Estimated reading time: 5 minutes
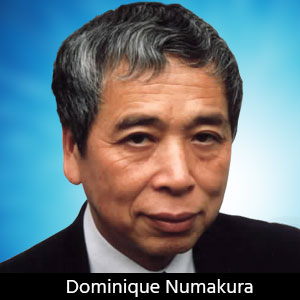
EPTE Newsletter from Japan--JPCA Show, Part III
The benchmark isn't set for the high-density fine line circuit segment from the Japanese printed circuit industry. The frontrunners for circuit manufacturers featured their fine line capabilities during the exhibition in a very competitive nature. I could not check all of them, but I viewed several examples from manufacturers. Fifty micron pitch traces with smaller blind vias for multi-layer IC substrates or double-sided flexible circuits are the minimum level set for volume manufacturers of high-density circuits. Thirty micron pitch traces, which translates into a 15 micron line and space, are already very common for single side COF substrates for flexible or flexible tape circuits. Representatives working in the booths for some of the prominent companies explained that they did not display volume production samples, but they can produce 25 micron pitch traces on flexible film substrates in large volume using roll-to-roll processes.
Leading manufacturers and industry experts are currently discussing the basic manufacturing processes for traces finer than 10 microns. Mitsui Metal Smelting announced it can produce 20 micron pitch traces using an etching process with high-resolution photolithography. Several printing machine manufacturers and screen mask suppliers agree that it is very possible to generate lines finer than 10 micron using a screen-printing process. To back up their statement, they provided microscope photos of the fine lines. They were photos of etching resist produced by screen-printing; unfortunately, these companies are not capable of conducting fine etching. They advise the etching companies to use these printing technologies, but the etching companies are currently hesitant to adopt this strategy.
The semi-additive process is an alternative solution to produce traces finer than 10 microns, and several manufacturers displayed samples. Taiyo Industries, a mid-sized flex circuit manufacturer, displayed 15 micron pitch traces built on flexible substrates, stating the fine circuits were produced using a semi-additive process. FCM, another mid-sized flex circuit manufacturer, displayed 10 micron lines built on both sides of thin polyimide films. An engineering manager from FCM explained they made micro via holes by laser and conductive seed layers using a semi-additive sputtering process.
The semi-additive process with thin seed layers on the substrates could be the secure process to produce lines finer than 10 microns. The problem is its relatively high cost compared with the traditional etching process, making manufacturers hesitant to try the semi-additive process.
There are probably not many solutions to generate micro via holes. The current procedure uses mechanical drilling, which is capable of producing 50 micron via holes. Laser is the only solution for holes smaller than 50 microns, especially for the blind via holes. Until recently, UV-YAG laser was the leader in generating micro via holes. Now, fiver laser, the new face of the industry, has grown dramatically over the last few years and continues to do so because of its high power and low cost.
Dominique K. Numakura
DKN Research, http://www.dknresearch.com/
Headlines of the Week
(Please contact haverhill@dknreseach.com for further information of the news.)
1. Hitachi Chemical (Major electronics material supplier in Japan) 6/20Has developed a new film type materials as the optical wave guide applicable on the printed circuits boards. Core size: 30~100 micron, Loss: 0.04 dB/cm
2. Furukawa Electric (Major cable and copper product supplier in Japan) 6/23Will takeover Furukawa Circuit Foil, one of the major copper foil vendors in Japan to make engineering efficiencies higher.
3. Nichiyu (Petroleum chemistry company in Japan) 6/23Will start the material business of printed circuit boards. It has been developing new products cooperating with Oki Printed Circuits.
4. Panasonic (Major electronics company in Japan) 6/24Plans to start the volume production of 37" size OLED TV in 2011.
5. Epson Toyocom (Device manufacturer in Japan) 6/24Has completed the construction of the new plant in China for the manufacturing of quartz devices. Actual production will start soon.
6. Casio (Major electronics company in Japan) 6/24Has commercialized a new transparent LCD module for business use.
7. Fuji Sankei Business (Business media in Japan) 6/25Rare metal recycling rates of cellular phones have been becoming worse in Japan. The users concern leak of private information from the memory devices.
8. Toray-Du Pont (Major polyimide film supplier in Japan) 6/25Has developed 7.7 micron thick polyimide film for the mobile electronics. Most of the properties are equivalent as traditional polyimide films.
9. Fujitsu (Major electronics company in Japan) 6/25Will increase the production of 2.5" hard disc drives 80% to 5.5 million units per month by 2010 to satisfy the booming demands of personal computers.
10. Dai Nippon Screen (Equipment supplier in Japan) 6/23Has developed a new AOI machine "FP-8200" for HDI circuit boards. New high-resolution color sensor detects the defects on the plated conductors. (Au, Cu and solder)
11. TMD (Major display manufacturer in Japan) 6/27Will strengthen the business of low-temperature poly-silicon LCD to make the finance positive.
Interesting Literatures About The Packaging Industry
Articles of DKN Research
1. "Screen Printing for High-Density Flexible Electronics", Robert Turunen, Masafumi Nakayama and Dominique Numakura, Printed Circuit FAB, October, 2007, http://pcdandm.com/cms/content/view/3846/95/
2. "Total Process Solution for the High-Density Multi-layer Flexible Printable Electronic Circuits", (Japanese only) Dominique Numakura, Denshi Zairyo, October, 2007
3. (New) "Roll to Roll Production of Flexible Circuits, Possibilities and Issues" Dominique Numakura, Joho Kiko, Tokyo, March 2008 (Japanese only)
4. "Coombs' Printed Circuits Handbook, 6th Edition, Part 15-Flexible Circuits", Dominique Numakura, McGraw Hill, New York, September, 2007
5. (New) "Screen Printing Process for High Density Flexible Electronics", Robert Turunen, Dominique Numakura, Masafumi Nakayama and Hisayuki Kawasaki, IPC Printed Circuit Expo/APEX and the Designers Summit, April 2008.
6. (New) "Global Flexible Circuit Industry, Market Trends and Technology Trends by Applications", Dominique Numakura, International Symposium of KPCA Show, April, 2008 (English power point file is available.)
From the Major Industry Magazines
1. "Vacuum Etching Technology, Combined Processes and Interesting Development", Volker Feyeravbend, CircuiTree, June 2008.
2. "Evaluating Manufacturability and Operational Costs for New Conformal Coating Processes", Jason Keeping, Circuits Assembly, May 2008.
3. "Alternative Replace Older Cleaners", Mike Jones and Tom Tattersall, SMT, May, 2008
4. "Don't Let Your Signals, STUB THEIR TOES", Eric Bogatin, Printed Circuit Design & FAB, May, 2008.
5. "DRIE for MEMS devices", Michel Puech, Jean-Marc Thevenoud, et al, Advanced Packaging, April, 2008
7. "Nanotechnology and mathematical methods for high-performance thrmal interface materials", Sara N. Paisner, Global SMT & Packaging, May 2008
8. "Microflex Circuit Applications for Medical Devices", Luke Volpe, MD & DI Magazine, January 2008
More Columns from EPTE Newsletter
EPTE Newsletter: Travel to Japan During COVIDEPTE Newsletter: A New COVID Surge in Taiwan?
EPTE Newsletter: COVID-19 PCR Test in Japan
EPTE Newsletter: Japan Failing in Vaccine Distribution
EPTE Newsletter: A Long Trip to the U.S.
EPTE Newsletter: Ten Years After Fukushima
EPTE Newsletter: Taiwan Releases 2020 PCB Production Numbers
EPTE Newsletter: The Printed Circuit Industry in China