-
- News
- Books
Featured Books
- smt007 Magazine
Latest Issues
Current IssueSupply Chain Strategies
A successful brand is built on strong customer relationships—anchored by a well-orchestrated supply chain at its core. This month, we look at how managing your supply chain directly influences customer perception.
What's Your Sweet Spot?
Are you in a niche that’s growing or shrinking? Is it time to reassess and refocus? We spotlight companies thriving by redefining or reinforcing their niche. What are their insights?
Moving Forward With Confidence
In this issue, we focus on sales and quoting, workforce training, new IPC leadership in the U.S. and Canada, the effects of tariffs, CFX standards, and much more—all designed to provide perspective as you move through the cloud bank of today's shifting economic market.
- Articles
- Columns
- Links
- Media kit
||| MENU - smt007 Magazine
Estimated reading time: 3 minutes
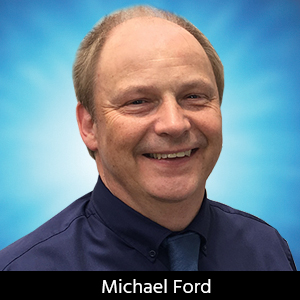
Contact Columnist Form
To Be Lean is to Be Human
The concepts related to Lean thinking continue to be interpreted in different ways by different people. Relating what happens in real life with principles of Lean as applied to manufacturing can serve to demystify the subject, opening up appreciation and acceptance for the adoption of new Lean ideas in a way that is simple and non-threatening.
Let’s take the example of queues, which have evolved naturally as a respectable alternative to a mad, free-for-all scramble. However, a queue for some people is a less-than-humanizing experience. They associate it with being driven like sheep or cattle, wasting precious time. Being stuck in queues is frustrating if the concept of queuing is abused.
For example, the number and frequency of people arriving at a postal office counter is variable, as is the time that each person will spend at the counter, depending on the transaction. The number of people who can be processed at the counter is relatively fixed by the number of counters that are open. If more people come in to the post office than the available counters, the queue grows longer. If fewer people come in, the queue grows shorter or disappears. The most efficient length of the queue is one person. If this was to stay constant, it would ensure that all counters were busy all of the time, at the same time, and that no one is needlessly waiting in line.
If we apply the principles of Lean thinking to the queue, the target should be to keep the queue size to one. The process has to be adjusted to achieve this with an uncontrolled input variable, in this example, the counter staff, to open or close windows dynamically. But rather than applying Lean principles to the post office worker’s job, which is valid, we can look at process optimization from a higher level. Many such levels of any problem can be looked at simultaneously when applying Lean principles. In practice, however, the application of Lean to the different levels of the problem hits an imposed ceiling.
In our example, the resource to work the counters is limited in the short term by the number of counter staff present, unless the manager steps in at peak times. In the longer term, the post office does not want to employ staff if the budget does not allow it and their time will not be fully utilized. Fixed management principles get in the way of process improvement. The cost of having excess counter staff would be more significant to the business than the cost of the longer queues for extended periods throughout the day, the majority of which is borne by customers or the public infrastructure.
Applying this queue theory to a problem with a complexity similar to that of manufacturing is illustrated by a recent trip to the emergency room. The average waiting time to be seen was four hours, which has become normal in the United Kingdom. Instead of taking the four-hour wait, a suggestion was made to go and “take your chances” at a nearby Minor Injury Unit (MIU). Even a 30-minute drive each way sounded better than four hours queuing, so it seemed worth a try. The MIU was totally unlike the emergency room scenario. In, processed, X-rayed, splinted up and out in 20 minutes. Barely time to check any emails. Queue size: one. This was not unusual. The MIU deals with a focused range of issues, mainly suspected broken bones or minor burns. The staff, who are all nurses, simply deal with cases one by one like a simple production line. Even busy times do not seem to put a strain on the operation because the flow is continuous, similar to a high-volume SMT production line.
Editor's Note: This article originally appeared in the April issue of SMT Magazine.
More Columns from The Essential Pioneer's Survival Guide
If It's My Data, I Can Do What I Want, Right?The Essential Pioneer's Survival Guide: One Size Fits All?
Smart for Smart’s Sake, Part 3: Unification & Traceability
Smart for Smart's Sake, Part 2: Material Management
The 'New Face' of Automotive Traceability
Industry 4.0: Who Benefits?
Stop the SMT Conspiracy, Part 2: Abduction
The Future of SMT: Welcome to the 4th Dimension