-
- News
- Books
Featured Books
- design007 Magazine
Latest Issues
Current IssueProper Floor Planning
Floor planning decisions can make or break performance, manufacturability, and timelines. This month’s contributors weigh in with their best practices for proper floor planning and specific strategies to get it right.
Showing Some Constraint
A strong design constraint strategy carefully balances a wide range of electrical and manufacturing trade-offs. This month, we explore the key requirements, common challenges, and best practices behind building an effective constraint strategy.
All About That Route
Most designers favor manual routing, but today's interactive autorouters may be changing designers' minds by allowing users more direct control. In this issue, our expert contributors discuss a variety of manual and autorouting strategies.
- Articles
- Columns
- Links
- Media kit
||| MENU - design007 Magazine
Estimated reading time: 4 minutes
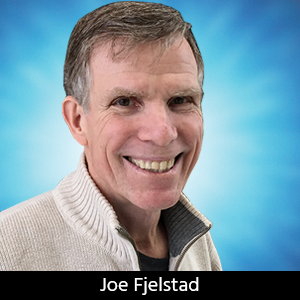
Flexible Thinking: Mechatronics in a Flex World
Mechatronics integrates two seemingly disparate engineering disciplines—mechanics and electronics—into a single subject. From my experience, the two disciplines are not the most compatible roommates because they are often at cross-purposes when implemented together. Interestingly, having been manufacturing, inventing, and writing about flexible circuits for more than four decades, I recognized that they actually fit perfectly.
In my many papers and presentations over the past years, I have often noted that a flex circuit designer is somewhat unique among circuit designers because they need to wear two hats when designing a solution for the challenge at hand. You’re frequently taking off one hat and replacing it with the other. This is because the common needs of the electronic elements of the design (routing space availability, electronic signal integrity, electromagnetic interference mitigation, etc.) will often be at odds with the design’s mechanical needs (bending, dynamic flexibility endurance, reliability, etc.). In terms of products, mechatronic solutions are often put into play where product developers need to design multipurpose electromechanical components such as actuators, sensors, and mechanisms that serve various functions of a product like robots, which are becoming increasingly common as manufacturing helpmates to improve, facilitate, or make the manufacturing process safer and more productive.
Perhaps flexible circuits are most popular simply because they are flexible and allow the designer to design and manufacture in two-dimensional space and then use the product in all three dimensions, either statically to seamlessly form fit into a box or product contour, or dynamically as might be required in the case of hinged or gated aperture that allows for rework, repair, or modification of the circuits interconnected by the flex circuit. In these cases, the designer must have some knowledge and appreciation of not only the needs for the electrical interconnections but also the mechanical requirements of the circuit to make sure the assembly will not suffer an untimely failure due to work hardening and metallurgical failure from overuse or inattention to such things as copper ductility and “I-beaming.”
I-beaming refers to the design for manufacturing steel beams used in the construction of buildings, which in cross-section look very much like the capital letter “I” or “H,” and provide superior strength-to-weight form. While good for general mechanical construction such as a building, in a flexible circuit, that strength is typically undesirable, especially in bend areas, and the designer needs to understand and appreciate that in the design process. This can be problematic in some cases where the designer is concerned with managing the characteristic impedance of a design; having a signal in specified proximity to a ground layer can create conflict if the reference pair must be bent. It can be accommodated to some degree if recognized and reacted to.
Another area of increasing interest in the past decade or so has been wearable mechatronic hardware designed to improve the lives of those debilitated by disease or injury. Referred to generally as exoskeletons, these products are wearable devices designed to support or augment the natural movements of the human body. While they came to the attention of the general public through science fiction movies such as “Alien,” they first found application in fields like the construction industry and military.
Such products are also finding use or are being proposed for many health-related uses. One example is physical rehabilitation, where mechatronic exoskeletons assist individuals in their return to physical health. Another would be to provide assistance to the growing elderly population with the mundane activities of daily living, such as walking, eating, climbing stairs etc. Such mechatronic devices could be augmented with stabilizing gyroscopes to reduce fall risk, monitor the individual’s biometrics and generally enhance quality of life for older adults.
There is arguably a third hat that could be tossed into the mechatronic equation and that is the matter of thermal management in design because of the steady increase in power demand and consumption by electronic products. It has been somewhat a “tit for tat” of spiraling challenges over the years where, when a designer has figured out a way to make a product use less energy and run cooler, the product developer sees it as a license to run the product faster and hotter. Thus, it is important that the designer pays attention to and accommodates the “getting the heat out” of their mechatronic design. Thermal management experts observe that with heat, it must “all go back to air” in some fashion, so determining the best way to facilitate that in the design will be increasingly important in the years to come if we continue down the path we are collectively on. Fortunately, there are lots of solutions bubbling up. (See my ideas on how to integrate thermal solutions into aluminum rigid-flex designs in my short book Solderless Assembly For Electronics.)
In summary, mechatronics is, in essence, a multidisciplinary field of design and manufacture that combines elements of mechanical engineering, electrical/electronics engineering, computing, and motion control engineering to design and create intelligent systems for a never-ending stream of products that serve to make our current and future lives better, safer, and more enjoyable.
Joe Fjelstad is founder and CEO of Verdant Electronics and an international authority and innovator in the field of electronic interconnection and packaging technologies with more than 185 patents issued or pending.
Download your free copy of Fjelstad’s book Flexible Circuit Technology, 4th Edition, and watch his in-depth workshop series “Flexible Circuit Technology.”
This column originally appeared in the July 2024 issue of Design007 Magazine.
More Columns from Flexible Thinking
Flexible Thinking: The Key to a Successful Flex Circuit Design TransferFlexible Thinking: Flexible Circuit Technology—Looking Back and Forward
Flexible Thinking: Mind-tapping into January
Flexible Thinking: Another PCB Design Paradigm Shift in the Works
Flexible Thinking: Rules of Thumb—A Word to the Wise
Flexible Thinking: Musings on High Density Interconnections
Flexible Thinking: Integrated Passive Devices—Design Solutions With Many Benefits
Flexible Thinking: PCB Designers Still Wanted