In other words, a poorly formulated paste can migrate over time and reduce the efficiency.
Thermally conductive resins can be used as an alternative solution to “keep things cool.” Such resins also provide lots of other value-added benefits such as mechanical protection. If protecting components from mechanical shock and vibration are a concern, then a thermally conductive encapsulation resin is likely to be the best solution as it adds a level of stability that helps to insulate the potted components against adverse mechanical movements. The arch enemy of electrical and electronic devices is the dreaded “moisture”; besides producing short-circuits moisture also causes corrosion, which leads to premature deterioration of components. You might also need to protect electrical or electronic components from encountering chemicals, including acids, alkalis, solvents, and other substances that pose a threat to delicate circuits and components. Encapsulating with a thermally conductive resin will help to ruggedize against all these harsh external factors. Lastly, it’s worth citing that, aside from providing all the protections listed above, opaque potting and encapsulation resins also conceal what lies beneath. This could provide an effective foil against counterfeiters or those wishing to copy a circuit layout, helping you to protect your intellectual property.
2. Which chemistry (if any) lends itself to thermal conductivity, i.e., epoxy, polyurethane, or silicone?
Epoxy, polyurethane, and silicone chemistries are all capable of producing resins with high thermal conductivity values. The thermal conductivity is dictated by the type of filler used, particle size, particle size distribution, and morphology. When these four factors are carefully considered as part of the product design, you get encapsulation resins with high thermal conductivity values, irrespective of the reactive chemistry that hold the filler in place.
One of our products provides the highest level of thermal conductivity combined with environmental protection afforded from the encapsulation process. This highly-filled epoxy resin possesses very high thermal conductivity, 1.54 W/m.K. Thermal conductivity, measured in W/m.K, represents a material’s ability to conduct heat. Bulk thermal conductivity values give a good indication of the level of heat transfer expected, allowing for comparison between different materials. We utilise a modified transient plane source (MTPS) method, amongst others, to provide accurate comparisons of bulk thermal conductivity. Note there are different methods to determine thermal conductivity so remember that when comparing datasheets from different suppliers.
3. Apart from the obvious assumed benefit to the environment, what other benefits could be expected from bio-based resins and are there more to come?
There are many observed benefits to using bio-based resins aside from the obvious environmental credentials. Research has shown that quality of performance can be significantly improved. Resins where the reactive component is derived from biobased feedstocks can have improved performance in harsh environments, particularly their electrical insulation in hot, humid conditions, as compared to reactive components derived from crude oil. Comparing biogenic powders with mineral rock powders shows that bio-sources can be used to effectively dissipate heat away from high power density devices and they show improved protection in underwater environments.
There can also be health and safety benefits. For example, the curing agent or hardener typically used for polyurethanes is based on methylene diphenyl diisocyanate (MDI); crude oil is a crucial raw material for the synthesis of MDI. It is a respiratory sensitiser and harmful if vapours are inhaled, from a H&S label perspective it contains the “exploding chest” pictogram (GHS08/health hazard). We can replace this hardener with alternative reactive agents derived from bio-sources which do not contain the GHS08 pictogram and are much safer for operators to use.
4. Do bio-resins lend themselves to RF applications?
They most certainly do. We have another with bio-sourced content of over 60%, which is an unfilled polyurethane resin that has found success in sensor applications as it has a low dielectric constant (relative permittivity). Most IoT communication takes place in blocks of the radio frequency spectrum; a low dielectric constant is essential to ensure the resin does not interfere with the RF signal. It provides excellent electrical insulation across a wide operating temperature range, which is required for long-term performance, and has a high toughness, offering protection from physical shock and vibration. It has good resistance to lots of deleterious substances, making it the ideal choice for ruggedizing sensors exposed to harsh environments.
5. What sort of testing programmes have these new bio-resins been subjected to?
The bio-resins have been tested extensively. There is a common perception that going green, or bio-based, means there will be some sort of compromise on quality of performance. For a new product line to be relatively disruptive and have a high bio-derived content, extreme testing was essential to generate valuable data. The barriers to entry for encapsulation resins in the electronics market is relatively low when compared with other ruggedization techniques such as conformal coatings. Typically, a lot of resin qualification comes down to customers screening for their own unique application; the resin either passes or fails. There is no formal industry standard that outlines a specific test criterion; this is mainly because every application is truly unique.
To recall just a handful of the tests these new bio-resins have been subject to:
- Surface insulation resistance testing (SIR) on copper and tin B-24 test coupons at 85°C/85% RH, to ensure the encapsulant remains electrically insulative in hot humid conditions
- Volume resistivity before and after immersion in water and salt water to ensure the bulk material remains electrically insulative in underwater applications
- Thermal shock testing at -40°C to +85°C for plastic housing and -40°C to +125°C for galvanised steel housing, to monitor for any cracks or loss of adhesion in this accelerated life test
- 1,000-hour thermal ageing was performed on type IV specimens in accordance with ASTM D638
- The tensile strength and elongation were measured before and after high temperature exposure for 100, 500, and 1000 hours to monitor the consistency in physical performance with long term exposure to high temperatures, to determine the maximum operating temperature
Numerous accelerated life tests have been performed to evaluate the performance of novel bio-based materials alongside commercially available resins derived from crude oil and mineral rock powders. Comparison of data concludes that “going green” can deliver performance advantages in underwater applications as well as hot and humid operating environments.
Resins play an integral part in ensuring that an electronics product can survive for at least its design life, and often well beyond. Be it chemical, physical, or thermal, whatever the conditions, there is a resin system that can be found or developed to provide the protection required. I hope you have enjoyed learning more about the benefits of bio-based resins and what they can bring to your applications. Over the coming months I hope to provide more useful tips and design advice that will help make life a bit easier for those who are responsible for making the decisions on protecting components and circuitry. Watch for my next column, where I will be exploring resin systems in more detail.
This column originally appeared in the April 2022 issue of Design007 Magazine.
Download your free copy of?Electrolube's?book,?The Printed Circuit Assembler's Guide to… Conformal Coatings for Harsh Environments,?and watch the micro webinar series “Coatings Uncoated!”?
More Columns from Sensible Design
Sensible Design: Automotive Conformal Coating ApplicationsSensible Design: Green Coats Are In
Sensible Design: Encapsulation Resins—PU vs. Epoxy
Sensible Design: Avoiding Conformal Coating Pitfalls
Sensible Design: Comparing Traditional and Bio-based Resins
Sensible Design: All Resins Are Not Created Equal
Sensible Design: Can Solvent-free UV-cure Coatings Increase Stability and Throughput?
Sensible Design: Optimize Your Thermal Management