-
- News
- Books
Featured Books
- design007 Magazine
Latest Issues
Current IssueProper Floor Planning
Floor planning decisions can make or break performance, manufacturability, and timelines. This month’s contributors weigh in with their best practices for proper floor planning and specific strategies to get it right.
Showing Some Constraint
A strong design constraint strategy carefully balances a wide range of electrical and manufacturing trade-offs. This month, we explore the key requirements, common challenges, and best practices behind building an effective constraint strategy.
All About That Route
Most designers favor manual routing, but today's interactive autorouters may be changing designers' minds by allowing users more direct control. In this issue, our expert contributors discuss a variety of manual and autorouting strategies.
- Articles
- Columns
- Links
- Media kit
||| MENU - design007 Magazine
Estimated reading time: 5 minutes
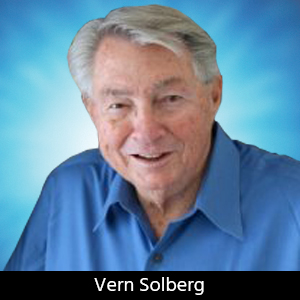
Specifying Lead-Free Compatible Surface Finish and Coating for Solderability and Surface Protection
A majority of the components furnished for electronic assembly are designed for solder attachment to metalized land patterns specifically designed for each device type. Providing a solder process-compatible surface finish on these land patterns is vital; however, selection of the surface finish on the circuit structure, whether plated or coated, can be greatly influenced by the components’ terminal metalization and the specific alloy composition used for the assembly process. Before applying a surface finish on the copper contact sites, however, a thin polymer coating (soldermask) will be applied over the entire surface of the board leaving only the contact sites exposed for soldering.
Soldermask is essential for preventing surface oxidation, contamination or shorting between the closely spaced copper conductors. The soldermask developed for rigid PCB applications is basically a polymer formulation furnished as a liquid for pattern printing or a liquid photoimageable (LPI) version for screen or spray coating. Photoimageable dry film is available as well, requiring surface lamination. LPI soldermask is favored for surface mount applications because it is very thin, flows well around the surface topography and enables precise image definition. Proper curing of the material is critical. When the mask is not fully cured it is susceptible to serious decomposition, crazing and peeling resulting from improperly cured flux chemistries. There is a wide range of curing methods but thermal cure and UV cure materials are most common for one-part formulations. Two-part epoxy-based soldermask materials will cure at room temperature.
Flex circuits and the flexible portion of rigid-flex circuits will require protection as well. These circuits will likely adopt a thin polyimide film as their base. Copper foils laminated or cast onto the base material are photo-patterned and chemically etched to form the final circuit pattern. A common surface protection solution relies on the lamination of a second layer of polyimide film (referred to as the ‘coverlay’) over the copper conductors, a material that is about half the thickness of the base material. Before lamination of the coverlay over the circuit pattern, openings around mounting holes and land pattern features must be provided.
There are several methods for preparing the coverlay film. Holes can be gang punched using dedicated tooling leaving a very clean edge profile. Hard tooling is expensive, but for high-volume applications, most practical. Steel rule punching and mechanical drilling and milling is an option but the edge quality can be lacking. A process that has evolved in recent years uses laser direct imaging (LDI) technology. The system is driven directly from CAD data so no tooling or complex NC programming is necessary. A modified acrylic based photoimageable dry film coverlay material is also available. The supplier (DuPont) claims it is well suited for both single- and double-sided flex circuit applications—applications that typically require fine-line resolution along with bend and crease flexibility. A liquid photoimageable coverlay material is also available. The material is specifically engineered for flexible circuits. It is halogen-free and meets RoHS, UL 94-V0, and NASA outgassing specifications. The manufacturer (Technic) claims the material exhibits “superior flexibility and excellent resolution” and it is a cost effective substitute for the traditional polyimide films. Although the material may be more economical than prefabricated polyimide coverlay, physical robustness must be evaluated for specific applications.
With regard to component terminal finish, manufacturers, in compliance with the RoHS directive, are supplying both active and passive devices with Pb-free surface plating. Solder ball or bump contacts on array-configured devices also use a compliant alloy. The alloys used for plating leads and terminals are pure tin or a tailored tin alloy with the addition of a small percentage of bismuth, nickel or copper alloys. On the other hand, alloy compositions furnished on array-configured devices can vary a great deal. Although they too will be composed primarily of pure tin, the addition of small amounts of silver, copper, bismuth, antimony and nickel alloys may be added to meet some requirement established by the manufacturer. A majority of these array-packaged components will rely on one of the so called ‘SAC’ alloys, a composition made up primarily with tin (Sn) as the base alloy and small amounts of silver (Ag) and copper (Cu). The solder material selected for assembly will likely be one of the SAC alloy compositions as well but modified variations may be considered for more environmentally stressful applications.
Although Pb-free ‘hot air solder leveling’ (HASL) over the etched copper land pattern features remains a predominant finishing technique, electroless plating combined with immersion plating processes are widely used as well. The Pb-free HASL process requires the momentary immersion of the circuit boards into a molten vessel of a SAC alloy and then removing any excess solder build-up by directing a high velocity stream of hot air across the surface of the board (hot air solder level process).
The most common electroless/immersion process (ENIG) begins with a nickel deposition over the copper to act as an oxidation barrier. Following the primary electroless Ni plating step, the circuit is immersed into a heated solution containing the secondary alloy, commonly gold (Au) to maintain solderability of the nickel surface. Immersion plating (without nickel) can be applied directly over bare copper as well. The alloys typically selected for immersion plating on copper are tin (Sn) or silver (Ag). All of these immersion-plating finishes support Pb-free surface mount solder processes but the thin coatings will degrade over time, somewhat dependent on the environment where the circuits will be stored prior to assembly.
As an alternative to alloy plating on copper, many have found that coating the surface with an organic surface preservative (OSP) is preferred. This material can be applied using the immersion technique or spray coated. OSP is a water-based organic compound that selectively bonds to only the copper not covered by soldermask, providing a thin protective layer over the copper. Unlike the alloy finishes noted above, the OSP material is considered environmentally innocuous. On the negative side, shelf life for solderability will be somewhat limited and post assembly test fixture probe contact may be compromised. But, unlike the immersion alloys, any compromised OSP coatings can be chemically stripped from the copper to enable re-coating with fresh material (and that’s a good thing.)
More Columns from Designer's Notebook
Designers Notebook: Basic PCB Planning Criteria—Establishing Design ConstraintsDesigners Notebook: Layer Stackup Planning for RF Circuit Boards
Designers Notebook: Addressing Future Challenges for Designers
Designers Notebook: Impact of Advanced Semiconductor Packaging on PCB Stackup
Designers Notebook: Implementing HDI and UHDI Circuit Board Technology
Designer's Notebook: Heterogeneous Integration and High-density SiP Technologies
Designers Notebook: PCB Design and IPC-CFX for Assembly Automation
Designer’s Notebook: What Designers Need to Know About Manufacturing, Part 2