Estimated reading time: 5 minutes
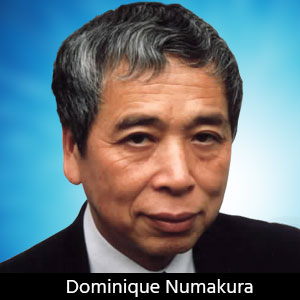
EPTE Newsletter from Japan--JPCA Show, Part II
The hot item at the JPCA convention this year was embedded components in multilayer boards and flexible circuits. Embedded components seems to be a very "fashionable" trend, started last year, and most of the major rigid board companies and flexible circuit manufacturers paraded their latest achievements from their technological departments at the show. Material suppliers and machine manufacturers also threw their hats in the ring by featuring sales pitches that involved embedded components.
Two basic technologies are used for embedded components. The first technology is forming passive components by screen-printing or photolithography inside or outside the circuit board. The concept is not very new--the technology came to light and really took off several years ago at the IPC Expo in the U.S. The basic idea has not changed; however, the idea has evolved and the accuracies and value of the passive components have become much larger.
Mitsui Metal Smelting released 8-micron thick dielectric layers for Farady Flex, while Fujikura Kasei announced that 50 are available as the dielectric constant of the screen printable ink. For circuit manufacturers, this allows the formation of larger capacitances in the same spaces on substrates compared with traditional materials. Asahi Chemical Laboratory provides several carbon conductor inks for embedded resistors. These carbon inks cover five orders of resistors 100 ohms to 10 mega ohms in small spaces by the screen printing processes.
The second basic technology used for embedded components involves mounting the chip components inside the multi-layer boards. During the early stages of the development process for the technology, actual chip devices for passive components were introduced. Today, major circuit board manufacturers are trying to use semiconductor chips as embedded components. Thin semiconductor chips are mounted in small cavities already prepared inside the multilayer boards. Because the wire-bonding technology has physical difficulties when covered by the other circuit layers, manufacturers began experimenting with new connection technologies. The flip-chip process is probably the most common technology used to make the connections for mounted chips. Toray Engineering, a major equipment supplier for the circuit board and assembling industry, launched new lines of flip chip bonding machines for both rigid substrates and thin flexible substrates. The automated bonding machines pick up the small, thin chips from trays or diced wafers for large size circuit boards. One manager from Toray engineering told me they are selling many flip chip bonding machines to new customers from circuit board companies, flex circuit manufacturers and OEM assembling companies. Toray Engineering representatives speculate these new customers use the machines for embedded semiconductor chips.
I surveyed major rigid board manufacturers and flex circuit manufacturers inquiring about the latest progress with embedded component technologies. Most manufacturers spoke about the advantages of their technologies, but few could provide clear answers relative to the reliabilities and actual production volumes. DNP, one of the major circuit board manufacturers in Japan, was the only company that provided actual samples of the circuit modules with embedded semiconductor chips. DNP representatives stated that they ship millions of embedded modules every month to a European cellular phone manufacturer.I came away from the exhibition feeling that embedded components are still in the R&D stage. Both circuit board manufacturers and their customers are wondering whether embedded components will be part of the industry main stream and, if the technology is adopted, what the major process for the technology will be.Dominique K. Numakura
DKN Research, http://www.dknresearch.com/
Headlines of the Week
(Please contact haverhill@dknreseach.com for further information on the news.)1. Toyo Kogyo (Circuit board shop in Japan) 6/9The shop suffered bankruptcy as of May 1, 2008 and will discontinue operations.
