Estimated reading time: 6 minutes
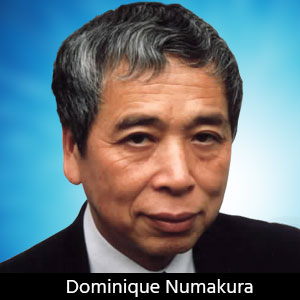
EPTE Newsletter from Japan--JPCA Show 2008, Part V
Since most assembly processes for printed circuit boards occurs at customer locations, assembly is one of the major factors considered by purchasing representatives. Many assembling equipment suppliers were in attendance at the JPCA show, as well as manufacturers for related products, and most shared relatively large floor spaces.
Giant machine suppliers, such as Panasonic and JUKI, reserved large spaces and demonstrated the workings of their mounting machines for electronic components in high-density circuit boards. Most of the mounting machine manufacture representatives shared common phrases in all their sales presentations, such as "higher mounting speeds," "capabilities for the smallest and finest components," "flexibilities for the different types of boards and components" and "lower assembling costs." Great sales pitch; however, most of us know that one machine or system cannot satisfy all of these requirements.
High-speed mounting is always the key measurement for machines, and machine companies are very competitive when it comes to trying to outdo each other with mounting speeds. Volume production machines are capable to mount over 100,000 chip components per hour with multiple heads for standard conditions. Most of the machines are capable of managing the smallest standard size components, 0402 (01005 by American standard), and some of the more prominent companies at the exhibition spoke of even smaller sizes--0201 (the American standard measurement does not have a grade for this size). A representative from another company told me the majority of the chip components used in the consumer electronics industry is still 1005 size (0402 size measured by the American standard).
The flexibility from these mounting machines allows the execution of different kinds of components including chip components, several different types of IC packages and irregularly shaped components like connectors. Machine manufacturers showcased relatively small machines with high flexibilities. I spoke with one manager from a machine manufacturer who explained that small- and mid- sized assemblers, as well as prototype EMS companies from Japan, the U.S. and Europe, do not focus on high speeds, but, rather, a flexibility to manage many different products from a small line. One difficulty the industry faces is satisfying the need for both higher speeds and flexibilities from the same assembly line.
Panasonic featured a unique mounting machine for multi-layer rigid/flex products. The engineering representatives at the booth explained that the machine is capable of managing low -quality, non-flat rigid/flex because of the high flexibility and great dimension control. I observed the machine mounting small components with high reliability for the waved rigid/flex and I knew the manufacturer who's rigid/flex was chosen for demonstration purposes. The manager was happy his company's products were used by Panasonic for the demonstration, but he was unhappy that the products selected were low-quality rigid/flex.
Soldering is another key aspect with circuit board assembly. Major soldering material suppliers, such as Nihon Superior and Senju Metal, always reserve relatively large spaces at the exhibition. I did not discover any new innovative products or review any new topics from the soldering zone. Lead-free solder is already standard in the industry, but material suppliers communicated their need for a new soldering material to evolve as the second generation of lead-free soldering. One manager representing a soldering material supplier spoke to me about the next generation soldering called Green assembly, which is typically halogen-free. He went on to say that his company is developing new soldering materials, including flux, for next generation assembly.
These comments seemed a bit contradictory from those made by sales presentations several years ago. Soldering material suppliers at that time announced that new soldering materials were perfect to satisfy both lead-free and productivity requirements and the material cost were higher than lead base soldering systems. The assembly companies fixed the soldering conditions with the first stage soldering materials, and probably will not make any changes for the next few years. Still, the soldering material companies are introducing new materials and costs to the assembly companies are higher. I am not sure how much interest assembly companies will have for these new soldering systems.
Dominique K. Numakura
DKN Research, http://www.dknresearch.com/
Headlines of the Week
(Please contact haverhill@dknreseach.com for further information on the news.)
1. Optimax (Material supplier in Taiwan) 7/7The supplier will double its shipment of polarization films for LG Display in Korea to NT $100 million per month in July.
2. Mitsubishi Plastic (Major plastic material supplier in Japan) 7/1The company has commercialized a new transparent film "X-BARRIER" for packages of electronic components. The film minimizes moisture permeability.
3. LDK Solar (Material supplier in China) 7/7The supplier will expand its manufacturing capacity of poly silicon for solar battery manufacturers in Taiwan to 1,000 tons per month.
4. Fuji Sankei Business (Business magazine in Japan) 7/7The magazine reports that over 70% of Japanese are still watching CRT TV at home. Less than 40% have LCD TV, but that number is continually increasing.
