-
- News
- Books
Featured Books
- design007 Magazine
Latest Issues
Current IssueAll About That Route
Most designers favor manual routing, but today's interactive autorouters may be changing designers' minds by allowing users more direct control. In this issue, our expert contributors discuss a variety of manual and autorouting strategies.
Creating the Ideal Data Package
Why is it so difficult to create the ideal data package? Many of these simple errors can be alleviated by paying attention to detail—and knowing what issues to look out for. So, this month, our experts weigh in on the best practices for creating the ideal design data package for your design.
Designing Through the Noise
Our experts discuss the constantly evolving world of RF design, including the many tradeoffs, material considerations, and design tips and techniques that designers and design engineers need to know to succeed in this high-frequency realm.
- Articles
- Columns
- Links
- Media kit
||| MENU - design007 Magazine
Resins: Cutting Through the Technical Jargon
August 21, 2017 | Alistair Little, ElectrolubeEstimated reading time: 2 minutes
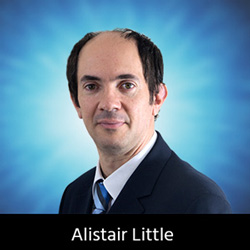
You only have to visit my company’s website to find out that resins come in many forms, with a list of properties that would challenge even a chemist graduate. Well, I do appreciate that most PCB manufacturers have little time to dwell on the subtleties—they just want a resin that will do the job. But with so many products on offer, how do you find time to wade through the jargon, make your choice and be confident that it will perform as expected?
Unquestionably, product detail is important to the user and will be his or her initial guide to making an appropriate choice; however, this month, I’m going to cut through some of the more heavy-going tech-speak, taking a few of my customers’ more frequently asked questions about resins to try to help you refine your selection process. There’s a lot of ground to cover, but for the purposes of this column, let’s concentrate on the PCB’s operating environment, caring for the components that are to be encapsulated, and the special needs of applications like LED lighting and RF systems.
Q. What exactly constitutes “general purpose” protection? Can we take this to mean that a general-purpose resin will meet most environmental conditions, or should we be more cautious if the operating environment is a little more challenging?
A. “General purpose” means that the resin offers good protection against the effects of temperature and humidity over a broad range, as well as providing good resistance to a wide range of chemicals. They also provide protection against vibration and shock, but when it comes to making a choice, you will need to be specific about the resin chemistries—polyurethane or epoxy—as they differ in terms of the types of protection they offer. In general, polyurethanes are better at protecting against vibration/cyclic mechanical shock and thermal cycling within an operating temperature range, as they retain their flexibility over their working life. Epoxies, on the other hand, can tolerate higher operating temperatures than polyurethanes, but they are more rigid and brittle when cured. While they are able to withstand higher mechanical shock, they are not as effective under conditions of high vibration or cycling shock.
Q. What are the main parameters to consider when making a resin selection and what pitfalls should I look out for?
A. The size and geometry of a PCB assembly are important parameters to consider before you choose an encapsulation/potting resin. Size will dictate the required useable life and gel time of a two-part resin, and it will also have quite a big impact on cure time.
Usable life and gel time data are typically calculated on a 100g mix size at room temperature (20-23°C). Short gel times are good for rapid turnaround of units, but may cause problems by allowing air to be released; long gel times, on the other hand, can extend production cycle times and introduce bottlenecks into the manufacturing process.
It is important to note here that very small volumes of resin will take longer to cure and special care should be taken to ensure that the correct mix ratio is maintained. In the case of larger volumes of resin, while the cure times will be reduced, the user must consider the corresponding rise in temperature of the resin/hardener mix, the “exotherm,” which may be high enough to damage vulnerable components. Epoxy resins are much more exothermic than polyurethanes.
To read this entire column, which appeared in the July 2017 issue of The PCB Design Magazine, click here.
Suggested Items
Intervala Hosts Employee Car and Motorcycle Show, Benefit Nonprofits
08/27/2024 | IntervalaIntervala hosted an employee car and motorcycle show, aptly named the Vala-Cruise and it was a roaring success! Employees had the chance to show off their prized wheels, and it was incredible to see the variety and passion on display.
KIC Honored with IPC Recognition for 25 Years of Membership and Contributions to Electronics Manufacturing Industry
06/24/2024 | KICKIC, a renowned pioneer in thermal process and temperature measurement solutions for electronics manufacturing, is proud to announce that it has been recognized by IPC for 25 years of membership and significant contributions to electronics manufacturing.
Boeing Starliner Spacecraft Completes Successful Crewed Docking with International Space Station
06/07/2024 | BoeingNASA astronauts Barry "Butch" Wilmore and Sunita "Suni" Williams successfully docked Boeing's Starliner spacecraft to the International Space Station (ISS), about 26 hours after launching from Cape Canaveral Space Force Station.
KIC’s Miles Moreau to Present Profiling Basics and Best Practices at SMTA Wisconsin Chapter PCBA Profile Workshop
01/25/2024 | KICKIC, a renowned pioneer in thermal process and temperature measurement solutions for electronics manufacturing, announces that Miles Moreau, General Manager, will be a featured speaker at the SMTA Wisconsin Chapter In-Person PCBA Profile Workshop.
The Drive Toward UHDI and Substrates
09/20/2023 | I-Connect007 Editorial TeamPanasonic’s Darren Hitchcock spoke with the I-Connect007 Editorial Team on the complexities of moving toward ultra HDI manufacturing. As we learn in this conversation, the number of shifting constraints relative to traditional PCB fabrication is quite large and can sometimes conflict with each other.