2. CPT (Major display manufacturer in Taiwan) 6/12The manufacturer has commercialized a new, full-color 15.4" TFT LCD panel without a color filter.3. Ishii Hyoki (Equipment supplier in Japan) 6/12The supplier has unveiled a new vertical-type scrubbing machine for thin flexible laminates.4. Hitachi Chemical (Major material supplier for circuit board) 6/13The company has developed the world thinnest polyimide base copper foil laminate. Total thickness is 12 microns; base layer is 3 microns; and the copper foil is 9 microns.5. Toppan Printing (Major printing company in Japan) 6/12The company has commercialized the trial kit for the RFTAG control system for the manufacturing process of printed circuit boards.6. Sharp (Major electronics company in Japan) 6/16The company has commercialized a 108" full color LCD display panel for business use. Sharp hopes to sell 3,000 units in the next two years.7. Oki Cable (Cable and circuit board manufacturer in Japan) 6/16The manufacturer has developed a new 3-D wiring technology with flexible circuits using a new graft polymer.8. Sanyo Electric (Major electronics company in Japan) 6/17The company will build a new solar cell plant in Kaizuka, Osaka.The total manufacturing capacity will be doubled to over 600 MW per year by 2010.9. Toray (Major material supplier in Japan) 6/17The supplier has developed a new extruding process to produce optical wave guide film for optical telecommunications systems.10. Samsung Electronics (Major electronics company in Korea) 6/18The company is considering spinning off its business of AMOLED (Active Matrix-type OLED) to survive international competition.11. Mektron (Major flexible circuit manufacturer in Japan) 6/19The manufacturer has developed transparent flexible circuits to be commercialized by the end of the 2008.12. Mitsubishi Chemical (Major chemical company in Japan) 6/20The company will terminate its recycling business of glass substrate materials of LCD devices in Taiwan.Interesting Literatures Concerning the Packaging IndustryArticles from DKN Research1. "Screen Printing for High-Density Flexible Electronics," Robert Turunen, Masafumi Nakayama and Dominique Numakura, Printed Circuit FAB, October, 2007, http://pcdandm.com/cms/content/view/3846/95/.2. "Total Process Solution for the High-Density Multi-layer Flexible Printable Electronic Circuits," Dominique Numakura, Denshi Zairyo, October, 2007, (Japanese only).3. New "Roll to Roll Production of Flexible Circuits, Possibilities and Issues," Dominique Numakura, Joho Kiko, Tokyo, March 2008, (Japanese only).4. "Coombs' Printed Circuits Handbook, 6th Edition, Part 15-Flexible Circuits," Dominique Numakura, McGraw Hill, New York, September, 2007.5. New "Screen Printing Process for High Density Flexible Electronics," Robert Turunen, Dominique Numakura, Masafumi Nakayama and Hisayuki Kawasaki, IPC Printed Circuit Expo/APEX and the Designers Summit, April 2008.6. New "Global Flexible Circuit Industry, Market Trends and Technology Trends by Applications," Dominique Numakura, International Symposium of KPCA Show, April, 2008, (English PowerPoint file is available).From the Major Industry Magazines1. "Vacuum Etching Technology, Combined Processes and Interesting Development," Volker Feyeravbend, CircuiTree, June 2008. 2. "Evaluating Manufacturability and Operational Costs for New Conformal Coating Processes," Jason Keeping, Circuits Assembly, May 2008.3. "Alternative Replace Older Cleaners," Mike Jones and Tom Tattersall, SMT, May, 2008.4. "Don't Let Your Signals, STUB THEIR TOES," Eric Bogatin, Printed Circuit Design & FAB, May, 2008.5. "DRIE for MEMS devices," Michel Puech, Jean-Marc Thevenoud, et al, Advanced Packaging, April, 2008.7. "Nanotechnology and mathematical methods for high-performance thermal interface materials," Sara N. Paisner, Global SMT & Packaging, May 2008.8. "Microflex Circuit Applications for Medical Devices," Luke Volpe, MD & DI Magazine, January 2008.
More Columns from EPTE Newsletter
EPTE Newsletter: Travel to Japan During COVIDEPTE Newsletter: A New COVID Surge in Taiwan?
EPTE Newsletter: COVID-19 PCR Test in Japan
EPTE Newsletter: Japan Failing in Vaccine Distribution
EPTE Newsletter: A Long Trip to the U.S.
EPTE Newsletter: Ten Years After Fukushima
EPTE Newsletter: Taiwan Releases 2020 PCB Production Numbers
EPTE Newsletter: The Printed Circuit Industry in China