Estimated reading time: 6 minutes
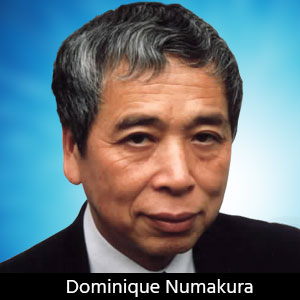
EPTE Newsletter from Japan - Just In Time (JIT) Strategy Feels Earthquake Tremors
Topics of the Week
Just In Time (JIT) Strategy Feels Earthquake Tremors
An earthquake with a magnitude of 6.8 struck the west coast of Japan on July 16, 2007, killing more than ten people. The epicenter of the earthquake was located near the city of Niigata, and delivered serious damage to many buildings. Utilities that include gas, water and electricity had service interrupted, and many people are still without power. Media outlets reported the nuclear power stations in the area suffered serious damages and radio active wastes were discovered. The Japanese government directed the electric power supply company to cease all operations from 8 nuclear reactors in the area. When the nuclear facilities were built, the electric company guaranteed its reliability and safety to withstand the strongest earthquake; however, they now have no idea when the plant can resume operation from its nuclear reactors. The shortage of power during the hottest summer in Japan is on everyone's mind.
RIKEN Corp., an automobile parts manufacturer in the area also suffered serious damages within its facilities prompting a brief production stoppage. Since RIKEN holds a very high market share within the piston ring industry, Japanese automobile manufacturers also shut down operations. Questions are being asked about the JIT (Just in Time) systems introduced to Japanese car manufacturers as a way to decrease manufacturing costs. When Japanese auto makers adopted this management concept, their vendors were expected to deliver the exact amount of parts and materials used in manufacturing process on time and eliminate surplus inventory. Automobile companies no longer needed large warehouses to inventory major parts and materials. Unfortunately, there was no surplus inventory of piston rings (a key part of an engine), and no alternative supplier to RIKEN. Some rings that were in transit or in the pipeline before the earthquake struck was exhausted within a few days. This hobbled car manufacturers causing production to halt. As long as the planets stay aligned, and no wrench is thrown into its gears, the JIT system is an efficient concept; however, as several business analysts pointed out, the unpredictable - earthquakes, typhoons, or other natural disasters, are the unknown variables that weaken or cause calamity to the "Just In Time" system.
Industry analysts did not give too much credit to the resilient Japanese auto manufacturers. Leading automobile companies including Toyota Motors and Honda Motors deployed rescue teams to the RIKEN plant that included several hundred engineers and technicians along with the necessary machines and tools to fix the building and damaged manufacturing equipment. The rescue teams seemed to work more effectively than the government troops. Their tasks completed very quickly, RIKEN resumed production within a week, and reached full operation within two weeks, despite the fact RIKEN management had no idea how to patch up the plant that was destroyed by an earthquake days earlier.
Once the dust settled, automobile industry spokespersons released nearly identical communications re-stating their support for the JIT system as a very reliable and cost effective concept. They further added there are no plans to increase production part inventories or increase vendor counts in anticipation of future natural disasters; however, consideration will be placed on optimizing quicker recovery systems. The JIT system is a technique that has contributed to the success of Japanese automobile manufacturers to emerge as a global leader in the industry.
There are many books published in the U.S. explaining the JIT systems and the Kanban systems. Many American companies tried to adopt the systems; however, reports indicate the management style did not work very well in the U.S. or in Europe. One could argue the textbooks introduce only basic ideas about the manufacturing systems, and it is not easy to understand its real values or how to evolve as an organization using this system. I hope the quick actions of the automobile companies during the earthquake disaster give you some insight to better understand the JIT system.
Dominique Numakura, DKN Research (dnumakura@dknresearch.com)
Headlines of the week
(Please contact haverhill@dknreseach.comfor further information of the news.)
1. Panasonic (Major electronics company in Japan) 8/7
Has started the manufacturing operation of the new plant in China for the assembling of semiconductors.
2. SMK (Major connector manufacture in Japan) 8/8
Has commercialized a new 0.5 mm pitch connector series "EF-51" for the termination of high density flexible circuit. They have a higher reliability.
3. Hitachi Chemical (Major electronics material supplier in Japan) 8/9
Will start the volume production of film base optical guide material. The material can generate 20 micron lines by a photolithography process on circuit boards.
4. Sanyo Semiconductor (Major component supplier in Japan) 8/14
Has developed a new EEPROM device with wafer level packages.
5. Nippon Electric Glass (Major glass material supplier in Japan) 8/14
Will invest 35 billion yens to increase the manufacturing capacity of glass substrates of LCD panels 10% in Shiga Plant.
