Estimated reading time: 6 minutes
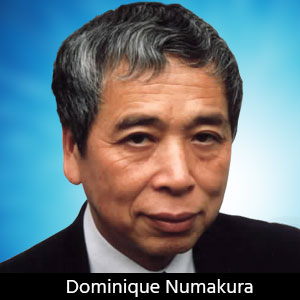
EPTE Newsletter from Japan - Flat Panel TV
The flat panel TV made its debut less than ten years ago, and has overwhelmingly won support from consumers. During its infancy, the flat panel TV was much more expensive compared to the traditional CRT TV, and the sales battle between both was very competitive. Today, the flat panel TV is the clear choice when purchasing the home entertainment center; so much so that all of the major Japanese electronics companies have terminated the production of their CRT models.
The second battle was waged between the LCD base flat panel TV and the PDP base flat panel TV relative to its size. The early rounds of the fight were won by the PDP TV since it maintained a slight advantage over its competitor with its bigger sized models (over 30 inches). During rounds, LCD manufacturers adjusted their game plan and made remarkable progress to enlarge the sizes. Nowadays, LCD TV's larger than 100 inches are available, and PDP TVs no longer have a commercial advantage in the models that are smaller than 50 inches. The third campaign began about a year ago and has manufacturers competing to produce the thinnest flat panel TV. Sharp, the leading manufacturer of the LCD TV, recently unveiled a 2 cm thick (less than one inch) 65" LCD TV and announced the availability of a thinner LCD TV may be possible in the near future. Sharp is also planning to commercialize a 106" LCD TV later this year. Pioneer, the technical leader within the PDP TV segment plans to commercialize a 9 mm thick 50" TV in the near future.A new face within the flat panel TV segment decided to throw its hat in the ring. Sony, the leading company for AV products, commercialized an 11" flat panel TV using a new organic EL display. The thickness of the TV is only 3 mm (almost one tenth of inch), and is still much smaller compared to other leading sizes of PDP and LCD TVs. However, Sony does have plans on the drawing board to quickly enlarge the sizes of their OLED TV, and other manufacturers have announced plans to develop larger flat panel TVs using this OLED technologies.There are only three countries that can produce flat panel TVs in volume: Japan, Korea and Taiwan. Japanese and Korean manufacturers compete to bring leading edge products to the marketplace, while Taiwanese manufacturers compete to bring lowest costs to the table. The evolution of the thin flat panel TV began in 2008, and benchmarks will be set to determine a new market direction.By the way, I had a chance to examine the inside of an ultra-thin OLED TV. The display wears an armor of flexible circuits for the wiring and is understandable to minimize the thickness of the flat panel TV. This makes me happy since my bread and butter is flexible circuits, but this technology could hamper the drive to reduce costs and compete against the other flat panel TVs. Cost competitiveness is the key to survive in this market.
Dominique K. Numakura
DKN Research, www.dknresearch.com
Headlines of the week
(Please contact haverhill@dknreseach.com for further information of the news.)
1. Oki Electric (Second tier electronics company in Japan) 12/24
Has developed an array LED technology for the high-resolution large size high-brightness display. There are over 500 LED elements in 1 mm square.
2. YAMAHA (Equipment vendor in Japan) 12/26
Has commercialized the industry smallest and lightest parts feeder "FS Feeder" for the high-speed SMT mounting machine.
3. Nikko Metals (Major non-ferric metal supplier in Japan) 12/26
Will open a new stock point in Taiwan for the copper recycling of the scrapped printed circuit boards.
4. Panasonic (Major electronics company in Japan) 12/28
Has started the sample supply of the world thinnest Blue Disc Drive for notebook PCs. Size: 9.5 x 128 x 127 mm.
5. Yano Keizai (Market research firm in Japan) 1/1
Has forecasted 1.6 million units of network cameras in 2008, 45% increase from the previous year for the remote control security systems.
6. Fuji Film (Major photo film and camera manufacturer in Japan) 1/7
Has had a business alliance with Adtech Engineering for the manufacturing of the digital exposure machines for printed circuit process.
7. Asahi Kasei Electronics (Major electronics material supplier in Japan) 1/7
Will start the operation of the new dry film plant in China with a capacity of 100 million square meters per year for the customers in China and Eastern Asia.
8. Sumitomo Bakelite (Major PWB material supplier in Japan) 1/7
Has cancelled the business alliance, manufacturing of paper phenol laminates in Malaysia with CMK because of the termination of the JV.
9. Ohara (Material supplier for disc drives in Japan) 1/7
Will invest 1.4 billion yens to increase the manufacturing capacity of glass substrates to 14 million discs per month from 11 million discs by July 2008.
