-
- News
- Books
Featured Books
- smt007 Magazine
Latest Issues
Current IssueMoving Forward With Confidence
In this issue, we focus on sales and quoting, workforce training, new IPC leadership in the U.S. and Canada, the effects of tariffs, CFX standards, and much more—all designed to provide perspective as you move through the cloud bank of today's shifting economic market.
Intelligent Test and Inspection
Are you ready to explore the cutting-edge advancements shaping the electronics manufacturing industry? The May 2025 issue of SMT007 Magazine is packed with insights, innovations, and expert perspectives that you won’t want to miss.
Do You Have X-ray Vision?
Has X-ray’s time finally come in electronics manufacturing? Join us in this issue of SMT007 Magazine, where we answer this question and others to bring more efficiency to your bottom line.
- Articles
- Columns
- Links
- Media kit
||| MENU - smt007 Magazine
Estimated reading time: 5 minutes
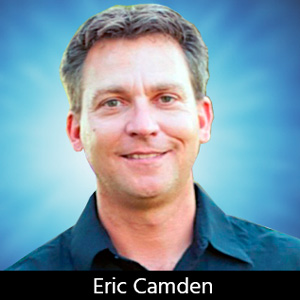
Contamination: The Enemy of Electronics
Welcome to the first installation of “Quest for Reliability.” The goal behind this column is to use my experience at an independent laboratory for over 18 years to help readers understand PCBA reliability issues, and more importantly, prevent suspect conditions in the first place. The laboratory I work in has served every sector of the electronics industry, from oil and gas equipment designed to function miles below the surface of the earth, to aerospace companies and everywhere in between. Not every column will be filled with data, photos, and 8D reports, but they will take a more hands-on approach to the assembly process from the perspective of analytical testing. I hope this column gives you a sneak preview of some of that priceless experience by providing answers to reader questions or shining a light on a problem you didn’t know you had until this point. I was once told, “Experience is something you receive right after you need it,” and this certainly applies to PCBA manufacturing.
This first column will focus on the basics of why contamination is bad for your product. It seems like a simple enough topic, and it is, but the heart of the issue is how to determine what the contamination is and how it was introduced. After you identify these items, you are armed with the information necessary to optimize the process and eliminate the problem. When you look at the overall cleanliness of the product, you must remember that it’s not only what your processing introduces, but also what every process has introduced. Processing steps include, but are certainly not limited to, the following: component manufacturing, PCB fabrication, assembly, and all the handling time in between point zero and the final packaging out the door.
The first and most likely result of excessive amounts of contamination is electrical leakage, which is normally a precursor to electrochemical migration (also known as dendrite growth). These are hard shorts and solid failures that won’t necessarily leave. When looking at an electrical leakage path, three ingredients must be present: conductive residues, voltage differential, and available atmospheric moisture. If you can remove any one of these three pieces, the likelihood of experiencing issues is greatly reduced. In the real world, removing either of the last two ingredients is not a good plan to make money, so let’s assume that power will be applied and the product will indeed be used in some type of atmosphere. Thus, the focus shifts to the level of cleanliness. This is the one thing that can be controlled and monitored before shipping product to the field. Let’s start at the beginning and look at each processing step related to each material choice.
The base for most assemblies is a standard laminate printed circuit board. The old saying is, “Garbage in, garbage out.” This is especially true when processing with a no-clean flux type because there is not a final wash process that can make up for the sins committed upstream, so if you start with a dirty PCB, it will surely get worse before the product is complete. When the topic of PCB cleanliness comes up, a traditional bulk ionic test might be required or supplied. However, without corresponding data from a more sensitive analytical test, such as ion chromatography or surface insulation resistance, the number may supply little more than a false sense of security.
Too many OEMs and CMs look to others to decide what is acceptable and simply want to check a box to show due diligence, but if we have learned anything from our time analyzing field failures, it’s that each manufacturer needs to own their process to build in quality based on the use of a specific product. The main problem is there isn’t a one-size-fits-all number to use because each product has its own set of variables, like voltage, spacing, metallization, and end-use environment. This has led to many companies seeing issues in the field on product that passed the industry accepted test. They don’t know where to turn next, but I digress back to bare board manufacturing.
Many times, PCB fabrication suppliers cut costs by using less than ideal water quality for washing and rinsing the etch and plating residues. This could mean anything from local river water (not a joke, I have seen this) to tap water with unknown amounts of dissolved solids and ionic content. Tap, or river, water has an increased surface tension that can prevent effective rinsing of vias around 8 mil or less on bare boards. This will leave behind processing chemistries that easily facilitate electrical leakage and corrosion. Most often, the only testing performed to supply a certificate of compliance is dimensional information. While this is equally important to the cleanliness data, it only tells you half of the story when looking at incoming bare board quality.
Components go through similar processing steps as bare boards. Both have metallization over a base metal and cleaning steps that include harsh chemistries that can induce issues in the field. When large enough amounts of the plating chemistries are left on the metalized finish, corrosion can propagate without additional moisture or voltage. These two factors can expedite the corrosion but are certainly not required.
After the bare board and components are chosen, they are assembled together using harsh processes that include aggressive flux chemistries and soldering temperatures, sometimes over 250°C. This is the step that has the most influence on the quality of the final product. Active flux residues are chief among processing residues and come from a lot of individual soldering processes. When using water soluble fluxes, any residue left behind will be conductive and corrosive. It isn’t as easy to determine the ionic activity level when using a no-clean flux. By design, no-clean flux residue is left behind and assumed to be near benign after thermal excursion, but that’s not always the case. Throw in the heavily requested aqueous cleaning of no-clean flux and you have yet another contributor of contamination.
The thinking behind the request to clean is well intentioned, but without knowledge of how no-clean fluxes work, the request can prove detrimental to quality. The reason behind this is when the cleaning process isn’t 100% effective, the protective outer shell is removed and material that was intended to be bound will instead be exposed and easily absorb moisture. Think of it as ripping off the bandage and leaving the wound exposed to the elements.
So far, the information I have given only scratches the surface when discussing process residues, and I haven’t discussed testing options at all. There are lots of choices to be made when building a PCBA, and within each of those choices, there are a lot of ways to do it wrong. In the end, the idea behind this column is to learn from others’ mistakes. It’s a whole lot less expensive.
Eric Camden is a lead investigator at Foresite, Inc.
More Columns from Quest for Reliability
Quest for Reliability: Here We Go (Virtual) AgainQuest for Reliability: Put Your Operators in the Driver’s Seat
Quest for Reliability: What’s Lurking in the Shadows?
Quest for Reliability: Reliability Starts at the Bottom
Quest for Reliability: Correlating COVID-19 With Reliability?
Quest for Reliability: Big Trouble Comes in Tiny Packages
Quest for Reliability: New Solder, Same Old Testing
Quest for Reliability: Improving Reliability for Free