-
- News
- Books
Featured Books
- smt007 Magazine
Latest Issues
Current IssueSupply Chain Strategies
A successful brand is built on strong customer relationships—anchored by a well-orchestrated supply chain at its core. This month, we look at how managing your supply chain directly influences customer perception.
What's Your Sweet Spot?
Are you in a niche that’s growing or shrinking? Is it time to reassess and refocus? We spotlight companies thriving by redefining or reinforcing their niche. What are their insights?
Moving Forward With Confidence
In this issue, we focus on sales and quoting, workforce training, new IPC leadership in the U.S. and Canada, the effects of tariffs, CFX standards, and much more—all designed to provide perspective as you move through the cloud bank of today's shifting economic market.
- Articles
- Columns
- Links
- Media kit
||| MENU - smt007 Magazine
Estimated reading time: 4 minutes
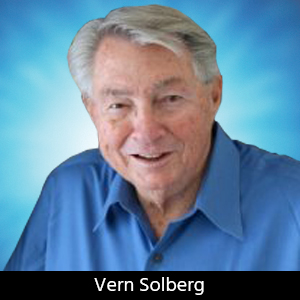
Designers Notebook: Flexible Circuits for In-line SMT Assembly Processing
Incorporating surface mount components directly onto a flexible circuit’s etched copper land patterns is not unlike the assembly process used for rigid circuit boards. To maximize robotic assembly efficiency and increase throughput of the flexible circuit, however, the circuit design engineer will need to provide a format that includes all features required for in-line assembly processing. There are three primary process stages for surface mount assembly: solder paste deposition, component placement, and reflow-solder processing. To maximize manufacturing efficiency, automated systems developed for performing these functions are each designed to accommodate the in-line conveyor transfer between one system to another (Figure 1).
Conveyor systems, although adjustable, rely on at least two parallel edges to support and transport the circuit from one machine to another. While rigid circuit boards are easily configured for conveyor processing, handling flexible material in a production environment will require a provision for the support of the thin, film-based circuit throughout each stage of the assembly process. For the low- and medium-assembly volume applications, a conveyor-compliant pallet fixture can be prepared to retain the individual flexible circuits during each stage of the assembly; however, products requiring high-volume assembly processing require a more efficient solution.
To better accommodate conveyor handling, flexible circuits can be furnished from the circuit fabricator with a temporary, rigid carrier panel backing. Figure 2 exhibits a single flexible circuit assembly with a rather complex outline. Without the benefit of the rigid backing material and a dedicated, product-defined carrier pallet fixture, precise solder paste deposition and accurate component placement would not be possible.
Fabrication companies have developed a broad range of solutions for panel layout to both encourage efficient handling and support large and small form factor circuits through the assembly process:
- Single unit format (medium and large circuits)
- Multiple unit array format (row and column layout)
- Nested array format (maximizing area utilization)
When processing the smaller form factor flexible circuits, the multiple unit array format has proved both efficient and economical.
Palletizing the Flexible Circuit
The carrier panel developed for flexible circuit applications is designed to provide the uniform, rigid-board outline needed for conveyor transfer and to physically support the flexible circuit through each assembly process sequence. To keep the single- and multiple-unit flexible circuits in place, the designer will need to provide small tab-like connecting features. To provide an area for the adhesion of the flexible material to the carrier panel, the flexible base material is simply extended outward to match the carrier panel outline. The adhesive film joining the flexible material to the rigid carrier panel must remain clear of the flexible circuit outline.
The palletized, multi-unit example shown in Figure 3 represents a grouping designed to maximize material utilization for small, irregularly shaped flexible circuit units. This example represents flexible circuit units that are arranged in the opposing orientation or “nested” array format.
Key Features Required for Automated Assembly
The supporting panel must include several key attributes:
- Edge clearance of the carrier panel must allow for unobstructed access to the conveyor support belt.
- Two or more tooling holes are required, located outside the flexible circuit units to secure the panel during the post assembly separation procedure.
- An equal number of “global fiducial targets” need to be located near the panel edge area to assist panel alignment during the solder deposition process. Solder deposition systems use cameras to pinpoint the fiducial targets, enabling precise alignment of the solder stencil to the land pattern features on the individual circuit units within the panel’s central area.
In addition to the globally located fiducial features, two or more fiducials will be required within the component mounting zone to facilitate precise automated component placement. Using multiple fiducial datum features within the SMT component placement area will minimize the effects of variable shrinkage or any process distortion in the flexible materials.
The illustration in Figure 4 is an example of a flexible circuit with SMT components mounted within two zones that are separated by a narrow interconnect section. Multiple fiducial locations will provide a tighter tolerance within each datum zone or termination area while relaxing the need to maintain a constricted tolerance of the flexible interface section between other component termination areas.
Fiducial Target Design Specification
The optimum fiducial target is simply a solid fetched copper circle that is clear of surface coating or cover layer material. Coatings and cover layer film material openings surrounding the fiducial must be adjusted to provide enough clearance around the fiducial’s perimeter to ensure that it does not overlap onto the fiducial target features during the cover layer-to-base circuit lamination process.
- The optimum fiducial is a solid circular land pattern that is 0.25 to 0.50 mm (~0.010" to 0.020") in diameter.
- To enable visual access for locating the fiducial targets, the solder mask or cover coat must provide a clearance 2 x R of fiducial R.
- Fiducial location must be clear of the panel or circuit outline edge by a minimum of 4.75 mm (~0.187") and provide a consistent high contrast.
No plating is required on the etched copper fiducial surface, but if a secondary alloy plating over the base copper is specified in the control document, the designer must ensure that flatness of the fiducial surface is maintained within 0.015 mm (0.006").
Final Comments
When planning multiple unit circuits for panel processing, the flexible circuit designer should attempt to coordinate the final panel size and unit configuration between both those responsible for the assembly process and the fabricator designated for manufacturing the circuit.
Technical Course
Vern Solberg will be presenting a half-day technical course, “Flexible and Rigid-flex Circuit Design for Manufacturing,” on Sunday, Jan. 22, at IPC APEX EXPO 2023. The course will focus on SMT design, fabrication, and assembly process principles.
This column originally appeared in the December 2022 issue of Design007 Magazine.
More Columns from Designer's Notebook
Designers Notebook: Basic PCB Planning Criteria—Establishing Design ConstraintsDesigners Notebook: Layer Stackup Planning for RF Circuit Boards
Designers Notebook: Addressing Future Challenges for Designers
Designers Notebook: Impact of Advanced Semiconductor Packaging on PCB Stackup
Designers Notebook: Implementing HDI and UHDI Circuit Board Technology
Designer's Notebook: Heterogeneous Integration and High-density SiP Technologies
Designers Notebook: PCB Design and IPC-CFX for Assembly Automation
Designer’s Notebook: What Designers Need to Know About Manufacturing, Part 2