Estimated reading time: 4 minutes
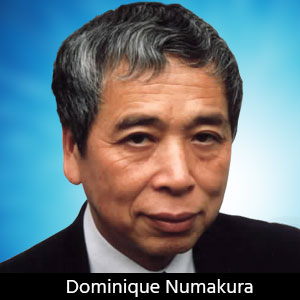
EPTE Newsletter from Japan - Printable Electronics: Trying To Popularize Trends
The printable electronics industry commonly develops new products that are trendsetting and almost guaranteed to generate demand. Over the last few years, the electronics and materials industry jumped on the bandwagon and their new concepts were the vogue. Several examples include nano-technologies, embedded technologies, and organic electronics, just to name a few. The marketing executives for these companies like to use captivating nouns and adjectives such as "laser", "plasma", "jet" and "virtual" so the concept is perceived as cutting edge.
Printable and Flexible Electronics has become one of these "cutting edge" concepts in the electronics industry over the last few years. Printable electronics is a main topic of discussion at many material companies, equipment manufacturing universities and institutes, and one marketing research firm estimated that the global market for printable electronics will be over ten billion US dollars within the next five years. The primary application for printable electronics is memory module followed by photovoltaic devices. Market research reports indicate the key technology for printable electronics is an organic semiconductor material that includes organic EL materials. Many researchers from material companies spend a bulk of their time and budget trying to develop new printable semiconductor materials. Nano-paste material is the buzz work with printable electronics. Unfortunately, I am skeptical for a practical commercialized use with these materials in the next three to five years. The basic ideas for them are very innovative, but require more tweaking and lab time before introducing the actual devices to a commercial environment.
Several equipment manufacturers share the same opinion that using inkjet printing is the correct technology to generate printable electronics on substrates. They claim the latest inkjet nozzles can generate 20micron lines at high speed. This sounds like a brilliant idea; however, I question if the inkjet technology is better than other printing technologies. The practical resolution for inkjet printing is less than 50 micron lines and spaces, and the applicable ink materials are very limited. The traditional screen-printing process has seen many advances over the last few years, and can produce finer traces than 20 microns, and it definitely has much higher printing speeds than inkjets which is important with volume productions.
The polymer thick film circuits made by the screen-printing process are not a new technology, but in my opinion, is the bona fide choice for printable and flexible electronics. The basic technologies were established over thirty years ago, and large volumes were used as the membrane switches for PC's keyboards and touch panel switches in microwaves. The applications were expanded for use with home appliances, office equipment and medical devices. I estimate the total market for these products is already over the billion dollar mark measured in US dollars, and continue to grow.
Screen-printing may be perceived as out of style because of its long history, but over the last few years has had a complete makeover. It can generate patterns finer than 20micron traces, and appropriate combinations with a good non-nano silber paste can generate 30micron traces with high conductivities for not only single side circuits, but also double and multi-layer circuits. It can build embedded passive circuits with a much simpler process than other technologies. Embedded active circuits are very practical when suitable ink materials are available, and will generate a large market with new applications such as flexible displays and solar cell batteries.
I agree with industry experts that printable electronics has the potential to become a revitalized and large market in the near future, but I have different opinions with the practical R&D approaches to commercializing the products. At the risk of sounding old fashioned, I would like material researchers and device designers to consider traditional methods, while upgrading the printing processes for new materials.
Dominique K. Numakura
DKN Research, www.dknresearch.com
Headlines of the week
(Please contact haverhill@dknreseach.com for further information on the news.)
1. Fujitsu (Major electronics company in Japan) 3/24
Has unveiled a new 2.5" hard disc drive with a 320 GB capacity at 7200 RPM.
2. Showa Denko (Major chemical company in Japan) 3/24
Will increase the selling prices of the polishing materials for the manufacturing process of glass substrates because of the extreme increase of the raw materials.
3. NEC Semicon Package (Packaging subsidiary of NEC Electronics) 3/25
Will increase the manufacturing capacity of automobile semiconductor packages to one million units per month.
4. Fuji Chimera (Market research firm in Japan) 3/25
Has released the new forecast of the global flat TV market in 2011. LCD TV will grow 75.9% to 79 million units from 2007.
5. Fuji Chimera (Market research firm in Japan) 3/25
Has released the production data of the global PC market in 2007. The total number grew 15% to 272 million units. Notebook PC grew 27.1% to 108 million units.
6. JPCA (Industrial organization in Japan) 3/26
Has forecasted the whole market of printed circuit industry in Japan grows 1.0% in 2008 to 1.39 trillion yens. It will grow to 1.61 trillion yens by 2012.
7. Nitta (Telecommunication module supplier in Japan) 3/26
Has been developing a new optical wave guide modules for the American market. The new modules will use film type quartz wave guide.
8. Takebane Sangyo (Device manufacturer in Japan) 3/27
Has been developing a low cost process for the manufacturing of MEMS devices. The new printing process will reduce the processing cost 80%.
9. NEC Electronics (Major device manufacturer in Japan) 3/27
Will switch all packaging materials for the linear CCD sensors to plastic from ceramic to reduce the manufacturing cost.
10. Hitachi Cable (Major cable company in Japan) 3/28
Has founded a new manufacturing subsidiary in Vietnam. The company will start the operation in May 2009 for electronics wire harness.
11. Tokyo Institute of Technology (Japan) 3/28
Has co-developed a new material for the next generation non-volatile memory with Fujitsu. The bismuth ferrite base material could be capable for 256 M bit devices.
12. Mitsubishi Chemical (Major chemical company in Japan) 3/28
Will build a volume manufacturing line in Mizushima Plant for the cathode materials of the lithium ion batteries with a capacity of 600 tons per year.
More Columns from EPTE Newsletter
EPTE Newsletter: Travel to Japan During COVIDEPTE Newsletter: A New COVID Surge in Taiwan?
EPTE Newsletter: COVID-19 PCR Test in Japan
EPTE Newsletter: Japan Failing in Vaccine Distribution
EPTE Newsletter: A Long Trip to the U.S.
EPTE Newsletter: Ten Years After Fukushima
EPTE Newsletter: Taiwan Releases 2020 PCB Production Numbers
EPTE Newsletter: The Printed Circuit Industry in China