Estimated reading time: 5 minutes
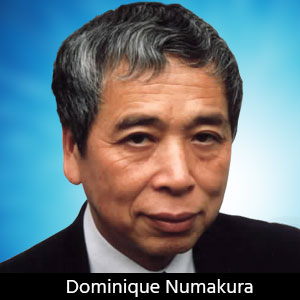
EPTE Newsletter from Japan - An Old Clock Radio (Plated Through Holes)
Topics Of The Week
An Old Clock Radio (plated through holes)
In the past, I may have written about my early studies of electronics. I have fond memories of tearing apart an old clock radio made from GE during the 1950s. There were no transistors and ICs used in the circuits, and five vacuum tubes were used instead for the electronics. All passive components are lead wire type, and a lot of fine mechanical gears were used to operate the analog type clock.
Surprisingly, most of the components were mounted on a printed circuit board; furthermore, the circuit board was double side construction. From what I understand, during this era, vacuum tubes were mechanically mounted on the metal chassis with a socket fixed by eyelets; however, there was clear evidence that the newly developed double sided printed board was used for a clock radio - a typical consumer product. The vacuum tube sockets had special terminals for soldering on the circuit boards.
I asked David Wolf, the president of PD Circuits, whether the holes had plated copper layers for the whole connections. David referred me to Ann Mary of the QA department, who conducted a cross-section analysis of the holes. Ann Mary developed exceptional cross section photos of the holes and we determined there was about 50 micron thick plated copper layers inside of one millimeter diameter holes. I recognized a conductive layer under the plated copper. The thickness of the copper layers is not very uniform, but it looks reliable. Bruce MacDonald, material specialist for the company, speculated that the base material could be Bakelite with some inorganic fillers, what is not a commonly used material these days.
I think the double side circuit with through holes was a very expensive material for the consumer electronics industry during that era. I have great respect for the GE engineers during this time period. They are well into their eighties, and if I could correspond with them, I would communicate my appreciation for their great design concept and reliability with the new technologies introduced for consumer products. I would also ask about their decision process with introducing the printed circuit boards.
Attached are two photos showing radio parts from my tear down study of the old clock radio. I am preparing a photo album and report of this tear down analysis including cross-sections. If you are interested, I will send the report by e-mail free of charge. Please send me a request by mail.
Dominique Numakura, DKN Research (dnumakura@dknresearch.com)
Headlines of the week
1. Toa TDK (Component & module supplier in Japan) 7/24
Will invest 350 million yens for the PWB assembling lines to complete RoHS capabilities.
2. Asahi Glass (Major glass material supplier in Japan) 7/25
Will reduce the global manufacturing capacity of the glass materials for CRT 35%. The market has been moving to FPD.
3. Sumitomo Heavy Industry (Equipment manufacturer in Japan) 7/25
Has rolled out a new high-speed carbon oxide laser system for the micro hole drilling of the high-density circuit boards. 2000 hit per second.
4. Matsushita Electric Works (Major laminate supplier in Japan) 7/24
Will increase the selling price of the phenol resins 25 yens per kg again from Aug. 1st.
5. Showa Denko (Major chemical company in Japan) 7/26
Will expand the manufacturing capacity of hard discs. The total capacity of three plants will be 15.75 million discs per month by end of 2006.
6. CMK (Major PWB manufacturer in Japan) 7/26
Will invest 10.8 billion yens to expand the capabilities of the plant in Thailand in 2006. It is more than half of the whole investment of the company.
7. Uemura Kogyo (Chemical supplier for PWB manufacturing process) 7/26
Will invest over 3.5 billion yens to improve the manufacturing facilities in Japan and China in 2006.
8. Alps Electric (Major components supplier in Japan) 7/26
Has developed three new two mega pixel cameras for cellular phone applications. The cameras have different focusing performances, but they have the same size packages.
9. Horiuchi Denki (Equipment manufacturer in Japan) 7/26
Has commercialized a new soldering robot with laser. An automatic image guide system provides a high accuracy.
10. Seiko Epson (Major electronics company in Japan) 7/26
Has developed a high resolution electronic paper. A-4 size flexible display was demonstrated with 1536 x 2048 pixels.11. Tokki (Equipment manufacturer in Japan) 7/26
Opened a new R&D center in Kyushu for the manufacturing equipment of organic EL displays.
12. Nihon Zeon (Chemical company in Japan) 7/26
Will invest 10 billion yens to build a new plant of optical films for LCD devices. The operation will start in July 2007.
13. JAE (Major connector manufacturer in Japan) 7/27
Is planning to expand the business of consumer use connectors targeting flat panel TV market.
Interesting literatures about the packaging industry
Articles of DKN Research
1. "Digest Version of the 2006 Global Projection for Flex Circuit" DKN Research, March 2006. http://www.dknresearch.com/GPFC2006.html
2. "Easy understanding Series, How to make IC packages", (Japanese only), Jan Vardaman & Dominique Numakura, Nikkan Kogyo Shinbun, December, 2005, 1,800 yens.
3. "The latest semiconductor package, Part XV, Termination Technologies-Direct Bonding Flip Chip Bonding", Dominique Numakura, Electronics Packaging Technology, June, 2006
4. "The Latest Technology Trends of the High Density Electronic Circuits", Dominique Numakura, Denshi Zairyo, the Special Edition of Jisso Guidebook, July, 2005.
5. "Global Market and Technical Trends of the Flexible Circuit Industry" Robert Turunen and Dominique Numakura, TPCA Journal, No. 32, 2006.
From the Major Industry Magazines
1. "High Frequency Materials: Setting the Pace for Lead-free Processing", Art Aguayo and Michael Kuszaj, CircuiTree, June, 2006.
2. "After the Fire, Catastrophic loss and the value of good contingency planning: One EMS provider's story", Art Rutlecge and Kim Boykin, Circuits Assembly, June, 2006.
3. "Challenges and Laws of Lead-free Cleaning", Tom Forsythe, SMT, June, 2006.
4. "Virtual RF PCB Prototypes", David Morris, Printed Circuit Design & Manufacturing, June, 2006.
5. "Packaging for Improved Thermal Management", Daxi Xiong, "Opto-WLP Technology (Wafer Level Solutions for Optical and Sensor Applications)", Juergen Leib and Vlker Seidemann, "IC and Package Co-design", Darren Maxwell, JohnSovinsky and Curtis Escobar, "Gold Ball Bumping", Mark Greenwell "Pulsed-laser heating for Flip Chip Assembly- A Stress-free Alternative", Thorsten Teutsch, Elke Zakel and Ghassem Azdasht, Advanced Packaging, May/June, 2006.
6. "An Outlook on the Evolution of Mobile Terminals: From Monolithic to Modular Multi-Radio, Multi-Application Platforms", Giuseppe Desoli and Enrica Filippi, IEEE Circuits and Systems Magazine, No. 2, 2006.
More Columns from EPTE Newsletter
EPTE Newsletter: Travel to Japan During COVIDEPTE Newsletter: A New COVID Surge in Taiwan?
EPTE Newsletter: COVID-19 PCR Test in Japan
EPTE Newsletter: Japan Failing in Vaccine Distribution
EPTE Newsletter: A Long Trip to the U.S.
EPTE Newsletter: Ten Years After Fukushima
EPTE Newsletter: Taiwan Releases 2020 PCB Production Numbers
EPTE Newsletter: The Printed Circuit Industry in China