10. Fujikura (Major manufacturer of cables and flex circuits in Japan) 1/7
Has co-developed the world smallest pressure sensor with ST Microelectronics for mobile equipment. Size: 0.8 x 0.8 mm.
11. Matsushita Electric Works (Major PWB material supplier in Japan) 1/9
Has developed a new conductive ink for the organic thick film circuits. The new ink makes a stable conductivity by metal/metal bonding through low temperature baking process.
12. Du Pont Toray (Major polyimide film supplier in Japan) 1/9
Has commercialized the new polyimide film Kapton EN-A with a better dimensional stability for driver modules of the LCD panels.
13. DaiNippon Printing (Major printing company in Japan) 1/9
Has started the volume production of the new multi-layer boards with embedded passive and active chips for mobile electronics.
14. ShinEtsu Polymer (Major elastic material supplier in Japan) 1/9
Will found a new subsidiary in India for the manufacturing of key pads of cellular phones. The volume operation will start in October 2008.
15. Showa Denko (Major chemical company in Japan) 10/10
Has started the volume production of 1.3" disc substrates for the small size 40 GB class hard disc drives.
16. Hitachi Chemical (Major electronics material supplier in Japan) 1/10
Will invest 2 billion yens to increase the manufacturing capacity of die bonding film 70% to 2 million square meters per year by May 2008.
17. Panasonic Factory Solutions (Equipment vendor in Japan) 1/15
Has developed a new flip chip assembling process using conductive resin with solder powders. It makes a reliable bonding with a smaller pressure.
18. Hitachi Chemical (Major electronics material supplier in Japan) 1/15
Has commercialized a new copper laminate, MCL-E-679GT with low CTE for the substrates of IC packaging.
19. YAMAHA (Equipment manufacturer in Japan) 1/15
Will roll out new SMT mounting machines, "YS12" and "YG12" for the high density assembling. The machines have the highest space efficiencies in the industry.
Interesting literatures about the packaging industry
Articles of DKN Research
1. New "Screen Printing for High-Density Flexible Electronics", Robert Turunen, Masafumi Nakayama and Dominique Numakura, Printed Circuit FAB, October, 2007, http://pcdandm.com/cms/content/view/3846/95/
2. New "Total Process Solution for the High-Density Multi-layer Flexible Printable Electronic Circuits", (Japanese only) Dominique Numakura, Denshi Zairyo, October, 2007
3. New "The latest electronics package, Part XXXI, Cellular Phones", Dominique Numakura, Electronics Packaging Technology, October, 2007
4. New "Coombs' Printed Circuits Handbook, 6th Edition, Part 15-Flexible Circuits", Dominique Numakura, McGraw Hill, New York, September, 2007
5. New "DKN Research Develops Film Base Connector", Circuits Assembly, September, 2007.
6. "Flexible Circuit Materials", (Japanese only) Dominique Numakura, Denshi Zairyo, April, 2007
7. "Business Trends and Technology Trends of the HDI Flexible Circuits -
Roadmap for the Ultra High-Density Advanced Flexible Circuits", Dominique Numakura, KPCA, October 31, 2006
From the Major Industry Magazines
1. "Embedded Active Technologies for Convergent Microelectronic Systems", Baik-Woo Lee, Chong K. Yoon, Venky Sundaram, Mahadevan Iyer and Rao R. Tummala, CircuiTree, January, 2008.
2. "Flux Selection for Lead-Free Wave Soldering", Douglas Watson, Jasbir Bath and Pan Wei Chih, Circuits Assembly, January, 2008.
3. "Evaluating Cleaning System Performance", Steve Stach and Mike Bixenman, SMT, December, 2007
4. "Designing to Improve PTH Reliability", Kathy Zulki Khan, Printed Circuit Design & FAB, January, 2008.
5. "Thick Copper Pillar Bump Fabrication", W.W. Flack, H Nguyen, E. Capsuto and C. McEwen, Advanced Packaging, November/December, 2007
7. "Under the Hood, Efficiency vs. Speed", presented by EE Times and Techonline, October 8, 2007
More Columns from EPTE Newsletter
EPTE Newsletter: Travel to Japan During COVIDEPTE Newsletter: A New COVID Surge in Taiwan?
EPTE Newsletter: COVID-19 PCR Test in Japan
EPTE Newsletter: Japan Failing in Vaccine Distribution
EPTE Newsletter: A Long Trip to the U.S.
EPTE Newsletter: Ten Years After Fukushima
EPTE Newsletter: Taiwan Releases 2020 PCB Production Numbers
EPTE Newsletter: The Printed Circuit Industry in China