-
- News
- Books
Featured Books
- pcb007 Magazine
Latest Issues
Current IssueInventing the Future with SEL
Two years after launching its state-of-the-art PCB facility, SEL shares lessons in vision, execution, and innovation, plus insights from industry icons and technology leaders shaping the future of PCB fabrication.
Sales: From Pitch to PO
From the first cold call to finally receiving that first purchase order, the July PCB007 Magazine breaks down some critical parts of the sales stack. To up your sales game, read on!
The Hole Truth: Via Integrity in an HDI World
From the drilled hole to registration across multiple sequential lamination cycles, to the quality of your copper plating, via reliability in an HDI world is becoming an ever-greater challenge. This month we look at “The Hole Truth,” from creating the “perfect” via to how you can assure via quality and reliability, the first time, every time.
- Articles
- Columns
- Links
- Media kit
||| MENU - pcb007 Magazine
Estimated reading time: 3 minutes
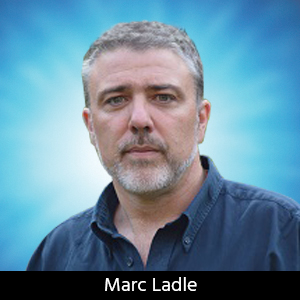
Ladle on Manufacturing: Fabricating for Signal Integrity
Signal integrity! In a world which is increasingly high-speed and digital, the chemical-dependent and mainly analogue-controlled world of PCB manufacturing is not always a comfortable partner.
In theory, the electronic performance of each PCB design is protected by the tolerances and material specification stated in the design package, but the further you proceed towards the limits of technical product performance, the more difficult it is to ensure you will get a perfect result.
Start with your base material. The copper thickness may be stated as 35 microns on the delivery paperwork but what is the real thickness of the copper? A lot of companies use a simple resistance-based thickness check to make sure they are using the right thickness but that will not tell you if you are starting with 35 microns or if the actual thickness is more like 33 microns. Copper is a relatively expensive commodity, and the process for foil production can be pretty accurately controlled. This means that material suppliers may use the allowed tolerance to their advantage by keeping the foil thickness closer to the lower limit of thickness.
Now let us consider a batch of 50 production panels passing through the inner layer process. Pretty early in the process you are going to have to clean the surface of the material to ensure your dry film photoresist will stick to the surface. Cleaning may be using an abrasive brush or chemical cleaning but either way you are reducing the copper thickness further.
Production processing is not a perfect science and reprocessing of material sometimes happens. Let’s say the dry film had a wrinkle on the surface. In this case the material cannot be used unless the film is stripped and then the panel has to pass again through the surface cleaning process and be re-laminated with dry film. In the process, we lose a little bit of extra copper thickness which then means one of our production panels is a little different from the rest with regard to the remaining copper thickness.
The etching process then removes the unwanted copper leaving the desired line width on the PCB. Again—life is not perfect—there is always some variation, as fresh etch solution is usually dosed into the machine in pulses so the etch rate is not the same from one panel to the next. Our panel which already has a little less thickness than the others in the batch is a potential worst case as it started with less copper so would etch just a few percent faster than the others, meaning the final track width will also be slightly thinner than the other panels. Poor working practice may mean that an under-etched panel is re-processed through the etch, which removes the unwanted copper but also takes a little more of what should have remained on the track with it.
After stripping the dry film and inspecting the panels, they usually pass through a reducing oxide to roughen the copper surface in preparation for multilayer lamination. The oxide process takes a further skim of copper from both the height and width of the tracks.
There are some fail-safes to try to help us with the above problems. Automatic optical inspection can certainly check for over-etched panels, but in truth the capability is very limited. Nearly every machine is only able to access the width of the top surface of the track which leaves a significant open question about the shape of the sidewalls of the tracks. Undercut of the copper due to over-etching may not be apparent at inspection but it can significantly reduce the cross-sectional area of the conductor. There is also no way to be sure of the actual copper thickness remaining without a destructive microsection being taken—and there is no guarantee that every panel is the same as the next anyway.
To read the full version of this article which appeared in the October 2017 issue of The PCB Magazine, click here.
More Columns from Ladle on Manufacturing
Ladle on Manufacturing: LED UV Cure—Does It Really Work?Ladle on Manufacturing: UV Cure LED Energy Saver
Ladle on Manufacturing: Sharing an Idea for Christmas
Ladle on Manufacturing: Behind the Scenes at productronica 2019
Ladle on Manufacturing: Sunday Afternoon in Dongguan
The Travelling Engineer, Installment 2
Ladle on Manufacturing: VCP—The Future of Plating
Developments in Wet Processing: Beyond Spraying and Dipping