6. Nissha (Photo and printing product supplier in Japan) 8/15
Will invest 7.8 billion yens for the new plant in Ishikawa Prefecture for the volume production of touch panel switches.
7. Showa Denko (Major chemical company in Japan) 8/14
Has started the volume production of new 3.5" aluminum base discs with 334 GB capacity in June.
8. Nippon Gohsei (Major material company in Japan) 8/16
Will invest 3.5 billion yens for the new manufacturing line of OPL films. The total capacity will be 55 million square meters per year.
9. Chisso (Major chemical company in Japan) 8/20
Has developed a new polyimide base insulation ink for the ink jet printing process.
10. Sangyo Times (Major industrial media in Japan) 8/21
Has published the new directory of the solar sells and relating products companies. The new directory also covers the technical trend of the industry. 18,900 yens.
11. SMK (Major connector manufacture in Japan) 8/22
Has rolled out a new 16 pin 0.8 mm pitch interface connector with low profile. (2.0 mm height)
12. Sharp (Major electronics company in Japan) 8/23
Will build a new plant of solar cells in Sakai, Osaka. The operation will be started in 2010 with 1000 MW manufacturing capacity.
13. Pulsmo (Assembling company in Japan) 8/23
Will build a new assembling plant of printed circuits in Iida-shi, Nagano for amusement applications.
14. Nitto Denko (Major electronic material supplier in Japan) 8/22
Will invest 35 billion yens to expand the manufacturing capacity of optical films in Onomichi Plant in 2007.
15. Kaneka (Major polyimide film supplier in Japan) 8/22
Will start the volume production of thermo plastic elastic material in Kashima Plant targeting 2 billion yen revenue in the next five years.
16. Toshiba (Major electronics company in Japan) 8/22
Will roll out a new 2.5" hard disc with 320 GB capacity in November.
17. Chisso (Major chemical company in Japan) 8/23
Will invest 6 billion yens to enlarge the manufacturing capacity or liquid crystal materials.
18. Tokyo Seimitsu (Equipment supplier in Japan) 8/23
Has commercialized a new regulation machine for the CSP substrates without dicing tapes.
Interesting literatures about the packaging industry
Articles of DKN Research
1. "2006 Global Material Projection for Flex Circuit" DKN Research, October, 2006. http://www.dknresearch.com/Products.html
2. "Introduction for the Printed Circuit Boards of Car Electronics, Flexible Circuits", (Japanese only), Dominique Numakura, Nikkan Kogyo Shinbun, June, 2006, 2400 yens.
3.New "The latest electronics package, Part IXXX, Cellular Phones", Dominique Numakura, Electronics Packaging Technology, June, 2007
4. "Five Year Projection of the Global Flexible Circuit Market" Robert Turunen, Dominique Numakura and James J. Hickman, The Board Authority, Volume 7, August, 2006
5.New "Flexible Circuit Materials", (Japanese only) Dominique Numakura, Denshi Zairyo, April, 2007
6. "Leading Edge Material and Application of Polyimide (Materials for the Advance Flexible Circuits)", Dominique Numakura, CMC publication, August, 2006
7. "Business Trends and Technology Trends of the HDI Flexible Circuits -
Roadmap for the Ultra High-Density Advanced Flexible Circuits", Dominique Numakura, KPCA, October 31, 2006
From the Major Industry Magazines
1. "Digital Inkjet Printing for Etching Circuits: Putting the Pieces in Place ofr Printed PCBs", John Ganjei, David Sawoska and Andrew Krol, CircuiTree, July, 2007.
2. "Understencil Cleaning for Process Repeatability", Trevor Warren, Circuits Assembly, July, 2007.
3. "Pick-and-Place: Users & Vendors Speak Out", Gail Flower, SMT, July, 2007
4. "The Organic Interconnect ROADMAP", Jack Fisher, Printed Circuit Design & Manufacturing, July, 2007.
5. "Optimizing the Wire Bond Process", Paul Reid, Advanced Packaging, July, 2007
7. "Under the Hood, How'd They Do That?", presented by EE Times and Techonline, May 2007
More Columns from EPTE Newsletter
EPTE Newsletter: Travel to Japan During COVIDEPTE Newsletter: A New COVID Surge in Taiwan?
EPTE Newsletter: COVID-19 PCR Test in Japan
EPTE Newsletter: Japan Failing in Vaccine Distribution
EPTE Newsletter: A Long Trip to the U.S.
EPTE Newsletter: Ten Years After Fukushima
EPTE Newsletter: Taiwan Releases 2020 PCB Production Numbers
EPTE Newsletter: The Printed Circuit Industry in China