5. Toppan Printing (Major printing company in Japan) 7/7The company has commercialized content delivery service system with electronic papers.
6. Canon (Major electronics company in Japan) 7/7The company will invest over 17 billion yen to build a new assembly plant for digital cameras in Nagasaki Prefecture by the end of 2009. Plant capacity will be 4 million units per year.
7. Pioneer (Major electronics company in Japan) 7/7The company has developed a new optical disc with 400 GB introducing a new 16-layer recording technology.
8. TDK (Major component supplier in Japan) 7/8The supplier will begin the production of small-size thermal printer heads for ID card applications in July.
9. CMO (Major display manufacturer in Taiwan) 7/8The manufacturer expects 40% growth this year--with the global market share rising 1% to 15%.
10. Poly Plastic (Plastic resin supplier in Japan) 7/8The supplier has been developing the applications of low tangent loss plastic resin "Flectis" in high frequency equipment. The new resin is capable of changing the epsilon from 5 to 20.
11. MARUWA (Circuit board manufacturer in Japan) 7/8The manufacturer will double its capacity of ceramic base multi-layer boards for automobile applications.
12. Nikko Metal (Major copper foil supplier in Japan) 7/8The supplier has commercialized ultra thin RA copper foil (8 and 9 micron thick) for hinge flexible circuits of cellular phones.
13. Yokogawa Electric (Major electronics company in Japan) 7/10The company will expand manufacturing capacity of displays for the avionics applications by 50% to 4,500 units per year by autumn of this year.
Interesting Literature Concerning the Packaging Industry
Articles from DKN Research
1. "Screen Printing for High-Density Flexible Electronics," Robert Turunen, Masafumi Nakayama and Dominique Numakura, Printed Circuit FAB, October, 2007, http://pcdandm.com/cms/content/view/3846/95/.
2. "Total Process Solution for the High-Density Multi-layer Flexible Printable Electronic Circuits," Dominique Numakura, Denshi Zairyo, October, 2007 (Japanese only).
3. New "Roll to Roll Production of Flexible Circuits, Possibilities and Issues," Dominique Numakura, Joho Kiko, Tokyo, March 2008 (Japanese only).
4. "Coombs' Printed Circuits Handbook, 6th Edition, Part 15-Flexible Circuits," Dominique Numakura, McGraw Hill, New York, September, 2007.
5. New "Screen Printing Process for High Density Flexible Electronics," Robert Turunen, Dominique Numakura, Masafumi Nakayama and Hisayuki Kawasaki, IPC Printed Circuit Expo/APEX and the Designers Summit, April 2008.
6. New "Global Flexible Circuit Industry, Market Trends and Technology Trends by Applications," Dominique Numakura, International Symposium of KPCA Show, April, 2008 (English PowerPoint file is available).
From the Major Industry Magazines
1. "Toward a PCB Production Floor Metric for Go/No Go Testing of Lossy High-Speed Transmission Lines," Brandon Gore, Richard Mellitz, Jeff Loyer, Martyn Gaudion, Jean Burnikell and Paul Carre, CircuiTree, July 2008.
2. "Measuring and Controlling Wave Height and Dwell Time," Ken Kirby, Circuits Assembly, June 2008.
3. "Laser Soldering: A Turning Point," Dave Sigillo, SMT, June, 2008.
4. "Drilling of PCBs--an Overview," Todd Lizotte, Gabor Kardos and Ronald D. Schaeffer, Printed Circuit Design & FAB, June, 2008.
5. "Flash Memory for Stacked PoP Technology," Kenneth Sean, Bertrand Wong, Goh Swee Heng and Tan Choon Leng, Advanced Packaging, May/June, 2008.
7. "Process and assembly method for increased yield of PoP devices," Brian Toleno and Dan Maslyk, Global SMT & Packaging, June 2008.
8. "Microflex Circuit Applications for Medical Devices," Luke Volpe, MD & DI Magazine, January 2008.
More Columns from EPTE Newsletter
EPTE Newsletter: Travel to Japan During COVIDEPTE Newsletter: A New COVID Surge in Taiwan?
EPTE Newsletter: COVID-19 PCR Test in Japan
EPTE Newsletter: Japan Failing in Vaccine Distribution
EPTE Newsletter: A Long Trip to the U.S.
EPTE Newsletter: Ten Years After Fukushima
EPTE Newsletter: Taiwan Releases 2020 PCB Production Numbers
EPTE Newsletter: The Printed Circuit Industry in China